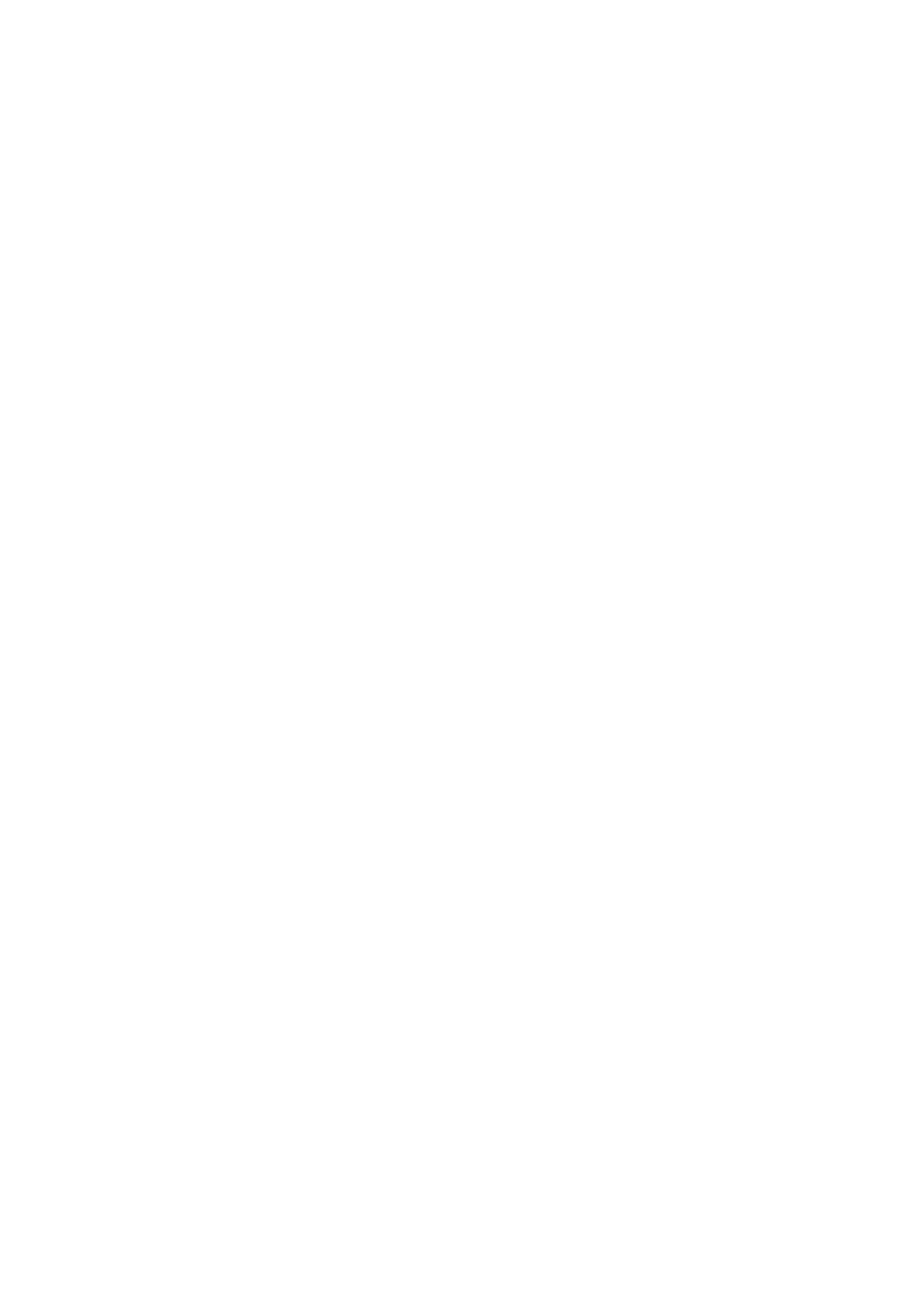
Résumé
L’incorporation de particules de céramique, telles que Sic, Al2O3, B4C, TiO2, dans la matrice,
peut améliorer les propriétés physiques et mécaniques du métal de base et détériorer sa
résistance vis-à-vis de la corrosion. Notre étude consiste en l’élaboration à la caractérisation
d’un composite en poudres (Al/Al2O3). Le procédé d’élaboration utilisé (agitation manuelle
du mélange de poudre dans un récipient suivie par une compression uniaxiale) donne un
composite hétérogène, ne change pas la dureté à charges réduites mais modifié la résistance à
la corrosion.
Mots clés : Composite Aluminium/alumine, Aluminium, alumine, déformation,
caractérisation physico-chimique.
Abstract :
The incorporation of ceramics particles, such as Sic, Al2O3, B4C, TiO2, in the matrix, can
improve the base metal physical and mechanical properties and deteriorate its corrosion
resistance. This study consists of the elaboration and the characterization of composite
powders (Al/Al2O3). The used elaboration process (manual agitation of the mixture of
powders in a container followed by a uniaxial pressing) gives a heterogeneous composite, do
not change hardness with reduced loads but modified the corrosion resistance.
Keywords: Composite, Aluminum/alumina, Aluminum, alumina, deformation,
physicochemical characterization.