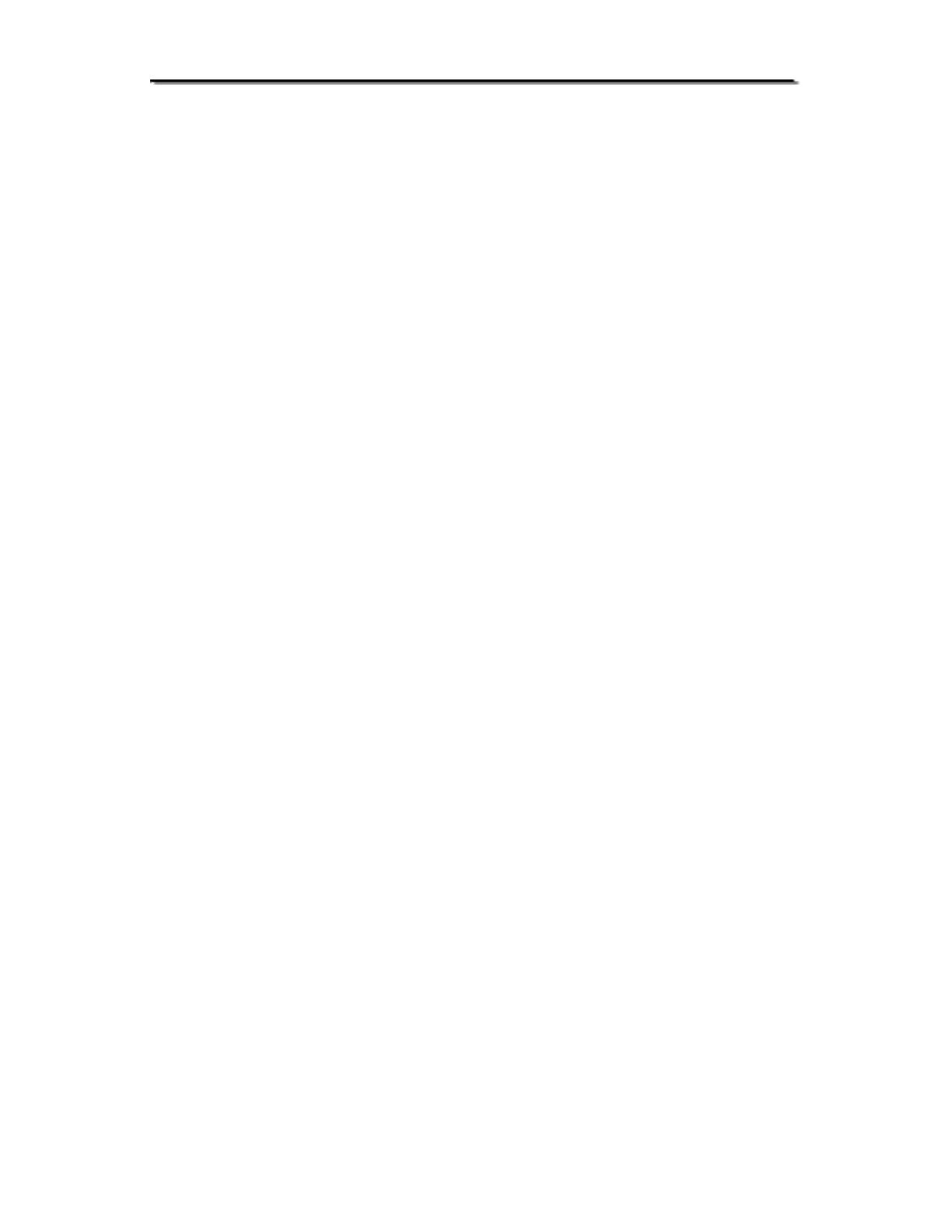
Table des matières
- 2 -
1.3. COMPOSITION ............................................................................................................................ - 72 -
1.4. DOMAINES D’APPLICATION ........................................................................................................ - 76 -
2. MISE AU POINT DE PROCEDES PROPRES...............................................................- 79 -
2.1. SYNTHESE DE L’ACETATE D’ISOAMYLE...................................................................................... - 79 -
2.1.1. Estérification : Etude bibliographique ............................................................................- 79 -
2.1.2. Estérification de l’acide acétique ....................................................................................- 82 -
2.1.3. Estérification de l’anhydride acétique sans catalyse.......................................................- 85 -
2.1.4. Estérification de l’anhydride acétique en présence de catalyseur...................................- 86 -
2.1.5. Evaluation de l’intérêt environnemental..........................................................................- 87 -
2.2. SYNTHESE DE L’ISOVALERATE D’ETHYLE .................................................................................. - 89 -
2.2.1. Oxydation des alcools : Etude bibliographique...............................................................- 89 -
2.2.2. Synthèse de l’acide isovalérique......................................................................................- 96 -
2.2.3. Evaluation de l’intérêt environnemental des réactions d’oxydation..............................- 103 -
2.2.4. Synthèse de l’isovalérate d’éthyle par estérification .....................................................- 103 -
2.3. SYNTHESE DU CARBONATE D’ISOAMYLE ET DE METHYLE........................................................ - 108 -
2.3.1. Le carbonate de diméthyle.............................................................................................- 108 -
2.3.2. Méthoxycarbonylation : Etude bibliographique............................................................- 115 -
2.3.3. Carbonatation de l’alcool isoamylique..........................................................................- 117 -
2.3.4. Evaluation de l’intérêt environnemental et économique ...............................................- 123 -
2.4. SYNTHESE DE L’ETHER D’ISOAMYLE ET D’ETHYLE .................................................................. - 124 -
2.4.1. Ethérification : Etude bibliographique..........................................................................- 124 -
2.4.2. Déshydratation de l’alcool isoamylique et de l’éthanol ................................................- 126 -
2.4.3. O- méthylation de l’alcool isoamylique par le carbonate de diméthyle ........................- 127 -
2.4.4. Réaction de Williamson.................................................................................................- 130 -
