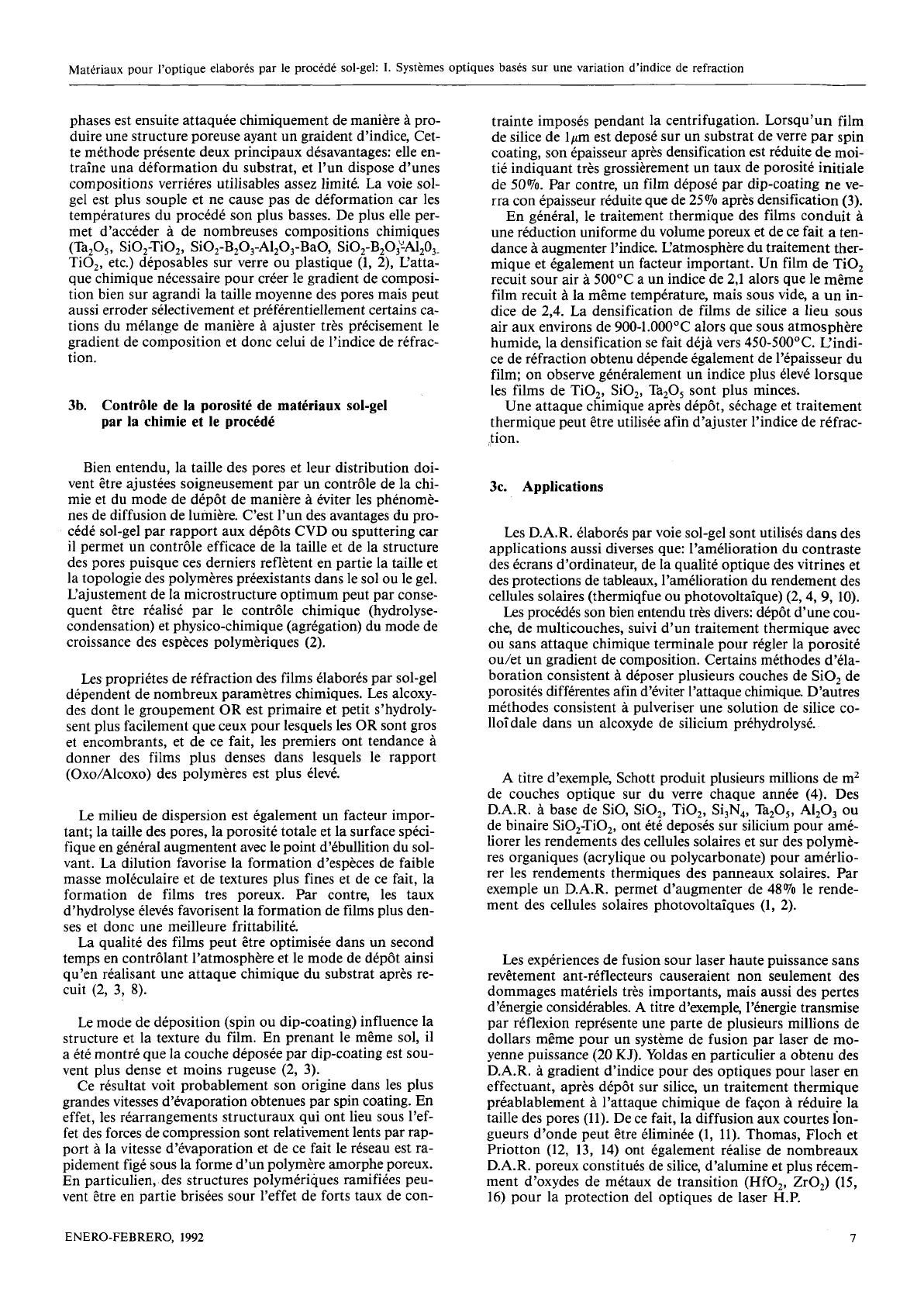
Matériaux pour l'optique élaborés par le procédé sol-gel: I. Systèmes optiques basés sur une variation d'indice de refraction
phases est ensuite attaquée chimiquement de manière à pro-
duire une structure poreuse ayant un graident d'indice, Cet-
te méthode présente deux principaux désavantages: elle en-
traîne una déformation du substrat, et Tun dispose d'unes
compositions verrières utiHsables assez limité. La voie sol-
gel est plus souple et ne cause pas de déformation car les
températures du procédé son plus basses. De plus elle per-
met d'accéder à de nombreuses compositions chimiques
(Ta205,
SÍO2-TÍO2, Si02-B203-Al203-BaO, SiO2-B2O3^Al203.
TÍO2,
etc.) déposables sur verre ou plastique (1, 2), L'atta-
que chimique nécessaire pour créer le gradient de composi-
tion bien sur agrandi la taille moyenne des pores mais peut
aussi erroder sélectivement et préférentiellement certains ca-
tions du mélange de manière à ajuster très pfécisement le
gradient de composition et donc celui de l'indice de réfrac-
tion.
3b.
Contrôle de la porosité de matériaux sol-gel
par la chimie et le procédé
trainte imposés pendant la centrifugation. Lorsqu'un film
de silice de l/^m est déposé sur un substrat de verre par spin
coating, son épaisseur après densification est réduite de moi-
tié indiquant très grossièrement un taux de porosité initiale
de 50%. Par contre, un film déposé par dip-coating ne ve-
rra con épaisseur réduite que de 25% après densification (3).
