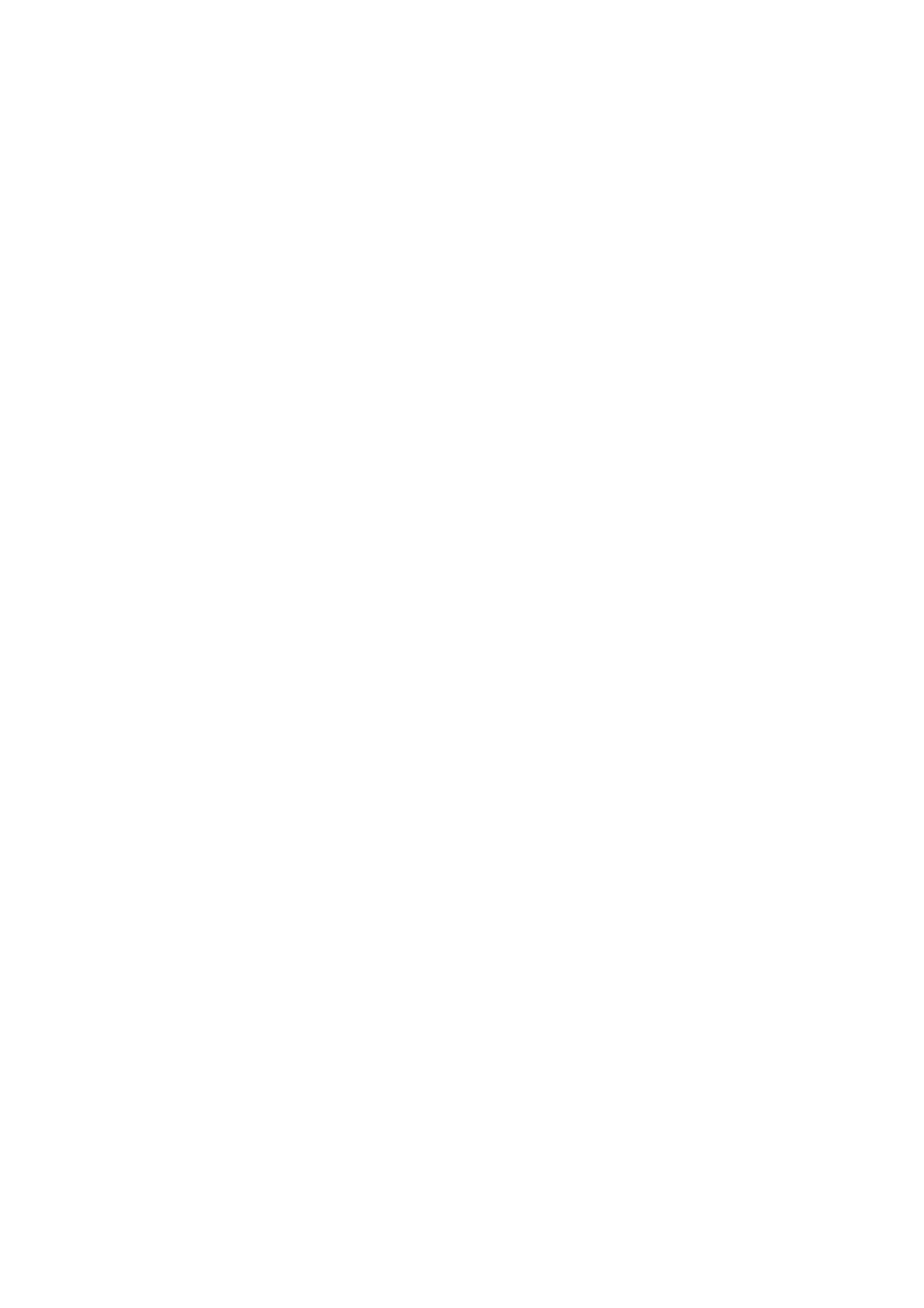
Table des matières
__________________________________________________________________________________________
3
TABLE DES MATIERES :
Chapitre I : Introduction.......................................................................................................13
I.1 Les microsystèmes.................................................................................................................13
I.2 Marché des microsystèmes....................................................................................................14
I.3 Structure du mémoire de thèse ..............................................................................................14
Chapitre II : Etat de l'art ...................................................................................................... 17
II.1 Introduction ...........................................................................................................................17
II.2 La biométrie comme méthode d'identification ......................................................................17
II.3 L’empreinte digitale ..............................................................................................................19
II.3.1 Caractéristiques d’une empreinte digitale........................................................................19
II.3.2 Méthode d’extraction de la signature et de reconnaissance de l’empreinte digitale........20
II.4 Les capteurs d’empreintes digitales.......................................................................................22
II.4.1 Les capteurs d'empreintes digitales macroscopiques .......................................................22
II.4.2 Les capteurs intégrés d'empreintes digitales ....................................................................24
II.5 Conclusion.............................................................................................................................31
Chapitre III : Conception et réalisation............................................................................... 33
III.1 Introduction ...........................................................................................................................33
III.2 Capteur tactile réalisé par micro-usinage en volume.............................................................33
III.2.1 Principe de fonctionnement du capteur .......................................................................34
III.2.2 Cahier des charges .......................................................................................................35
III.3 La piezorésistivité..................................................................................................................36
III.3.1 La piezorésistivité dans le cas du silicium monocristallin...........................................36
III.3.2 Facteurs de jauge .........................................................................................................39
III.3.3 Récapitulatif concernant les facteurs de jauge.............................................................42
III.3.4 Explication physique du phénomène ...........................................................................42
III.3.5 Piezorésistivité du silicium polycristallin....................................................................44
III.3.6 Conclusion sur la piezorésistivité ................................................................................45
III.4 Le micro-usinage en volume .................................................................................................45
III.4.1 La gravure anisotrope du silicium : généralités...........................................................46
III.4.2 Le micro-usinage en volume par la face avant ............................................................50
III.4.3 Le micro-usinage en volume par la face arrière .......................................................... 52
III.4.4 Le micro-usinage en volume mixte par la face avant et arrière...................................53
III.4.5 Le micro-usinage électrochimique ..............................................................................53
III.4.6 Détermination des temps de gravure : Calculs et simulations .....................................54
III.4.7 Conclusion sur le micro-usinage en volume................................................................ 58