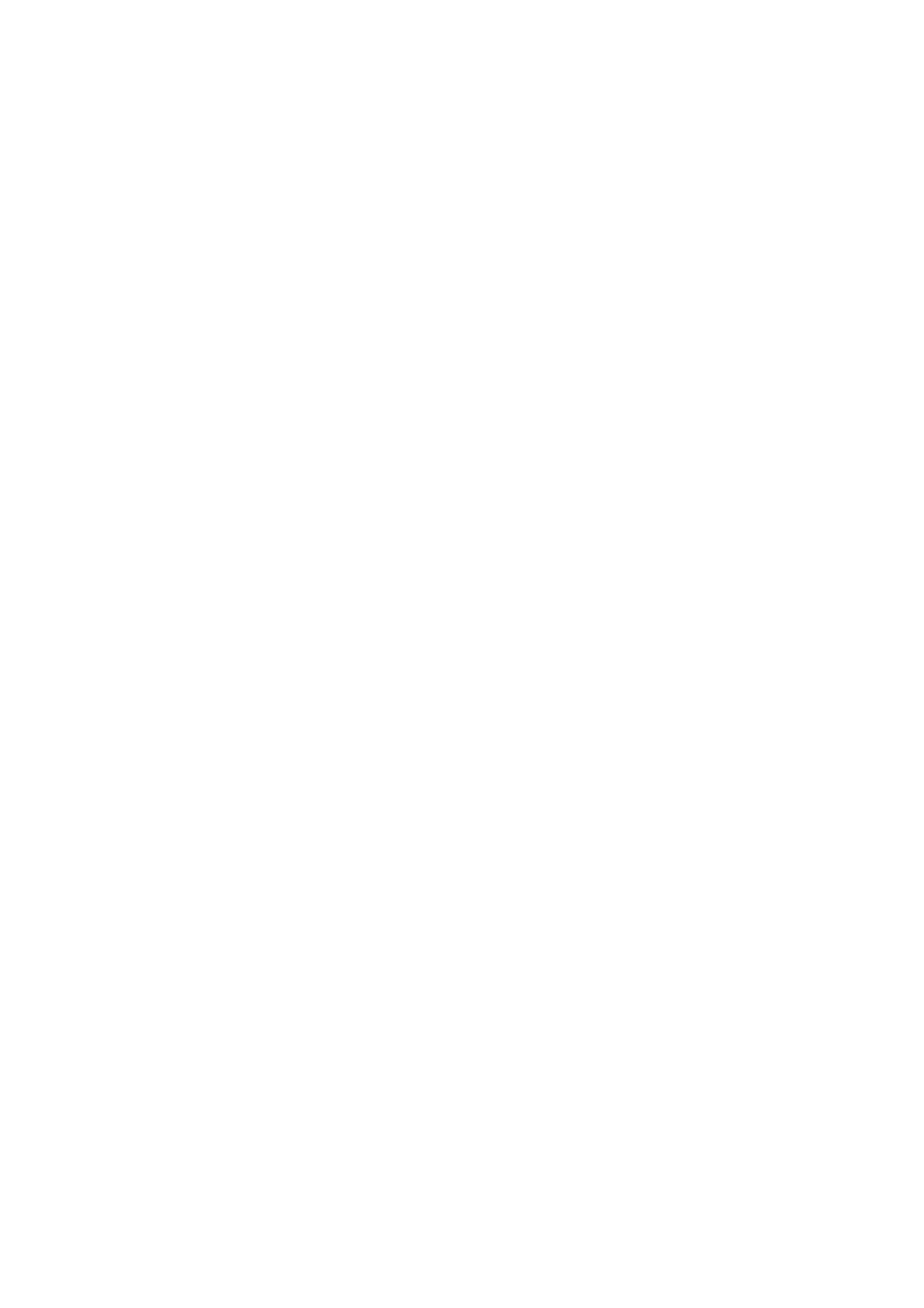
Modélisation semi-analytique par approche énergétique du procédé de
perçage de matériaux monolithiques.
Le but de ce travail est d'analyser et de modéliser les phénomènes ayant lieu lors d'une
opération de perçage de façon à fournir des résultats utilisables pour d'autres modèles d'étude
des outils coupants. Le modèle présenté permet donc d'obtenir, le torseur des actions
mécaniques et également les champs de contrainte et de température pour toutes les surfaces
actives du foret.
La modélisation proposée comprend la modélisation de la géométrie de l'outil ainsi que la
modélisation complète des phénomènes thermomécaniques présents en perçage, incluant, en
outre des phénomènes de coupe, l'influence de l'acuité d'arête et de l'âme du foret. Les
principes de la modélisation utilisés permettront d'adapter ce modèle à de nombreux
matériaux à partir d'un minimum de paramètres.
Les moyens expérimentaux originaux mis en place ont permis d'étudier la validité du modèle.
Grâce à l'étude approfondie qui en a découlée, l'origine des sources d'erreurs a pu être mise en
évidence. Ceci a montré les limitations de la loi de comportement utilisée pour des
applications en usinage.
Les résultats que le modèle permet de déterminer ouvrent de nombreuses perspectives sur
l'étude de la prévision du comportement des outils coupants.
Mots-clés : Perçage, Modélisation analytique, Modèle géométrique, Modèle
thermomécanique, Acuité d'arête, Ame
Semi Analytical modelling with an energetic approach of metal drilling.
The aim of this work is to model the phenomena occurring during a drilling operation in order
to give results that can be used in other models for the study of cutting tools. Beside
mechanical actions, the presented model gives stress and temperature fields on every active
surface of the drill.
The proposed modelling include the geometrical modelling of the tool and the complete
modelling of drilling phenomena, taking into account cutting, tool acuity and the chisel edge.
Modelling principles allows adapting the model to various materials with a minimum input
dataset.
Original experimental setups where used for the study of model validity. It allowed an
extended study that has bring to evidence the causes of errors. This has showed the limitation
of the constitutive law for machining applications.
The data that can be calculated with this model enable numerous perspectives on the prevision
of cutting tool behaviour.
Keywords: Drilling, Analytical modelling, Geometric model Thermomechanical model, Tool
acuity, Chisel
Laboratoire de Génie Mécanique et Matériaux de Bordeaux
IUT Bordeaux I
Domaine Universitaire
33405 Talence Cedex
Laboratoire de Mécanique Physique
Université Bordeaux 1
Domaine Universitaire