En général, le traitement thermique des films conduit à
une réduction uniforme du volume poreux et de ce fait a ten-
dance à augmenter l'indice. L'atmosphère du traitement ther-
mique et également un facteur important. Un film de TÍO2
recuit sour air à 500°C a un indice de
2,1
alors que le même
film recuit à la même température, mais sous vide, a un in-
dice de 2,4. La densification de films de siHce a Heu sous
air aux environs de 900-1.000°C alors que sous atmosphère
humide, la densification se fait déjà vers 450-500°C. L'indi-
ce de réfraction obtenu dépende également de l'épaisseur du
film; on observe généralement un indice plus élevé lorsque
les films de TÍO2, SÍO2, Ta205 sont plus minces.
Une attaque chimique après dépôt, séchage et traitement
thermique peut être utilisée afin d'ajuster l'indice de réfrac-
tion.
Bien entendu, la taille des pores et leur distribution doi-
vent être ajustées soigneusement par un contrôle de la chi-
mie et du mode de dépôt de manière à éviter les phénomè-
nes de diffusion de lumière. C'est l'un des avantages du pro-
cédé sol-gel par rapport aux dépôts CVD ou sputtering car
il permet un contrôle efficace de la taille et de la structure
des pores puisque ces derniers reflètent en partie la taille et
la topologie des polymères préexistants dans le sol ou le gel.
L'ajustement de la microstructure optimum peut par conse-
quent être réalisé par le contrôle chimique (hydrolyse-
condensation) et physico-chimique (agrégation) du mode de
croissance des espèces polymèriques (2).
Les propriétés de réfraction des films élaborés par sol-gel
dépendent de nombreux paramètres chimiques. Les alcoxy-
des dont le groupement OR est primaire et petit s'hydroly-
sent plus facilement que ceux pour lesquels les OR sont gros
et encombrants, et de ce fait, les premiers ont tendance à
donner des films plus denses dans lesquels le rapport
(Oxo/Alcoxo) des polymères est plus élevé.
Le milieu de dispersion est également un facteur impor-
tant; la taille des pores, la porosité totale et la surface spéci-
fique en général augmentent avec le point d'ebullition du sol-
vant. La dilution favorise la formation d'espèces de faible
masse moléculaire et de textures plus fines et de ce fait, la
formation de films tres poreux. Par contre, les taux
d'hydrolyse élevés favorisent la formation de films plus den-
ses et donc une meilleure frittabilité.
La qualité des films peut être optimisée dans un second
temps en contrôlant l'atmosphère et le mode de dépôt ainsi
qu'en réalisant une attaque chimique du substrat après re-
cuit (2, 3, 8).
Le mode de déposition (spin ou dip-coating) influence la
structure et la texture du film. En prenant le même sol, il
a été montré que la couche déposée par dip-coating est sou-
vent plus dense et moins rugeuse (2, 3).
Ce résultat voit probablement son origine dans les plus
grandes vitesses d'évaporation obtenues par spin coating. En
effet, les réarrangements structuraux qui ont lieu sous
l'ef-
fet des forces de compression sont relativement lents par rap-
port à la vitesse d'évaporation et de ce fait le réseau est ra-
pidement figé sous la forme d'un polymère amorphe poreux.
En particulien, des structures polymèriques ramifiées peu-
vent être en partie brisées sour l'effet de forts taux de con-
3c.
Applications
Les D.A.R. élaborés par voie sol-gel sont utilisés dans des
applications aussi diverses que: l'amélioration du contraste
des écrans d'ordinateur, de la quahté optique des vitrines et
des protections de tableaux, l'amélioration du rendement des
cellules solaires (thermiqfue ou photovoltaîque) (2, 4, 9, 10).
Les procédés son bien entendu très
divers:
dépôt d'une cou-
che,
de multicouches, suivi d'un traitement thermique avec
ou sans attaque chimique terminale pour régler la porosité
ou/et un gradient de composition. Certains méthodes d'éla-
boration consistent à déposer plusieurs couches de SÍO2 de
porosités différentes afin d'éviter l'attaque chimique. D'autres
méthodes consistent à pulveriser une solution de sihce co-
lloïdale dans un alcoxyde de silicium préhydrolysé.
A titre d'exemple, Schott produit plusieurs millions de m^
de couches optique sur du verre chaque année (4). Des
D.A.R. à base de SiO, SÍO2, TÍO2, SÍ3N4, Ta205, AI2O3 ou
de binaire SÍO2-TÍO2, ont été déposés sur silicium pour amé-
liorer les rendements des cellules solaires et sur des polymè-
res organiques (acryhque ou polycarbonate) pour amérUo-
rer les rendements thermiques des panneaux solaires. Par
exemple un D.A.R. permet d'augmenter de 48^0 le rende-
ment des cellules solaires photovoltaîques (1, 2).
Les expériences de fusion sour laser haute puissance sans
revêtement ant-réflecteurs causeraient non seulement des
dommages matériels très importants, mais aussi des pertes
d'énergie considérables. A titre d'exemple, l'énergie transmise
par réflexion représente une parte de plusieurs milUons de
dollars même pour un système de fusion par laser de mo-
yenne puissance (20 KJ). Yoldas en particulier a obtenu des
D.A.R. à gradient d'indice pour des optiques pour laser en
effectuant, après dépôt sur silice, un traitement thermique
préablablement à l'attaque chimique de façon à réduire la
taille des pores (11). De ce fait, la diffusion aux courtes lon-
gueurs d'onde peut être éhminée (1, 11). Thomas, Floch et
Priotton (12, 13, 14) ont également réahse de nombreaux
D.A.R. poreux constitués de silice, d'alumine et plus récem-
ment d'oxydes de métaux de transition (Hf02, Zr02) (15,
16) pour la protection del optiques de laser H.P.
ENERO-FEBRERO, 1992