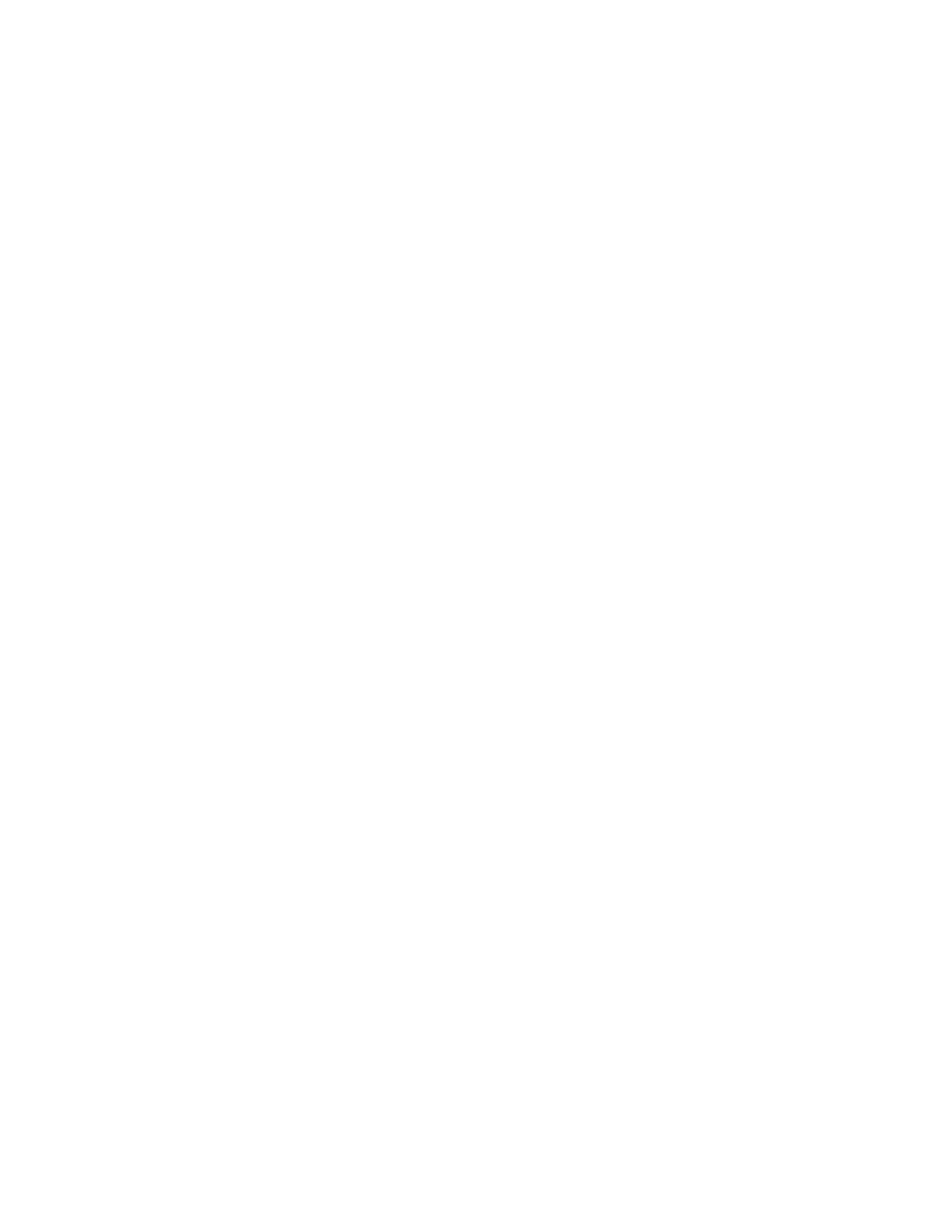
ii
également dans les alliages contenant du magnésium, où il réagit avec ce métal pour former un
chlorure de magnésium, qui réagit alors avec le métal alcalin pour former un chlorure alcalin.