2.4.5. Evaluation de l’intérêt environnemental........................................................................- 131 -
3. SELECTION DU BIOSOLVANT LE PLUS ADAPTE POUR LES VERNIS A ONGLES ......- 133 -
3.1. TESTS DE SOLUBILITE ET DE COMPATIBILITE............................................................................ - 133 -
3.2. ETUDE DU TEMPS DE SECHAGE................................................................................................. - 134 -
3.2.1. Critère primordial de sélection d’un solvant de vernis à ongles...................................- 134 -
3.2.2. Influence de la nature du solvant sur le temps de séchage du vernis ............................- 135 -
3.3. THEORIE DE HANSEN ............................................................................................................... - 137 -
3.3.1. Description de la théorie ...............................................................................................- 137 -
3.3.2. Description des paramètres de solubilité de Hansen.....................................................- 139 -
3.3.3. Détermination expérimentale des paramètres de Hansen .............................................- 140 -
3.3.4. Paramètres de solubilité de Hansen d’un mélange de solvants.....................................- 145 -
3.3.5. Conclusion.....................................................................................................................- 147 -
3.4. ASPECTS ECONOMIQUES........................................................................................................... - 147 -
4. CONCLUSIONS ...................................................................................................- 150 -
CHAPITRE III - PLASTIFIANTS D’ORIGINE VEGETALE ................................ - 153 -
1. DEMARCHE DE SUBSTITUTION DES PLASTIFIANTS .............................................- 155 -
1.1. ROLE DES PLASTIFIANTS DANS UNE FORMULATION.................................................................. - 155 -
1.2. PLASTIFIANTS D’ORIGINE PETROCHIMIQUE .............................................................................. - 155 -
1.3. IDENTIFICATION DES MOLECULES CIBLES................................................................................. - 158 -
2. STRATEGIES DE DEVELOPPEMENT D’AGENTS PLASTIFIANTS .............................- 159 -
2.1. HUILES VEGETALES : SOURCE DE CARBONE RENOUVELABLE ................................................... - 159 -
2.2. PREPARATION DES ALCOOLS GRAS A PARTIR DES HUILES VEGETALES...................................... - 160 -
2.3. L’ALCOOL LAURIQUE EN TANT QUE MATIERE PREMIERE.......................................................... - 161 -
2.4. LE GLYCEROL COMME MATIERE PREMIERE.............................................................................. - 162 -
2.4.1. Origine du Glycérol.......................................................................................................- 162 -
2.4.2. Applications et débouchés .............................................................................................- 166 -