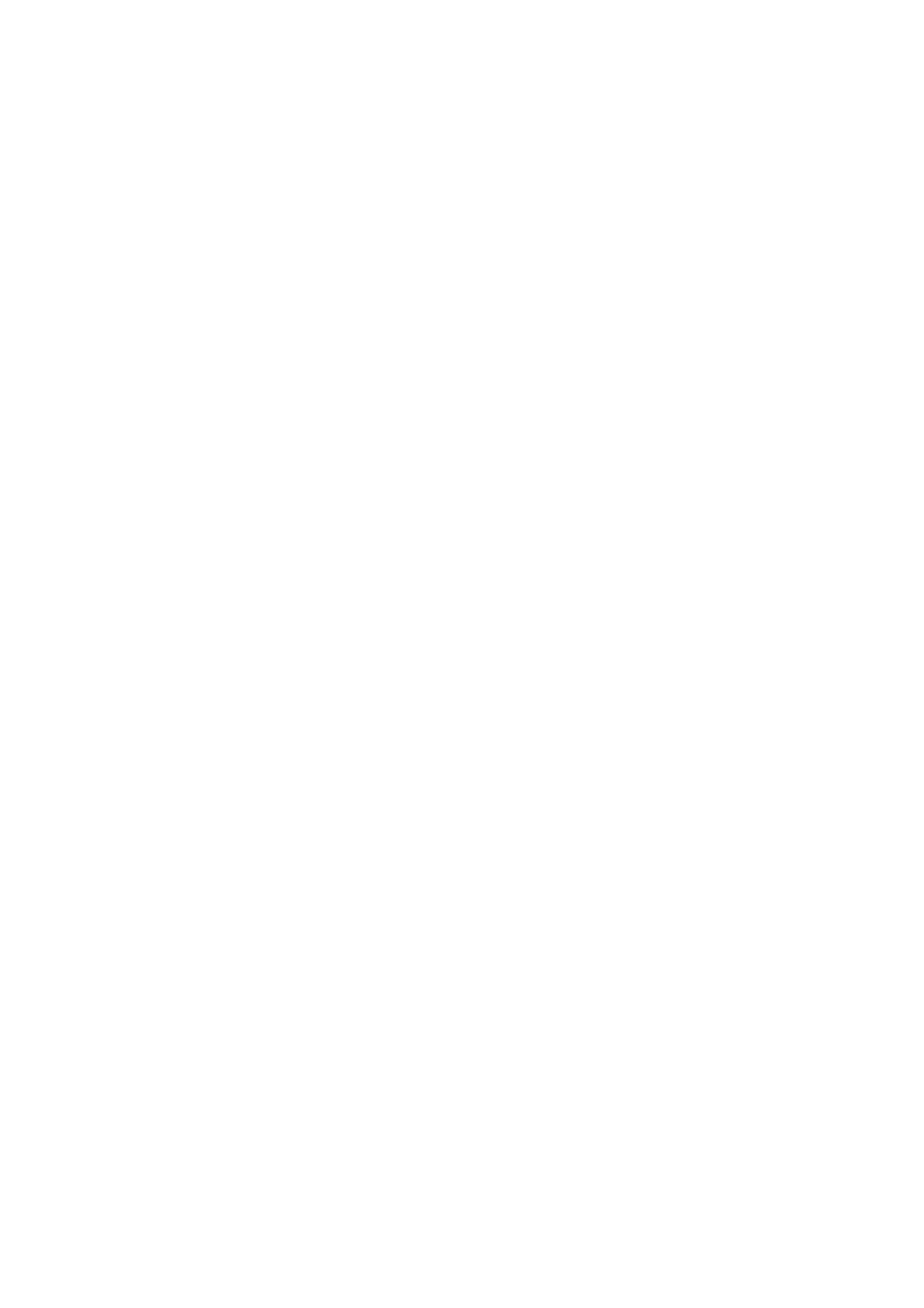
RÉSUMÉ
On a souvent recours à des assemblages métal-céramique pour des systèmes complexes
couplant les propriétés, souvent opposées, des alliages métalliques et des céramiques. Les
besoins industriels pour de hautes températures d’utilisation, en milieu corrosifs, restent
toujours difficiles à satisfaire de façon fiable.
Deux céramiques techniques industrielles ont été retenues pour cette étude : le carbure de
silicium SiC et l’alumine Al2O3. Elles ont été assemblées à un superalliage de Nickel
réfractaire (HAYNES™214®), selon le procédé de thermo-compression sous vide, par
l’intermédiaire d’un joint métallique de faible épaisseur.
La forte réactivité du SiC avec le nickel a conduit à rechercher une barrière de diffusion
entre l’alliage et la céramique. Un joint d’argent ne formant aucun siliciure a permis
d’éviter cette réactivité et a conduit ainsi à des tenues mécaniques en cisaillement
significatives (45 MPa).
Pour l’alumine (Al2O3), nous nous sommes orientés vers l’utilisation de joints de nickel,
peu réactif avec cet oxyde. Cependant la différence de coefficient de dilatation thermique
entre la céramique (Al2O3) et les métaux (Ni et HAYNES™214®) conduit à de fortes
concentrations de contraintes résiduelles à l’interface. Une simulation par éléments finis,
en utilisant le code ABAQUS, a permis de localiser le champ de contraintes résiduelles
dans ce type d’assemblage. Une comparaison entre un calcul élasto-plastique et un calcul
élasto-visco-plastique a été réalisée. La distribution des contraintes est sensible à
l’épaisseur du joint de nickel ainsi qu’aux dimensions et formes respectives de l’alliage et
de la céramique. Il a ainsi été montré que le calcul élasto-visco-plastique est
indispensable pour caractériser la liaison Al2O3/Ni/HAYNES™214®, contrairement à des
liaisons Al2O3/Ni/Al2O3 étudiées plus classiquement. De plus, les contraintes de tension
dans la céramique sont beaucoup plus importantes pour l’assemblage alumine/alliage
métallique que pour l’assemblage alumine/alumine. Ceci est retrouvé expérimentalement
par les résultats de caractérisation mécanique (cisaillement, délamination) de ces deux
types d’assemblage et par des mesures expérimentales de contraintes résiduelles par
indentation et par diffraction des rayons X.
La fragilisation de l’alumine près de l’interface est un phénomène connu dû
essentiellement à la diffusion du métal de liaison et au frottement entre le joint métallique
et l’alumine. Une corrélation entre la ténacité, l’intensité des contraintes résiduelles et le
piégeage de charges électriques a été montrée.
Enfin, l’étude de joints multicouches Cu-Ni-Cu a permis d’accommoder les contraintes et
d’améliorer la résistance de l’assemblage Alumine/HAYNES™214®. De plus, la pré-
oxydation des joints de cuivre côté alumine, reproduisant ainsi la méthode de l’eutectique,
ouvre une voie quant à une utilisation des assemblages pour de hautes températures
(> 1200 °C) et l’industrialisation du procédé pour de grandes séries.
Mots clés : Liaison céramique-métal, thermocompression, contraintes résiduelles,
simulation numérique, éléments finis, diffraction X, indentation, carbure de silicium,
alumine.