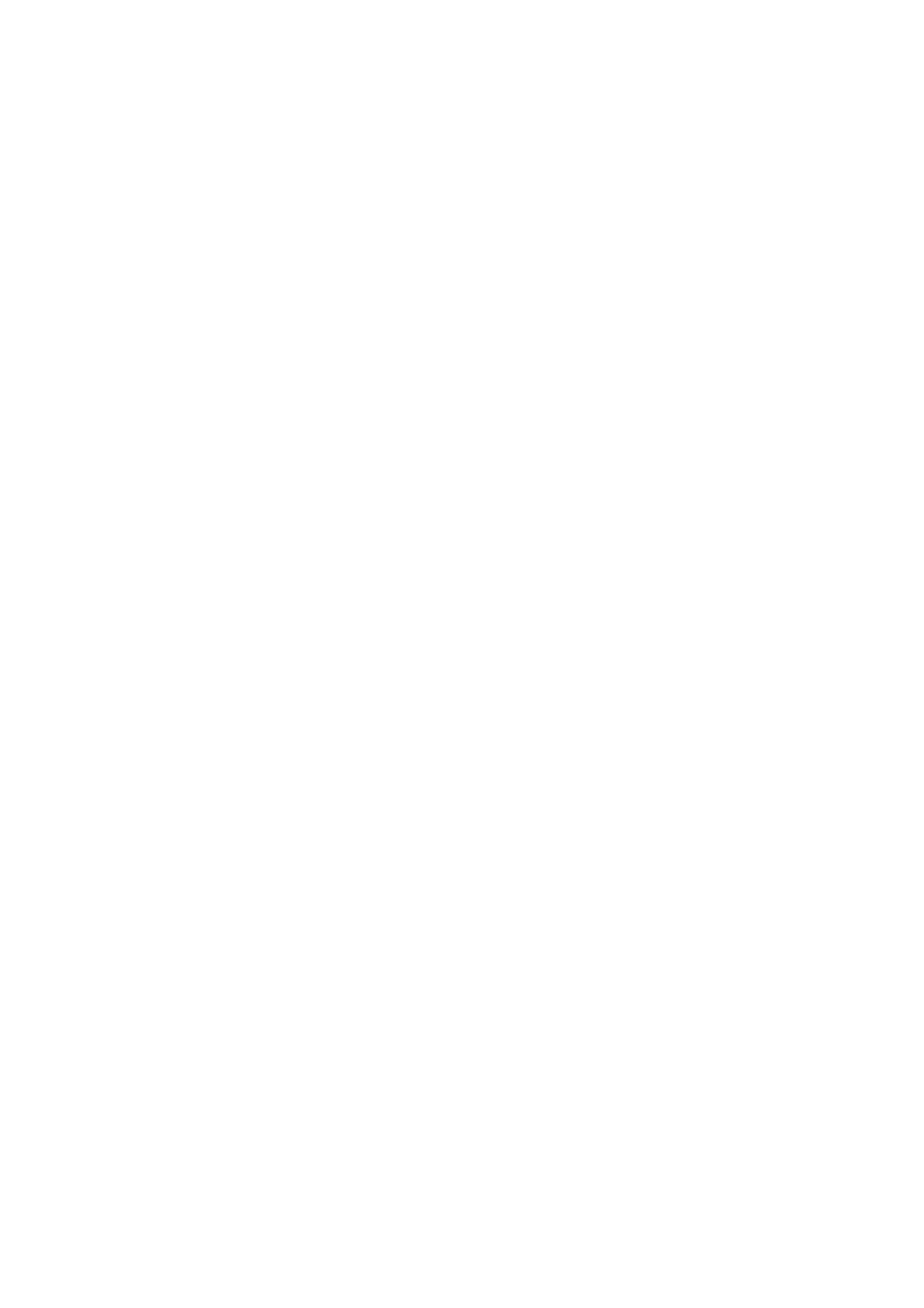
Remerciements
Ce travail a été effectué sous la direction de Monsieur Houcine Zeroug, professeur à
l’université des sciences et de la technologie Houari Boumédiène (U.S.T.H.B). Je tiens à le
remercier pour la confiance qu’il m’a témoignée en acceptant de diriger ce travail. Sa
disponibilité, ses conseils et ses encouragements durant de longues années m’ont été d’un grand
apport pour l’aboutissement de ce travail.
Je remercie Monsieur Nacer Eddine Benamrouche, professeur à l’université Mouloud
Mammeri de Tizi-Ouzou (U.M.M.T.O) pour l’honneur qu’il nous fait en acceptant de présider ce jury.
Que Monsieur Mohammed-El-Hadi Zaim, professeur à l’école polytechnique de Nantes
trouve ici l’expression de mes plus vifs remerciements pour avoir accepter de nous consacrer un
peu de temps de son activité scientifique en participant à ce jury.
Je remercie également Monsieur Toufik Rekioua, professeur à l’université
Abderrhamane Mira de Béjaïa (U.A.M.B) d’avoir accepter d’examiner ce travail et de faire partie
du jury.
Que Monsieur Larbi Refoufi, professeur à l’université M’hamed Bougara de Boumerdes
(U.M.B.B), qui a bien voulu faire partie du jury, trouve ici l’expression de mes vifs remerciements.
Je tiens également à remercier Monsieur Salah Haddad, Professeur à l’université
Mouloud Mammeri de Tizi-Ouzou (U.M.M.T.O) pour avoir accepter d’examiner et de critiquer
ce travail.
Mes remerciements vont également à Mr Hamid Sediki, Mr Said Harmim et Mr
Brahim Nait Kaci, pour leur amitié ainsi que pour le temps passé ensemble à remettre en cause
nos connaissances sur le monde des machines électriques.
Que Mr Tahar Otmane Cherif et Mr Nahid Mufidzada trouvent ici toute ma gratitude
pour leur soutien moral et leurs encouragements durant ce travail.
Je remercie également Mr Ali Bechouche, notre jeune collègue et Doctorant au niveau du
département pour sa sympathie et ses encouragements.
Je ne peux oublier de remercier Mr Azouaou Aoudj, informaticien de notre faculté, qui
par sa disponibilité, sa serviabilité et ses compétences fortes appréciées en informatique, nous a
énormément facilité la tache.
Que tous les collègues du département d’Electrotechnique de L’U.M.M.T.O, trouvent ici
mes sincères sentiments de reconnaissance, en particulier l’équipe du Labo TES 403, pour leurs
encouragements.