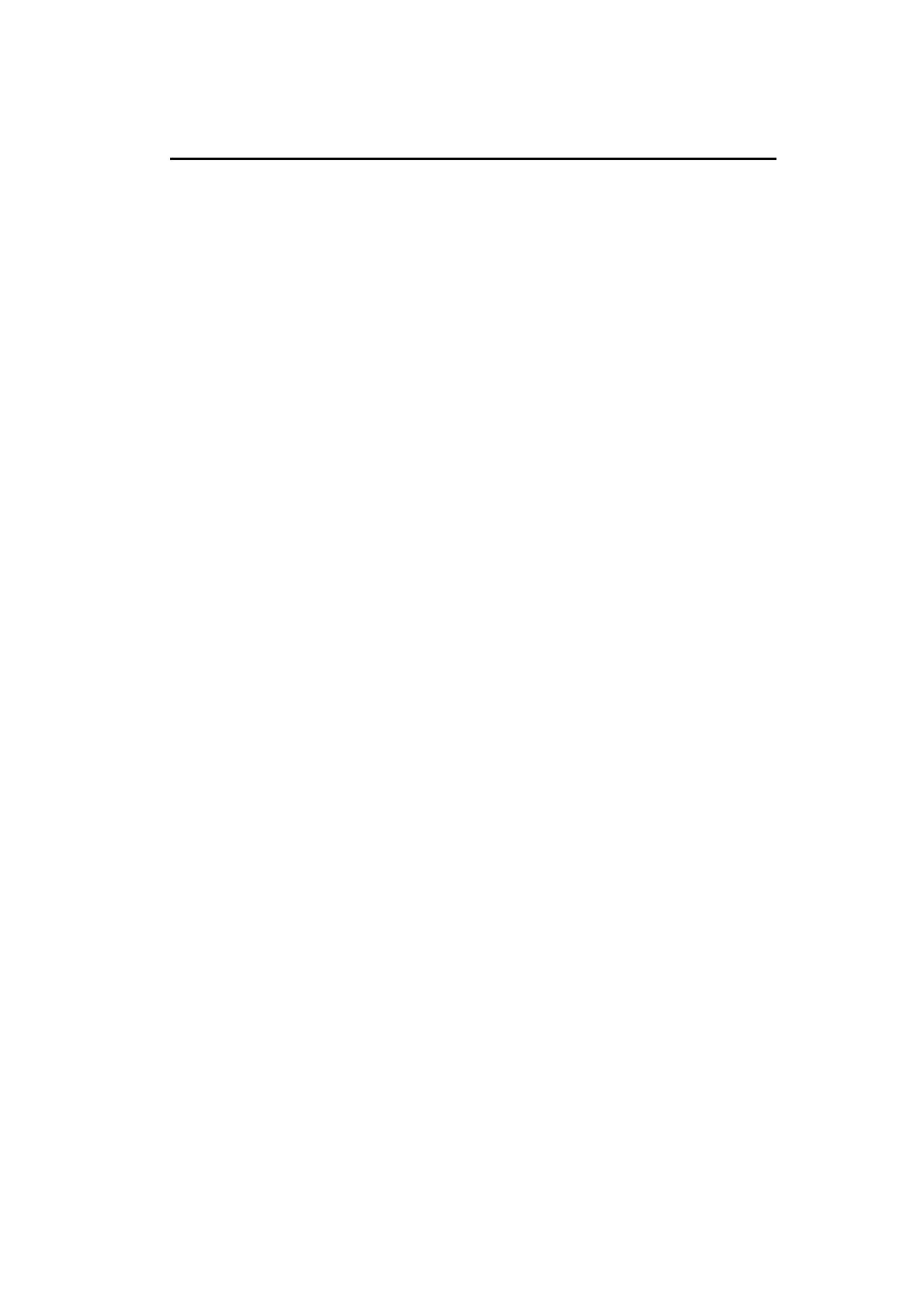
ii
Partie 1 : Photopolymérisation & Matériaux Composites.
Dans la première partie de ce manuscrit sont rassemblées les informations générales
sur les matériaux composites, la technologie de polymérisation UV et son emploi pour
la préparation de composites à matrices polymère.
CHAP. 1 : MATERIAUX COMPOSITES/INTERFACE
1.1 Caractéristiques et propriétés de matériaux composites
1-3
Dans la quête continue pour les performances améliorées, les matériaux traditionnels
sont remplacées de plus en plus par les matériaux composites synthétiques faisant appel
à l’association d’une matrice polymère et d’agents de renforcement comme des charges
particulaires (nanométriques ou micrométriques) et des fibres de renfort comme les
fibres de verre ou de carbone.
Les matériaux composites sont constitués de phases chimiquement différentes sur
une échelle microscopique, séparée par une interface distincte. Le composant qui
constitue la phase continue et présent en plus grande quantité est appelé la matrice. Le
deuxième composant est connu sous le nom de la phase renforçante, ou renforcement,
puisque généralement les propriétés mécaniques de cette phase sont supérieures à celles
de la matrice.
Les paramètres géométriques liés à la phase renforçante (facteur de forme, surface
spécifique, etc.) sont essentiels pour déterminer les caractéristiques des matériaux
composites qui en seront issus.
1.2 Interface/interphase: structure et propriétés
Les propriétés de composites également sont contrôlées par les caractéristiques de
l’interface
1,3,4
, région à deux dimensions (interface) ou plutôt de l’interphase, zone à
trois dimensions (phase intermédiaire aux propriétés spécifiques). Une forte liaison à
l’interface ou via l’interphase entre la matrice et la fibre assure alors le transfert de
charge de la matrice (renforcement) et est une des conditions essentielles pour conduire
à des propriétés de renforcement associées à l’association d’une matrice polymère et
d’un composant de fort comportement élastique comme des fibres ou des charges
particulaires. La résistance à la fracture (choc ou impact, propagation de fissures),