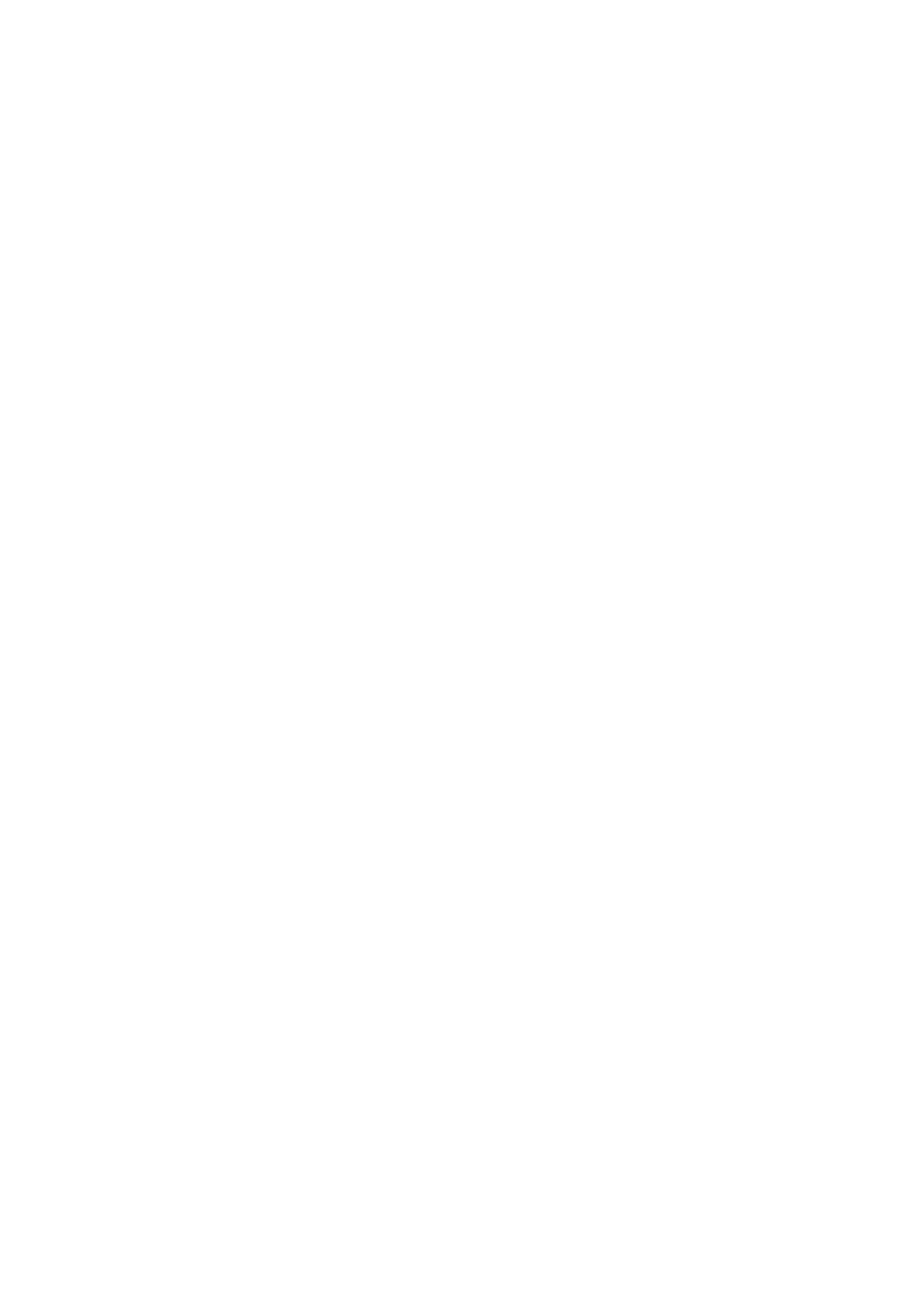
0 3
Résumé
Avec le développement de l’usage d’internet et les nouveaux services tout en ligne, la
quantité de données traitée par les data-centers ne cessent de croître. Ainsi, si la mise en
parallèle de plusieurs serveurs permet de répondre à cette demande, un problème structurel
apparaît. Comme dans les supercalculateurs entre les nœuds de calculs, les données ne
circulent plus suffisamment rapidement entre les serveurs sur les câbles électriques classiques.
Pour pallier à ce goulot d’étranglement, l’utilisation de l’optique permet d’obtenir des débits
plus importants. Si les câbles actifs existants permettent une solution rapide, la photonique sur
silicium présente un avantage certain. L’intégration des composants optiques au plus près des
puces électroniques permet de réduire considérablement le chemin des interconnexions ainsi
que leurs coûts énergétiques.
Une chaine de communication optique complète nécessite différents composants. Si les
modulateurs, multiplexeurs, coupleurs fibres, démultiplexeurs et photodetecteurs ont déjà été
démontrés, les sources lasers utilisées sont toujours extérieures à la puce photonique. Il s’agit
en effet du chainon manquant dans l’intégration complète de l’optique grâce à la photonique
sur silicium. Plusieurs architectures ont déjà été proposées mais cette thèse s’appuie sur
l’intégration hybride d’un matériau III-V sur le silicium.
Le travail de cette thèse a consisté en la conception, la fabrication et la caractérisation de
sources laser hybrides III-V sur silicium et a été entièrement accompli aux CEA/LETI.
L’architecture du LETI d’un guide III-V couplé à un guide silicium a été améliorée grâce à un
critère adiabatique pour obtenir une zone active de laser efficace et robuste. Cette architecture
a été déclinée en différents types de lasers (Fabry-Pérot, DBR, racetrack et DFB). La
fabrication de ces lasers a nécessité des développements de procédés de structuration du
matériau III-V reporté sur du silicium dans les laboratoires du CEA/LETI.
Les premiers résultats ont permis la validation de l’architecture utilisée. Les lasers DBR
présentent des seuils inférieurs à 20mA et des puissances optiques maximales supérieures à
20mW dans le guide silicium. Ces lasers ont également un fonctionnement monomode avec
un SMSR de plus de 50dB. Les lasers DFB possèdent quant à eux des seuils de 30mA et des
puissances optiques maximales supérieurs à 40mW dans le guide silicium. Ils sont
monomodes avec un SMSR de 40dB. Ces résultats sont à l’état de l’art mondial sur les
sources lasers hybrides en photonique sur silicium.
Abstract
With the development of the Internet and the new cloud services, the amount of data
processed by data-centers is increasing. Though, if the paralleling of multiple server answer to
this growing quantity, a structural problem arises. As in super calculators between nodes
calculations, data are not transmitted quickly enough between servers on classical electric
cables. This bottleneck can be overcome thanks to the optic which can access greater data
rates. If existing active cables allow a quick resolution, silicon photonic has a clear benefit.
The integration of the optical components closer to the electronic chips reduces substantially
the path of interconnections and their energetic costs.
An optical transmitter and receptor need different components. If modulators,
multiplexers, fiber coupler, multiplexer and photo-detectors are already achieved, laser
sources used are still outside the photonic chip. This is the missing link for a complete optical
integration thanks to the silicon photonic. Several architectures have been proposed but this
thesis relies on hybrid integration of III-V material on silicon.
The work of this thesis consisted on the conception, the fabrication and the
characterization of hybrid III-V on Silicon laser sources and was completely done at the
CEA/LETI. The LETI architecture composed by a III-V waveguide coupled to a silicon