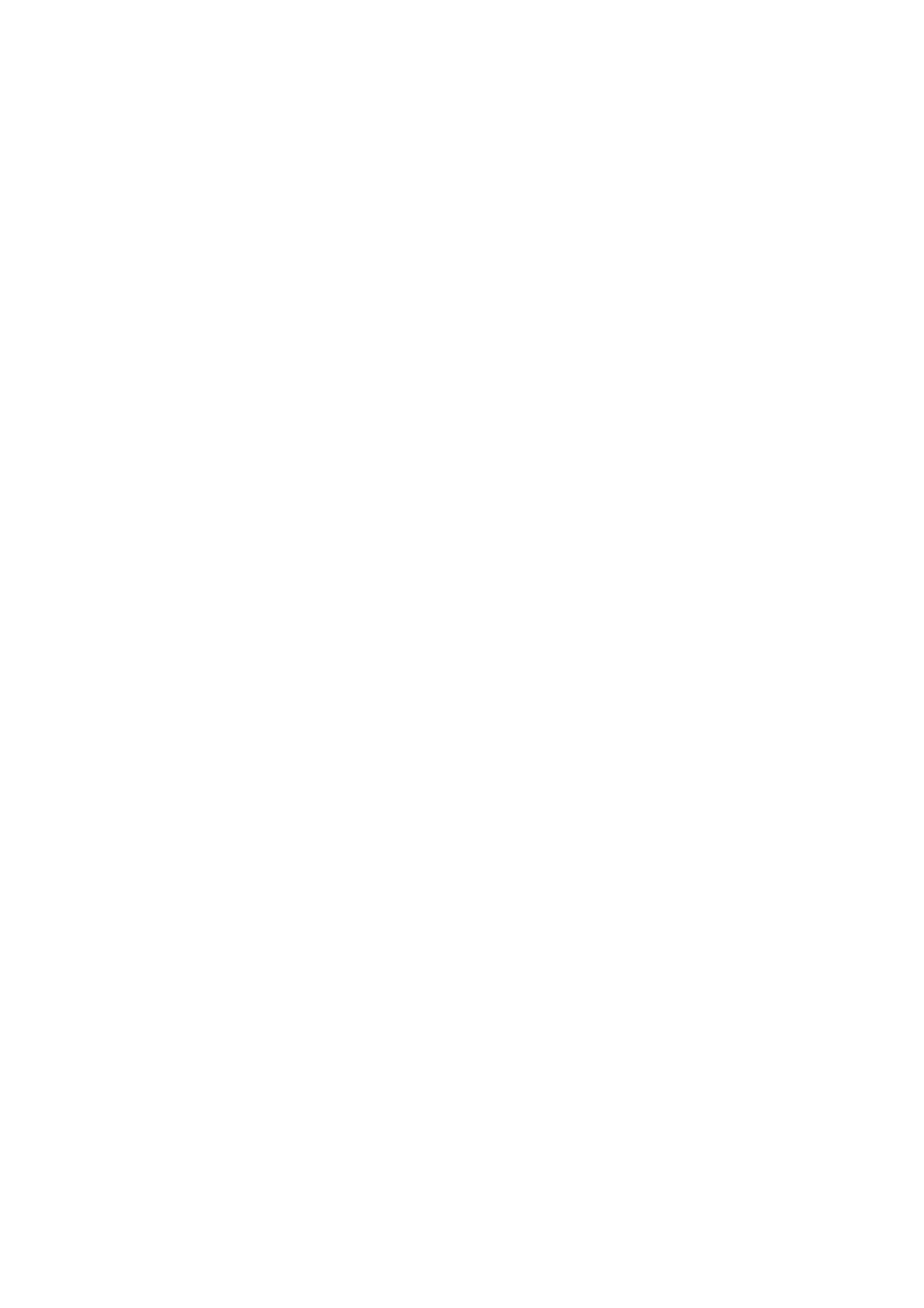
Résumé
Un des problèmes majeurs limitant le rendement des cellules photovoltaïques
est la qualité des contacts. Actuellement, la sérigraphie est la technique la plus cou-
ramment utilisée pour la production de cellules solaires industrielles en raison de son
faible coût, sa rapidité et sa facilité de mise en œuvre. Cependant, cette technique pré-
sente un certain nombre de limitations: résistivité élevée, nécessité d’un dopage
d’émetteur élevé pour assurer un bon contact, taux d’ombre important en raison de la
largeur minimale des contacts comprise entre 100 et 120 µm, alignement indispensable
dans le cas des émetteurs sélectifs… La mise en œuvre de techniques de métallisation
innovantes capables de rivaliser avec la sérigraphie est donc un enjeu essentiel. L’idée
est de s’orienter vers des techniques compatibles avec l’industrie et ne nécessitant ni
photolithographie, ni hautes températures ou basses pressions. Les dépôts de métaux
conducteurs par voie électrochimique semblent répondre à ces contraintes technologi-
ques. Cette thèse s’est focalisée sur le développement et l’optimisation de techni-
ques de métallisation électrochimique permettant le dépôt de métaux conducteurs,
l’argent et le cuivre, par voie électrolytique ou par la technique dite LIP (Light-Induced
Plating). Deux approches ont été abordées pour l’élaboration des contacts en face
avant : l’épaississement de contacts sérigraphiés d’une part, et la réalisation de
contacts entièrement par voie électrochimique sans recours à la sérigraphie. Pour cette
dernière solution, le dépôt d’une couche d’accroche avant l’étape d’épaississement est
nécessaire afin d’assurer une résistivité de contact faible, une bonne adhérence et une
bonne sélectivité au travers de la couche anti-reflet. Ces objectifs ont été atteints grâce
à la mise en œuvre et l’optimisation de dépôts electroless de nickel-phosphore (NiP), y
compris sur émetteur peu dopé. Les investigations menées ont également permis une
meilleure compréhension des mécanismes de formation du contact NiP/Si.
La faisabilité des techniques de dépôt électrochimique a été démontrée pour
diverses applications: cellules avec contacts électrochimiques NiP/Ag en face avant,
cellules de type n, épaississement de contacts fins sérigraphiés… Des résultats très
prometteurs d’amélioration de facteur de forme FF et de rendement η ont été obtenus
et permettent d’envisager une ouverture potentielle vers de nouvelles structures de cel-
lules photovoltaïques à haut rendement : cellules à émetteur peu dopé, cellules à émet-
teur sélectif avec ouverture laser de la couche anti-reflet, cellules à contacts arrières….
Cette thèse est accessible à l'adresse : http://theses.insa-lyon.fr/publication/2011ISAL0032/these.pdf
© [C. Boulord], [2011], INSA de Lyon, tous droits réservés