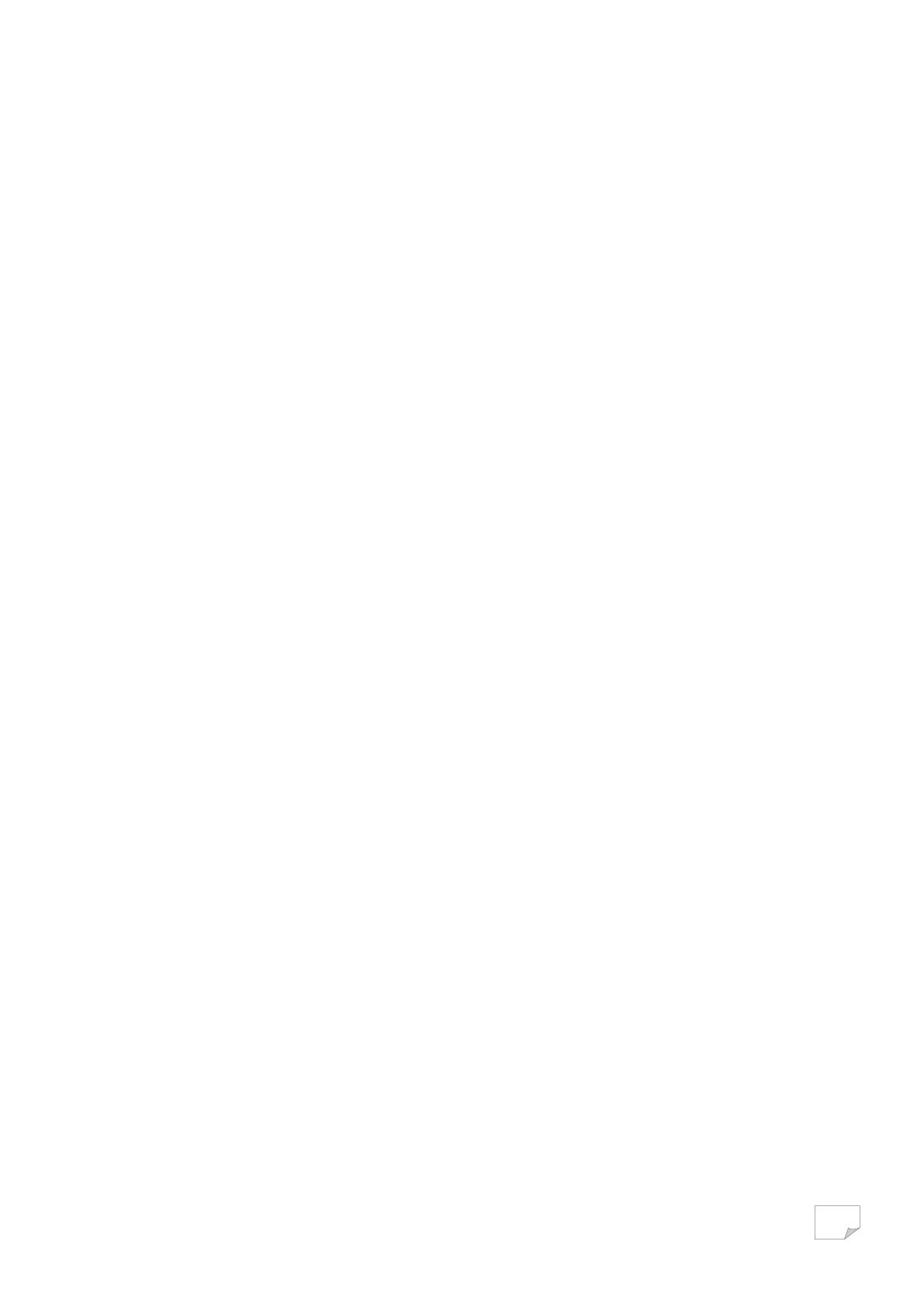
3%
:,,,,,
Résumé
Le but de ce travail est l’étude du comportement de l’acier galvanisé et sa résistance à la
corrosion.
Les investigations par la technique de l’électrochimique, nous ont permis de suivre le
comportement de l’acier nu et galvanisé dans deux différentes solution l’eau douce et le
chlorure de sodium à 3%.
Les résultats obtenus ont montré que le chlorure de sodium à 3% était plus réactif à la
corrosion que la protection par le zinc. Par contre, l’eau douce n’a aucun effet sur l’acier
galvanisé du fait de la passivation de la couche galvanisée par rapport au substrat (acier nu).
On conclu que la protection par le zinc est favorable pour les tubes transportant l’eau douce.
Mots clé : Corrosion, électrochimie, acier, galvanisation, zinc, tube.