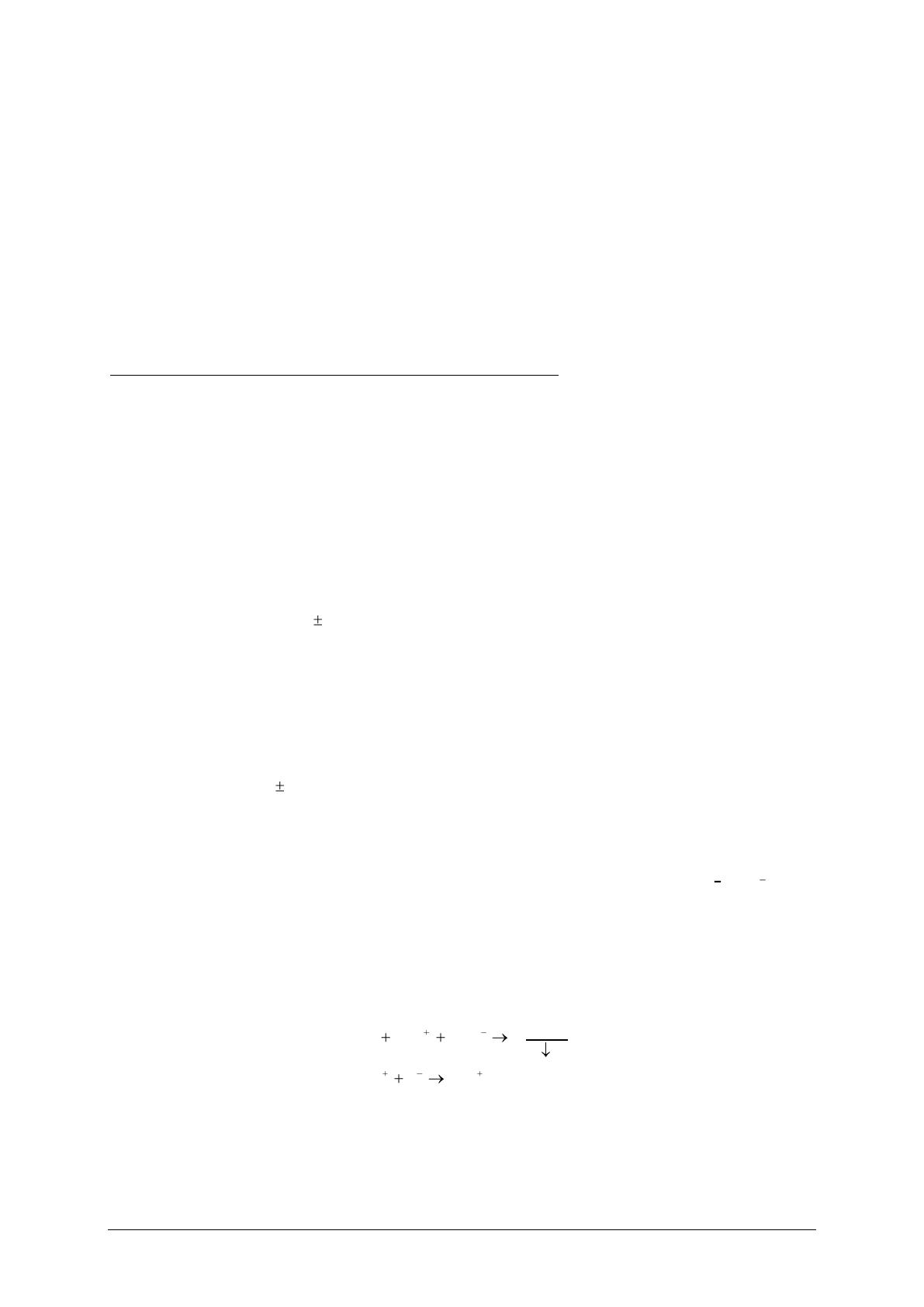
Electrochimie et applications – Dépôt électrolytique des métaux 4
Le choix entre l’électroraffinage, l’électroobtention ou une autre voie chimique
d’extraction est influencée par le minerai de départ, les impuretés présentes (ex.:
présence de métaux nobles tels que Au, Pt, ...), la pureté exigée du métal, le prix de
revient de l’énergie thermique et de l’énergie électrique.
Si on veut faire un bilan correct, il est en effet important de considérer que
l’électroraffinage exige une étape préalable de métallurgie thermique consommatrice
d’énergie thermique.
A titre d’exemple, on comparera les deux méthodes dans le cas du cuivre
Exemple de l’électroraffinage - Electroobtention du cuivre
Le cuivre est principalement utilisé en électricité et en électronique et la conductibilité est
très sensible à la présence de traces telles que l’arsenic. Il est donc nécessaire de
produire un cuivre de très haute pureté (>99,99 %).
Dans le cas de l’électroraffinage, on part de minerais le plus souvent sulfurés tels que la
chalcopyrite (CuFeS2) ou la chalcosine (Cu2S) et on procède à une série d’opérations
reprises au tableau III qui conduisent au cuivre blister qui titre 98-99 % de cuivre; les
principales impuretés qui ont suivi le cuivre dans l’élaboration sont : les métaux nobles
(Ag, Au, Pt,...) et les impuretés moins nobles (Ni, Pb, Sb, As, Fe, Co,...).
Le tableau IV donne les principales caractéristiques du bain et de l’électrolyse. Le métal
impur forme les anodes ( 350 kgs) et les cathodes sont des feuilles de cuivre pur. La
tension anodique est choisie de sorte que les métaux plus nobles que le cuivre (moins
facilement oxydables), par exemple l’or et l’argent, tombent au fond du bain sous forme
de boues qui seront récupérées séparément.
La tension cathodique ne permet pas la décharge des cations moins oxydants (plus
difficilement réductibles) que le cuivre. De plus, les cations plus oxydants tels que Ag+
qui pourraient se déposer n’existant plus dans la solution, on obtient après électrolyse
sélective prolongée ( 20 jours avec 250 kWh par tonne de cuivre) un métal très pur à
99,99 % minimum.
Dans le cas de l’électroobtention (tableau V), on part le plus souvent de minerais oxydés
tels que la malachite (Cu2CO3(OH)2), azurite,... . Ces minerais sont attaqués par l’acide
sulfurique le plus souvent, et les impuretés que l’on retrouve en solution sont Cl , NO3,
Fe3+; cette solution doit être purifiée pour éviter des pertes de rendement lors de
l’électrolyse.
Les ions chlorures sont éliminés sous forme de chlorure cuivreux.
Les ions Fe3+ sont réduits en Fe2+ par le cuivre ou par injection de SO2.
Les principales caractéristiques sont rassemblées au tableau IV et comparées à
l’électroraffinage.