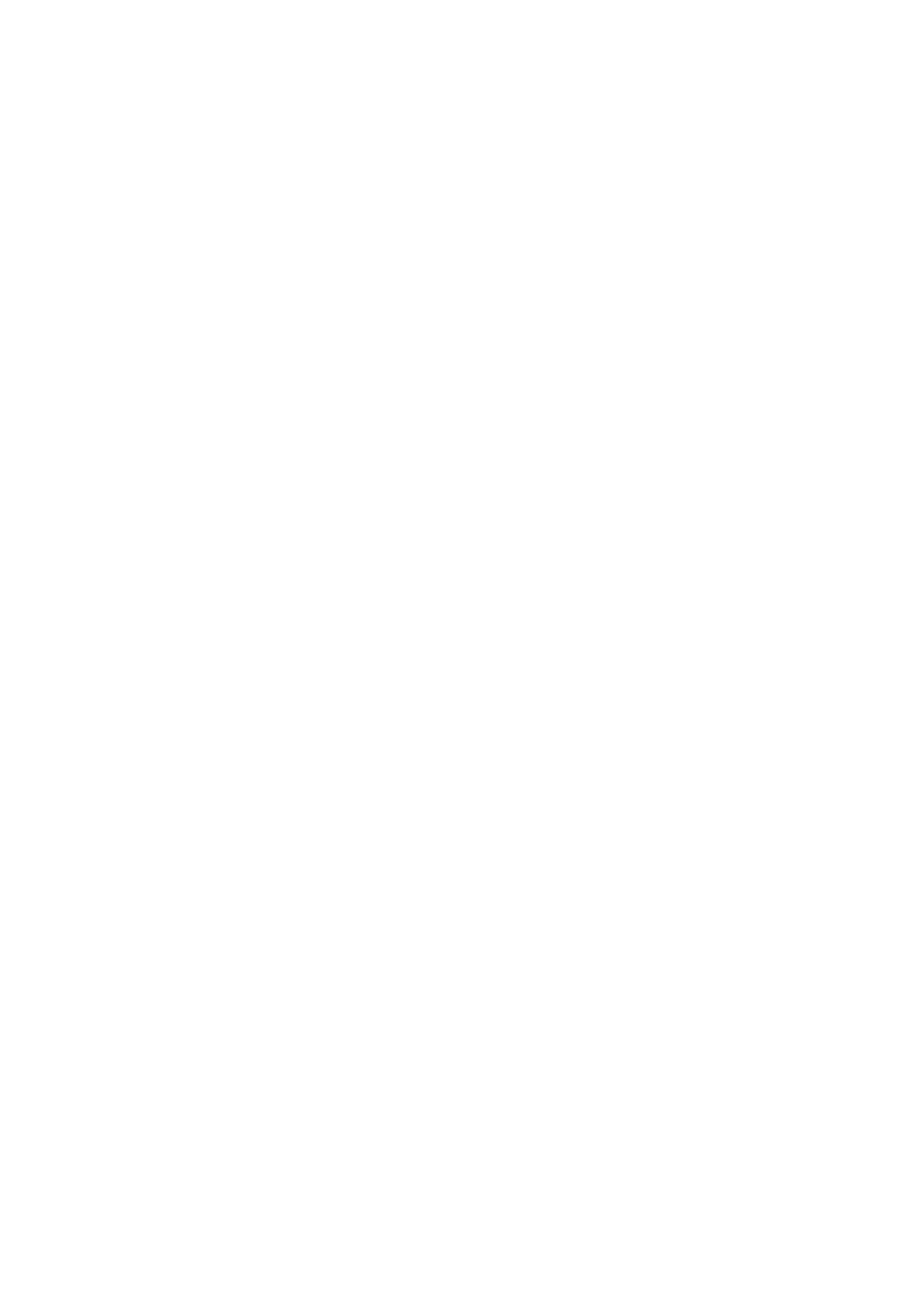
Remerciements
Ce travail de thèse a été réalisé au sein de l'équipe MEMO (Mécanique, Microstructure, Oxydation,
Corrosion) du Centre Inter-universitaire de Recherche et d'Ingénierie des MATériaux (CIRIMAT-UMR
5085, CNRS/UPS/INPT) à l'ENSIACET, en collaboration avec la société TURBOMECA.
J'adresse mes plus vifs remerciements à Rémy Mévrel, Joe W. Quadakkers et John R. Nicholls pour les
heures passées à lire ce manuscrit, parfois dans une langue qui n'était pas la leur, afin de pouvoir juger ce
travail en tant que rapporteurs.
Je remercie Régine Molins pour avoir présidé ce jury et Philippe Lours pour avoir accepté de participer à
mon jury de thèse. Mes remerciements vont également vers André Malié, qui en plus d'avoir participé à
mon jury de thèse, a su se rendre disponible afin de répondre à mes nombreuses questions lors de ces trois
années.
Je tiens à remercier les personnes de TURBOMECA que j'ai côtoyées lors de mes déplacements, en
particulier Fabrice Crabos qui s'est rendu disponible malgré un emploi du temps surchargé.
Je remercie une fois de plus John R. Nicholls qui m'a accueillie pendant trois mois à Cranfield University
pour me faire partager ses nombreuses connaissances sur l'élaboration de systèmes barrière thermique.
J'exprime également toute ma gratitude aux personnes de Cranfield University pour leur accueil fort
sympathique ainsi que pour leur aide à chacune des étapes de fabrication de mes éprouvettes : Kevin,
Marc, Laura, Simon, Tony(s), Christine, Jeff, Andrew, Richard, Sandra, Sharon, etc…
Je tiens à remercier Eve Péré et Jean-Paul Grenet, de l'équipe Chimie Physique (ECP), qui m'ont
régulièrement accueillie à l'IPREM afin de me faire découvrir le monde complexe de la spectroscopie
Raman. Merci pour votre disponibilité et votre gentillesse lors de cette collaboration.
Ce travail de thèse ne serait rien sans trois personnes, à savoir Djar, Aymeric et Daniel que je tiens à
remercier tout particulièrement pour leur implication, leur gentillesse, leur soutien et pour la confiance
qu'ils ont su me témoigner au cours de cette thèse. Merci Djar pour ta sympathie, ta disponibilité ainsi que
tes précieux conseils de microscopiste qui ont apporté beaucoup à ce travail. Merci Aymeric d'avoir
régulièrement décroché le téléphone à 8h00 du matin afin de discuter science mais surtout de m'avoir fait
partager tes connaissances et ceci toujours dans la bonne humeur. Daniel, je ne sais comment te remercier.
Ta patience, ta disponibilité, la transmission de ton savoir et ton soutien, que ce soit au cours de la thèse ou
pour l'après-thèse, m'ont beaucoup apporté et ont très largement contribué à ce travail.
Vient maintenant le moment de remercier toutes les personnes ô combien sollicitées pour des questions
expérimentales et de caractérisation. Un grand merci à Alexandre et à Yannick pour leur disponibilité et
leur sympathie. Merci également à Cédric et à Laure Vendier (du LCC) pour les DRX. Un immense merci
revient à Marie-Christine pour sa gentillesse et sa grande implication dans les analyses MET. Merci aux
baby-sitters des machines, Ronan et Jean-Claude, pour leur aide précieuse notamment sur les
thermobalances et le GBOC. Merci enfin à Helena, qui séjourne régulièrement au laboratoire, pour sa
gentillesse et son aide sur certains essais.