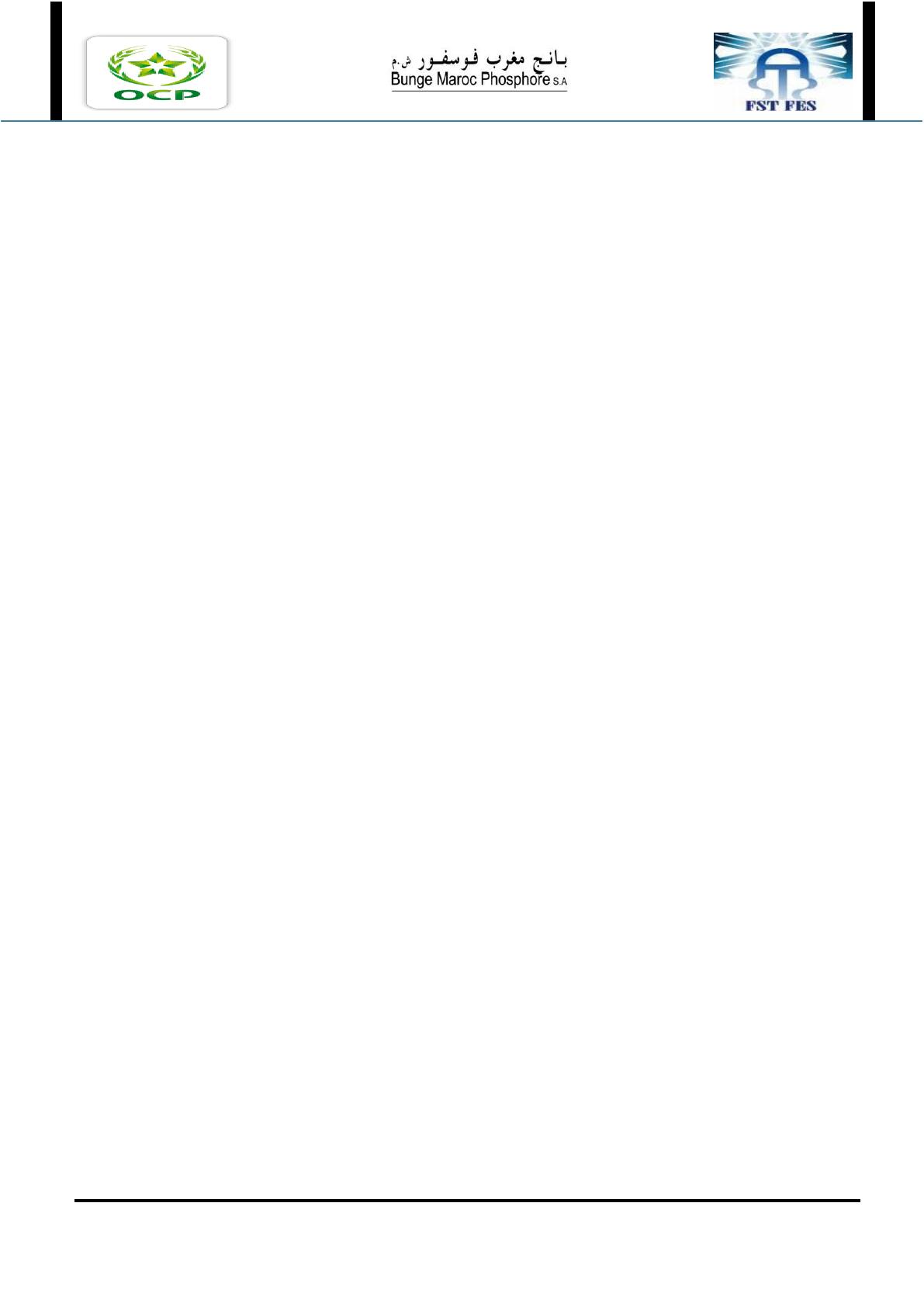
Projet de Fin d’études 5 juin 2012
Figure 3: Les ateliers de production implantés au sein de Bunge Maroc Phosphore ............... 15
Figure 4:organigramme de BMP ............................................................................................... 15
Figure 5:principe de production de l’atelier acide sulfurique ................................................... 18
Figure 6: synoptique de la phase de conversion ........................................................................ 20
Figure 7: unité de traitement des eaux douces .......................................................................... 21
Figure 8: section de manutention et de broyage ........................................................................ 26
Figure 9: Production des engrais MAP et DAP ........................................................................ 30
Figure 10 : le champ magnétique .............................................................................................. 33
Figure 11 : le champ résultant ................................................................................................... 34
Figure 12:Schéma de principe d’une cage d’écureuil ............................................................... 34
Figure 13:Structure générale d’un variateur de vitesse électronique ........................................ 35
Figure 14:les situations possibles d’une machine dans son diagramme couplent vitesse ........ 37
Figure 15:forme de l’alimentation fournie au moteur ............................................................... 40
Figure 16: la tension en fonction de temps ............................................................................... 41
Figure 17:salle BT ...................................................................................................................... 43
Figure 18:tableau intelligent ..................................................................................................... 44
Figure 19:tiroire électrique ....................................................................................................... 45
Figure 20:les constitutions d’un tiroir ....................................................................................... 45
Figure 21:jeux de barre ............................................................................................................. 45
Figure 22:Courbe du courant de démarrage ............................................................................. 48
Figure 23: données de projet ..................................................................................................... 54
Figure 24:type d'installation ...................................................................................................... 54
Figure 25:Données de l'installation ........................................................................................... 55
Figure 26:Régime de fonctionnement ...................................................................................... 55
Figure 27:Résultats .................................................................................................................... 56
Figure 28:diagramme qui résume les types de la maintenance ............................................... 59
Figure 29: diagramme des étapes de la programmation des activités de révision .................. 61
Liste des tableaux
Tableau 1:Fiche technique du groupe OCP ............................................................................... 14
Tableau 2:Types de démarreurs ................................................................................................ 40
Tableau 3:liste des moteurs de la ligne de production 306 ..................................................... 49
Tableau 4: liste des moteurs de la ligne de production 307 .................................................... 49
Tableau 5:liste des moteurs qui nécessite un démarreur électrique ....................................... 49
Tableau 6:cout total d’installation des variateurs de vitesse ................................................... 52
Tableau 7:cout total d'installation des démarreurs .................................................................. 53
Tableau 8:le planning de maintenance préventive ................................................................... 64
Table des matières
Liste des Figures ................................................................................................................................ 4