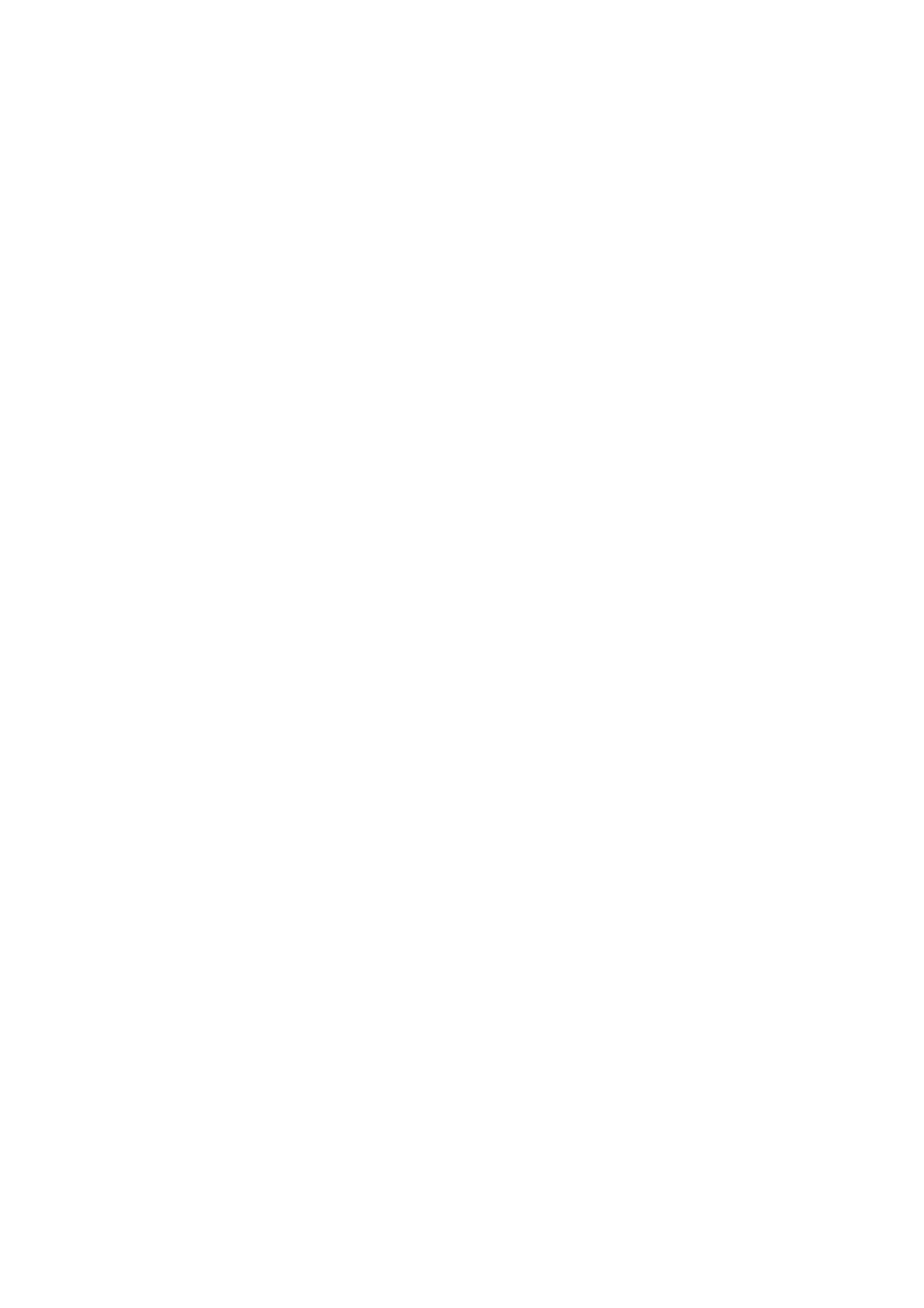
Remerciements
Je remercie tout d’abord Fabrice Casset qui fut mon encadrant au quotidien. De part son expérience sur les
MEMS, Fabrice m’a beaucoup appris, conseillé et soutenu tout au long de la thèse. Je lui en suis très
reconnaissant. Je remercie également Pascal Ancey pour m’avoir accueilli dans son équipe à ST, ainsi que
pour avoir promu mes activités au niveau de l’entreprise. Je remercie Eric Ollier pour m’avoir permis de
réaliser une partie des développements au sein du CEA-LETI. Enfin, je remercie Lionel Buchaillot pour
avoir accepté d’être mon directeur de thèse. Bien que n’étant pas basé dans son laboratoire au quotidien, ce
dernier a assuré un suivi régulier de l’avancement de mes travaux, tout en apportant sa critique scientifique à
tous niveaux. Il a également su soutenir les résultats de mes travaux à leur juste valeur.
Au sein de STMicroelectronics à Crolles, je souhaite remercier toutes les personnes qui m’ont aidé dans les
différentes phases de la thèse, allant de la modélisation à la caractérisation des composants, en passant par la
réalisation technologique. Je pense tout particulièrement à Lorenzo Ciampolini m’ayant formé sur les outils
Synopsys, Stéphane Monfray m’ayant aidé sur la physique des transitors et la technologie SON, Fabienne
Judong, Alexandre Talbot, Delia Ristoiu, Linda Depoyan ou encore Nicolas Loubet sur les développements
technologiques. Je remercie également Nicolas Abelé pour son partage de connaissances sur les résonateurs.
Au sein du CEA-LETI, je souhaite remercier toutes les personnes qui m’ont aidé, principalement au niveau
des réalisations technologiques et de la caractérisation électrique des composants. Je pense tout
particulièrement à Denis Renaud, Stéphan Borel, Pauline Gautier, Rémi Quenouillère, Brigitte Florin en ce
qui concerne les développements technologiques, à Philippe Renaux et Denis Mercier concernant les
caractérisations électriques.
Au sein de l’IEMN, Je remercie les membres du groupe NAM6 pour m’avoir accueilli lors de mes venues à
Lille, et tout particulièrement Bernard Legrand et Marc Fauché pour leur partage de connaissances sur les
résonateurs, ainsi que leur aide précieuse concernant des caractérisations électriques.
Au sein de l’EPFL, je remercie Daniel Grogg et Adrain Ionescu pour m’avoir accueilli dans leur laboratoire
afin de faire les mesures de mes composants en température.
Je remercie mes collègues de travail à STMicroelectronics avec qui j’ai passé de très bons moments durant
ces trois dernières années. Je pense entre autres à Pierre Bar, David Petit, Loic Mourot, Siegfried Dossou,
Perceval Coudrain, Yacine Felk et Syvlain Joblot.
Enfin, je remercie Alain Bossebeouf et Adrian Ionescu pour avoir accepté de repporter ce travail et je
remercie tous les autres membres du jury pour avoir accepté d’examiner le travail effectué.
Thèse de Cédric Durand, Lille 1, 2009
© 2010 Tous droits réservés.
http://doc.univ-lille1.fr