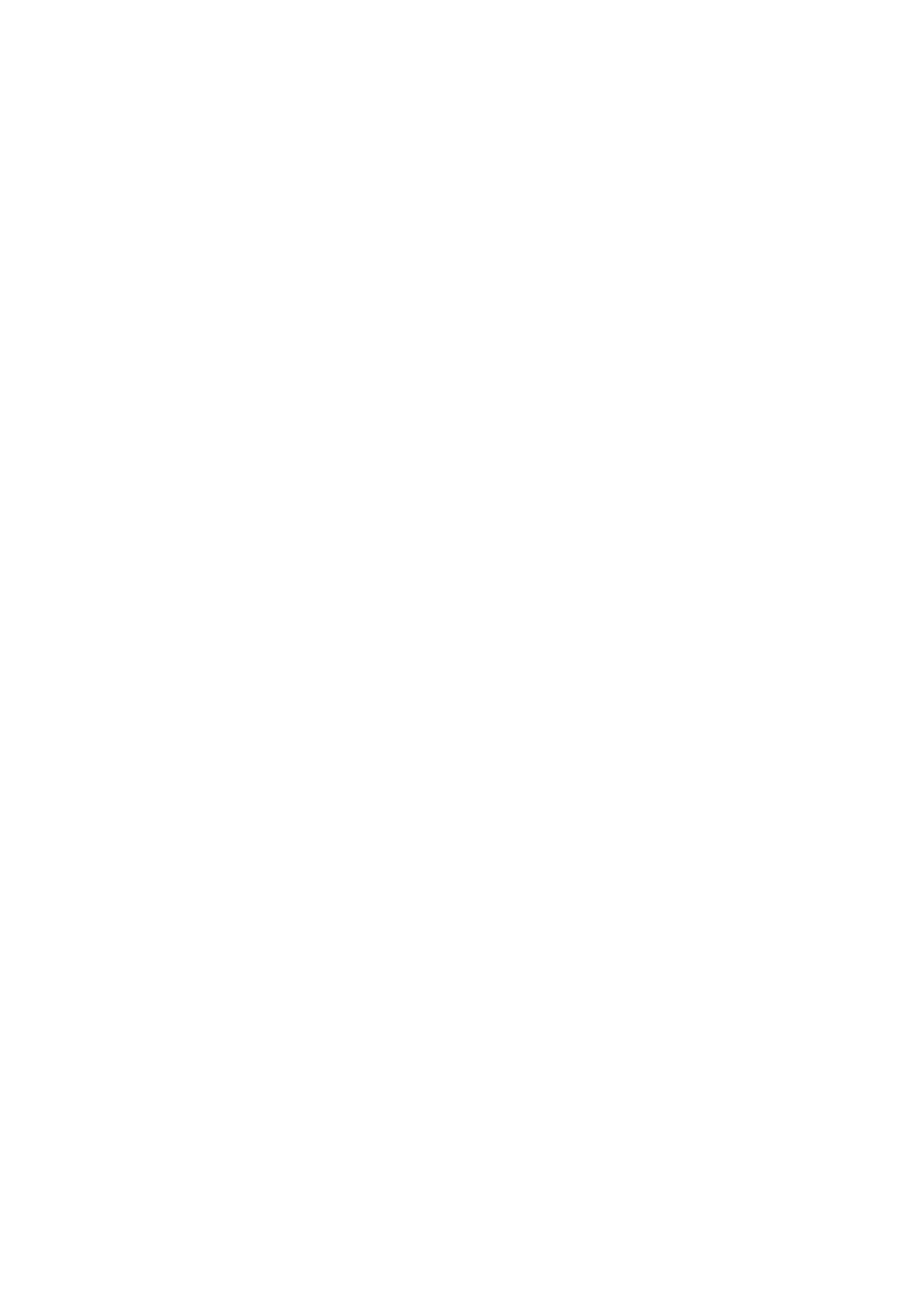
1
REMERCIEMENTS
Je remercie tout d’abord, mes deux grands chefs, M. Didier MAYER et M. Rudolf
METKEMEIJER, pour m’avoir embauchée, encadrée, supportée, laissée grande liberté et
envoyée présenter mes travaux dans différentes contrées (pas trop loin quand même). Vos
connaissances techniques et vos qualités humaines m’ont permis de réaliser cette thèse dans
les meilleures conditions.
Je remercie les membres du jury, M. Christian GLAIZE et M. Kodjo AGBOSSOU,
rapporteurs de ma thèse, ainsi que M. Jean-Christian MARCEL et M. André CLAVERIE,
pour avoir accepté d’évaluer mon travail et pour leurs remarques constructives.
Je remercie ensuite, l’équipe technique du CENERG sans qui une manip’ ne pourrait être
montée. Un merci particulier à Patrick qui sous sa carapace de râleur invétéré, cache un
technicien adorable et efficace. Merci aussi à la joyeuse équipe technique du CEMEF !
Pour finir, je remercie l’ensemble du personnel du CENERG, permanents et étudiants. Plus
particulièrement, mes collègues de bureau, Christine, Marie-Jeanne, Lionel et Michel (hé oui !
même les TM) qui m’ont aidée et supportée au cours de ces 4 ans.
Maintenant, passons aux amis … D’abord les filles, puis les garçons : Estelle, Manue, Val,
Isa, Aurel, Mag, Chris, Sand, Fab, Annie, François, Ju, Thierry, Ben, Christophe, Nico …
Merci pour votre amitié, votre bonne humeur, votre aide et tous les bons moments, passés et
futurs.
Enfin, merci à Mag, Sandra, les parents, Jacky, Léna, les randonneurs, Ombré, …