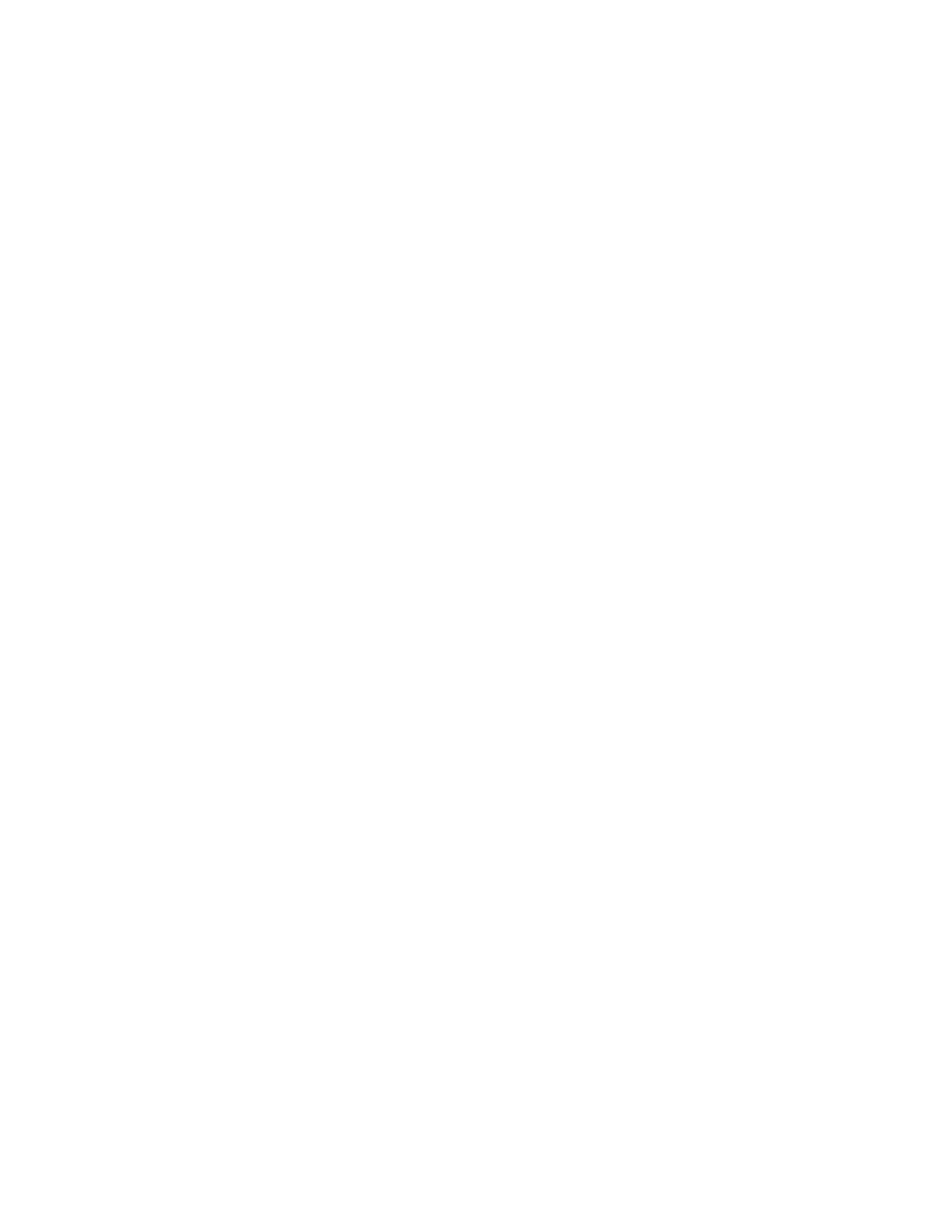
iv
d'un point très chaud luminescent. Ce modèle a produit une flamme sujette à une extinction
rapide et ne semble pas être approprié pour les simulations numériques de la micro
combustion. En outre, l’utilisation d’une cinétique chimique à une équation globale semble
déterminer la température initiale applicable à la fois à la zone d'écoulement de fluide et
aux parois du micro réacteur, ce qui favorise l’ignition de la combustion du pré mélange.
Une question clé de recherche en combustion est la réduction des émissions nocives,
cette question est posée ici dans le cas de la micro combustion. Une micro flamme pré
mélangée méthane/air a été simulée avec une cinétique chimique simplifiée à quatre
équations de Jones et Lindstedt. De plus, le mécanisme de cinétique chimique à trois
équations permettant de décrire la formation du NO thermique a été intégré au code
Comsol 4.2a décrivant le processus de production et de disparition des espèces chimiques
majoritaires. Les simulations effectuées dans les conditions stœchiométriques et de
mélange pauvre avec des ratios équivalents égaux à 0.9 et 0.7, montrent que le modèle de
cinétique chimique de Jones et Lindstedt permet d’obtenir une flamme stable avec des
températures de l’ordre de 2000K, comparables à celles obtenues avec une cinétique
chimique détaillée rapportées dans la littérature. On note aussi que la richesse du mélange
influence la position de la micro flamme. Elle se forme à l’entrée du micro réacteur pour
ф=1 et ф=0.9, mais est déviée au centre du micro réacteur avec ф=0.7. La production du
dioxyde de carbone (CO2) varie avec la richesse du mélange. Elle est maximale pour ф=1
et de l’ordre de 250 ppm, inférieure à celle du seuil exigée pour un air respirable. Quant au
monoxyde de carbone (CO), il ne se retrouve pas dans les produits de combustion du fait
des températures élevées des produits de combustion dans les trois cas de figure. Le
monoxyde d’azote (NO) se retrouve en quantité minime dans les produits de combustion et
a une concentration inférieure à 1ppm. Cependant, on remarque que sa production est