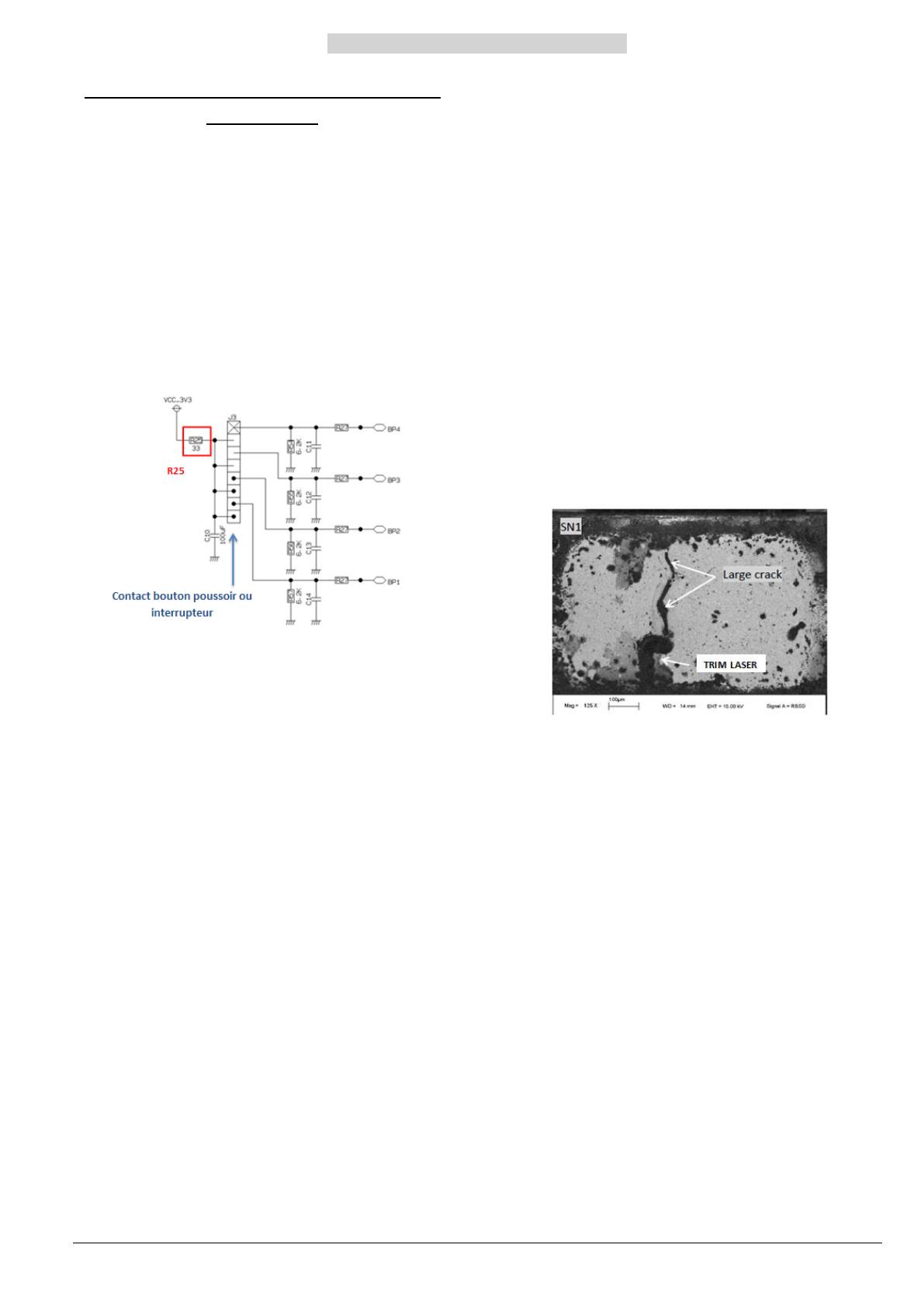
Natassha Nadia MAZNAN – GE5 2015/2016
Proprietary data, Company confidential. All rights reserved Hager Electro SA Page 1 / 3
ANALYSE DE ROBUSTESSE DES ENTREES
DE PRODUIT
I. INTRODUCTION
Des problèmes de détection de l’appui des
boutons poussoirs ou des interrupteurs ont été
observés sur le terrain. Lorsqu’il y a un appui, le
produit doit envoyer les données sur le bus de
communication KNX. Suite à l’analyse de
défaillance qui a été faite, nous avons trouvé que
la défaillance était due à un défaut sur une
résistance de filtrage.
Sur des produits retournés par le terrain, une
augmentation de la valeur de la résistance de
filtrage, R25 a été observée. A cause de cette
augmentation de valeur, le niveau de tension
transmit aux ports d’entrée de microcontrôleur
devenait trop faible pour être détecté par le
microcontrôleur. Par conséquence, le
microcontrôleur n’arrivait pas à détecter l’appui
de bouton poussoir.
Le but de cette analyse de robustesse est
d’identifier la cause racine ou la root cause de la
défaillance de cette résistance. Après avoir
identifié la cause racine, des solutions pour
éliminer la défaillance doivent être identifiées.
Pour confirmer et valider la cause racine, il faut
reproduire la même défaillance que celle apparue
sur le terrain.
II. ANALYSE DE LA CAUSE RACINE
Suite à une analyse par rayon X et une
visualisation par MEB (Microscope Electronique
à Balayage), nous avons observé la présence
d’une fissure sur la couche résistive de la
résistance défectueuse. La fissure qui s’est
produite dans la zone du point chaud empêchait
le passage du courant dans la résistance. Cela
explique donc l’augmentation de la valeur de la
résistance.
D’après l’analyse de défaillance effectuée,
nous avons identifié que la fissure était due à une
impulsion de puissance importante. Connaissant
le mode de défaillance de la résistance, il a fallu,
dans la suite d’analyse, identifier les conditions
ou les facteurs qui ont fait augmenter l’appel de
courant et de tension dans la résistance R25.
Une étude électronique du circuit a donc été
réalisée. L’étude sur le procès de fabrication de
la résistance a aussi été réalisée afin d’étudier
tous les évènements possibles qui ont fragilisé la
résistance.
Les simulations sur le logiciel PSPICE ont été
effectuées pour réaliser l’étude électronique du
circuit. Grâce aux simulations, les conditions de
fonctionnement les plus critiques ont été
identifiées. Les conditions critiques sont des
conditions dans lesquelles la résistance R25 est
stressée par une tension ou un courant élevé.
Un branchement des entrées à une source
de tension extérieure a été identifié comme la
cause racine de la défaillance. La tension
extérieure probable est la tension de bus KNX
30V qui est sa tension d’alimentation. Les
entrées de produit sont conçues pour être reliée
à un contact sec comme un bouton poussoir ou
un interrupteur. Lorsqu’il y a un contact entre les
entrées et une source extérieure même pendant
une durée très courte, la défaillance de la
résistance se produit. La résistance R25 est une
résistance CMS 0603 de 33Ω. La puissance de
Figure 1: Le circuit des entrées du produit
Figure 2: Fissure sur la couche résistive