Dans les deux cas, le chlorure alcalin se sépare de la fonte en remontant à la surface, où il flotte.
Le chlore est ajouté à l’aluminium soit à l’état de gaz pur, soit mélangé à un gaz inerte tel que
l’argon ou l’azote, puisqu’il n’est pas nécessaire d’utiliser un gaz fait uniquement de chlore pour
obtenir un nettoyage efficace de la fonte. La lance et le système rotatif d’injection de gaz (SRIG)
sont les deux méthodes utilisées le plus souvent pour diffuser le gaz sous la surface de la fonte et
le disperser dans tout le creuset. Le fluxage à la lance est inefficace en comparaison avec le SRIG
parce que les bulles de gaz sont trop grosses et la population trop petite pour que la méthode soit
efficace. Sa capacité de brassage est elle aussi limitée et oblige à recourir à une méthode
supplémentaire de brassage de la fonte. Avec le SRIG, on n’utilise qu’une fraction du chlore
gazeux utilisé pour le fluxage à la lance, ce qui contribue à faire diminuer les émissions et la
nécessité d’utiliser des épurateurs alcalins. L’utilisation de chlore gazeux abaisse également la
concentration d’hydrogène et d’oxydes dans la fonte d’aluminium en flottant ces impuretés et en
les amenant à la surface du métal en fusion.
Comme la réglementation environnementale régissant l’utilisation du chlore gazeux est
maintenant plus stricte, certains centres de coulée d’aluminium sont en train d’évoluer vers la
mise en place d’un système rotatif d’injection de flux (SRIF) pour le fluxage de la fonte
d’aluminium. Le SRIF utilise un sel réactif, soit du chlorure de magnésium fondu, soit du
fluorure d’aluminium fondu, et un rotor conçu pour injecter le sel solide sous la surface de la
fonte tout en brassant le produit. Les forces de cisaillement produites par la giration rapide du
rotor font que les particules de sel sont immédiatement cisaillées, ce qui en réduit la grosseur et
en augmente la dispersion dans l’aluminium. En outre, le rotor brasse adéquatement tout le
volume d’aluminium et fait en sorte que toute la fonte est traitée. La méthode offre l’avantage de
ne produire pratiquement aucune émission de chlore gazeux ou de gaz chlorhydrique et son
efficacité en matière d’élimination des impuretés alcalines est égale ou supérieure à celle du
SRIG. Le fluorure d’aluminium collabore lui aussi à l’élimination des oxydes de la fonte
puisqu’il favorise le mouillage, l’agglomération et l’élimination de ces impuretés.
Le fluxage à la lance, par SRIG ou par SRIF a lieu dans un four de coulée et les trois méthodes
permettent de réduire de façon adéquate les concentrations de métaux alcalins dans les fontes
d’aluminium. Le SRIG et le SRIF sont les deux procédés les plus fréquemment utilisés dans les
centres de coulée d’aluminium parce qu’ils permettent d’obtenir un métal plus pur et de réduire
les émissions de chlore. On prévoit que, dans un proche avenir, tous les centres de coulée
adopteront le système rotatif d’injection de flux à mesure que les lois environnementales
deviendront plus sévères. Cependant, aucun de ces procédés de fluxage ne permet de respecter
les normes de propreté du métal désignées à la plupart des fins commerciales et certaines étapes
supplémentaires de traitement sont nécessaires.
Après avoir quitté le four de coulée, la fonte est transférée au dégazeur, où l’aluminium en fusion
est soumis à de multiples rotors d’injection de gaz semblables à ceux utilisés dans le SRIG. Le
procédé de dégazage vise à réduire par flottation le niveau d’hydrogène global dans la fonte
fondu et il est appliqué dans un récipient fermé. Le gaz utilisé consiste en du chlore mélangé avec
de l’azote ou de l’argon. La présence de chlore dans le gaz d’alimentation est très importante
puisqu’il est impossible d’obtenir un faible niveau d’hydrogène sans le produit et que celui-ci