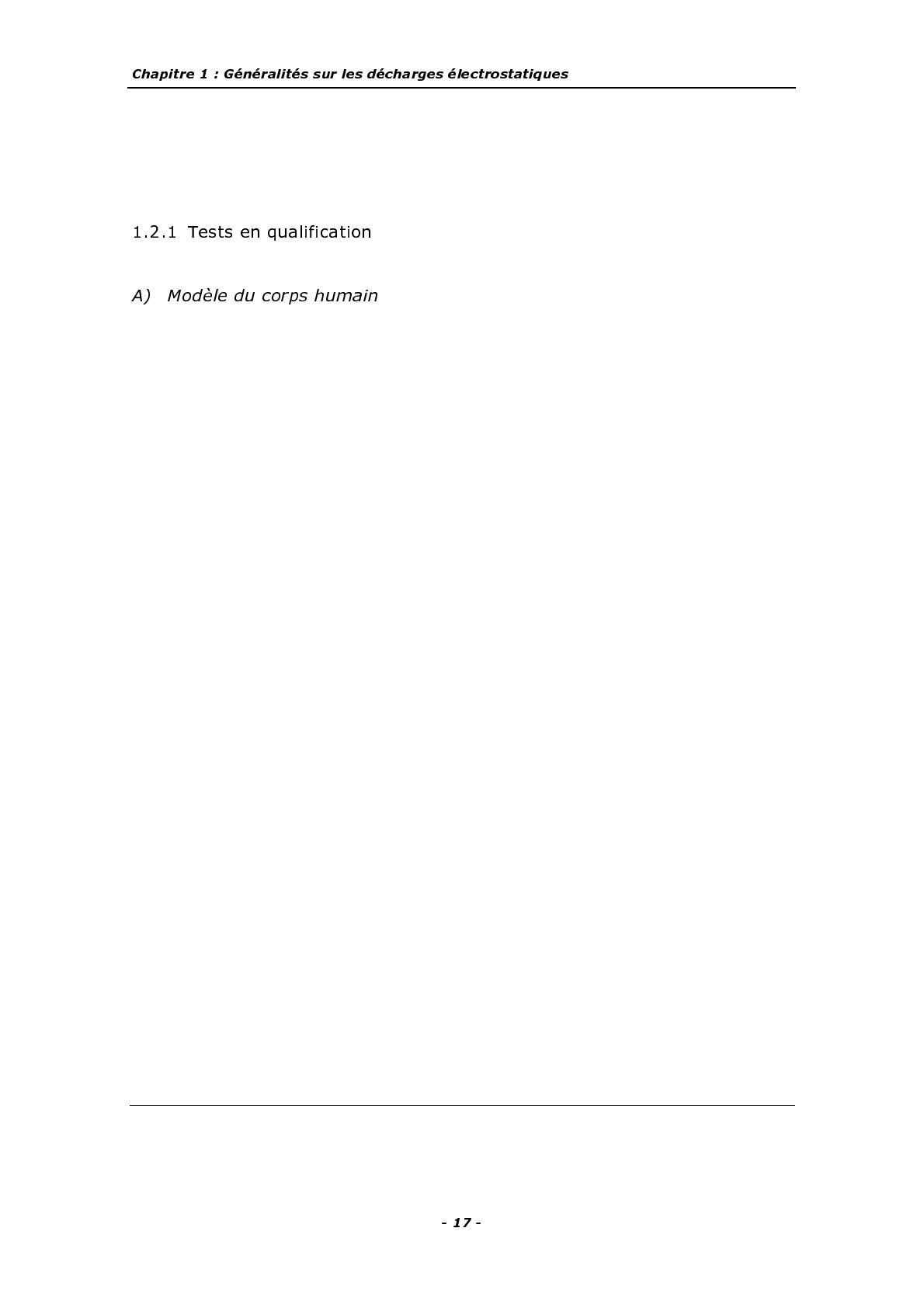
Le modèle du corps humain, HBM (Human Body Model), est le test le plus large-
ment utilisé pour qualifier la tenue des composants aux ESD. Depuis son introduc-
tion dans les années 1980, il a permis de réduire considérablement le taux de dé-
fauts survenus lors de la fabrication puis de l’utilisation des composants.
Le test simule la décharge d’une personne chargée sur un composant électronique.
Le corps de l’opérateur est modélisé par une capacité placée en série avec la résis-
tance de contact de la peau (fonction de la surface de contact de l’opérateur et de
sa résistivité). La sensibilité d’un composant au test HBM est définie par la tension
de charge maximum que le circuit intégré peut supporter sans présenter de dé-
faillance notoire.
La norme HBM, remise à jour en 1998, décrit [AEC98-a][EIAJ97-a][ESD98] :
• les valeurs de la capacité CHBM (100 pF), de la résistance de contact RHBM
(1,5 kΩ) et de l’inductance LHBM (7,5 µH) (cf. Figure 1. 1),
• la forme de l’onde HBM aux bornes d’un court-circuit ou d’une résistance de
500 Ω (cf. Figure 1. 2 et Tableau 1. 1),
• les valeurs maximales de distorsions en courant autorisées1 [LEE99],
• la classification des composants selon leur niveau de tenue aux impulsions
HBM2.
Pour limiter la durée et les coûts des tests HBM industriels, proportionnels au
nombre de broches des circuits, tout en garantissant une certaine reproductibilité
des mesures, il est conseillé de tester sur un échantillon représentatif :
• chaque broche une par une par rapport aux broches d’alimentation,
• chaque broche d’entrée/sortie une par une par rapport aux autres broches
d’entrée/sortie,
1 Les distorsions de courant sont liées aux capacités et inductances parasites présentes dans les testeurs commerciaux.
2 Classe 1 : composant endommagé par une impulsion HBM inférieure ou égale à 2000 V ; classe 2 : composant qui
fonctionne après un test HBM de 2000 V mais qui ne résiste pas à une impulsion de 4000 V ; classe 3 : composant qui
fonctionne après un test HBM de 4000 V.