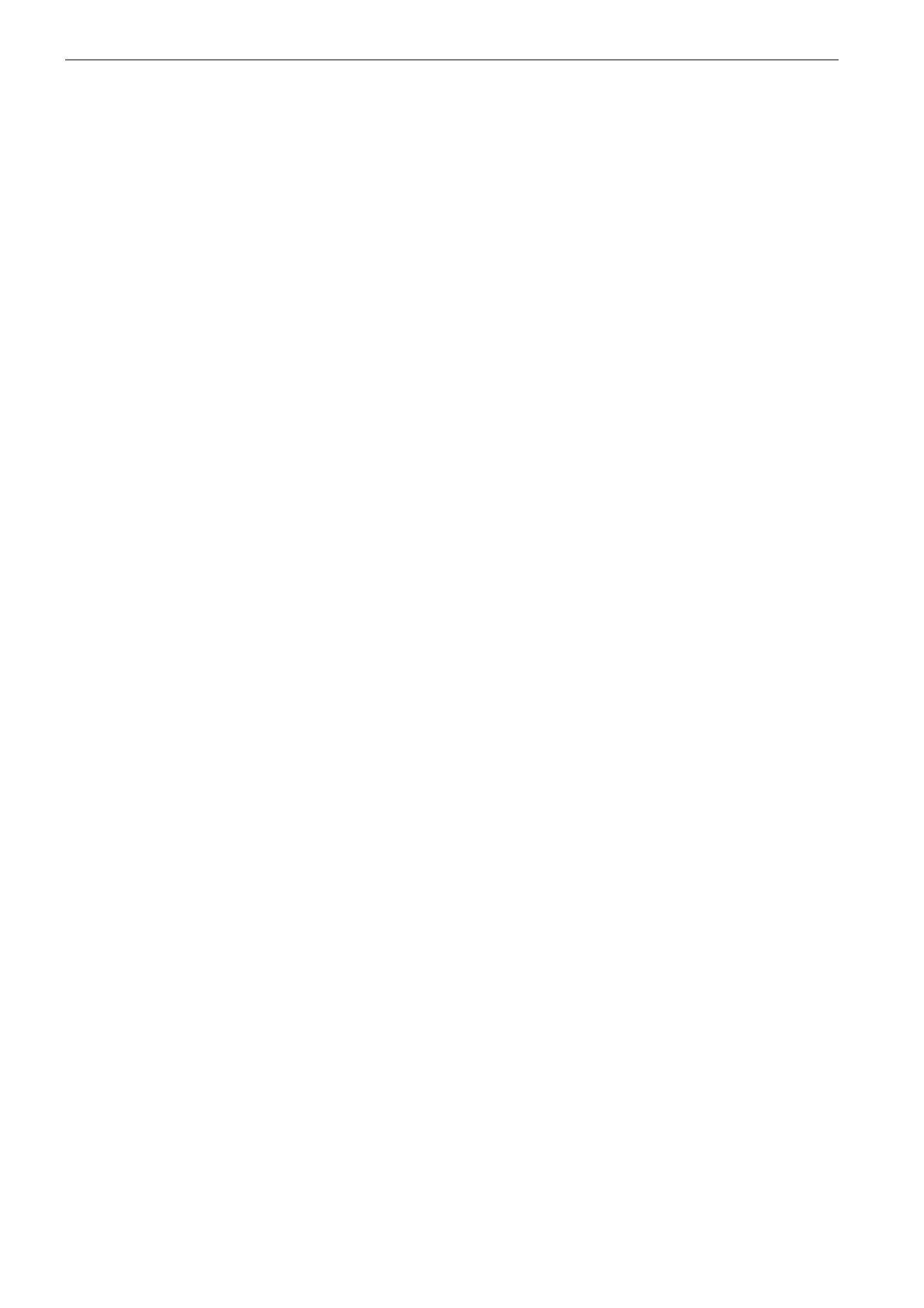
5
Introduction
L’automobile est une des clés de la mobilité et de facto du développement d’une société moderne. Un des
indicateurs du niveau de vie d’un pays est en effet son nombre de véhicules pour 1000 habitants. Toutefois,
outre la crise économique mondiale subie par l’ensemble du système économique actuel, cette industrie doit
relever les nouveaux défis induits par la raréfaction des ressources énergétiques et des matières premières, la
nécessité de concevoir des véhicules de moins en moins polluants ainsi que l’électrification croissante des
automobiles.
Dans ce contexte, le projet M2EI « Machines électriques et Electronique intégrée », au sein duquel cette
thèse CIFRE entre VALEO Systèmes Electriques et le Laboratoire d’Electromécanique de Compiègne s’intègre,
vise à rechercher de nouvelles topologies de machines embarquées pour des applications de type véhicule
hybride au sens large.
Il consiste donc à effectuer une analyse comparative des technologies de machines existantes puis à
rechercher des solutions innovantes tant en termes de machines électriques que d’électronique associée.
Ces améliorations concernent aussi bien le domaine du transport de personnes ou de marchandises en site
urbain que les véhicules particuliers.
De part sa nature multiphysique, la conception optimale d’une machine électrique à haut rendement pour
de telles applications « moteur-générateur » embarqués est un problème compliqué qu’il convient de
formaliser afin d’obtenir une méthodologie efficace de détermination de solution optimale.
Les travaux de cette thèse s’inscrivent dans cette optique de développement de modèles multiphysiques
couplés et utilisation de méthodes d’optimisation robustes dédiés à la conception optimale de structures
électrotechniques.
Le premier chapitre détaillera les enjeux automobiles actuels afin de mettre en exergue la nécessité
d’implanter des machines électriques embarquées dans les véhicules actuels, notamment des alterno-
démarreurs. Nous en déduirons les contraintes et objectifs auxquels ces machines électriques doivent se
conformer avant de dresser un panorama des topologies susceptibles de remplir ces conditions, à savoir
principalement les machines à flux radial ou axial en version synchrone ou asynchrone. Finalement, nous
dresserons un état des lieux des matériaux magnétiques dur et doux permettant d’atteindre ces
performances.
Le second chapitre sera dévolu aux modèles et méthodes de conception optimale de dispositifs
électrotechniques embarqués. Il sera, de ce fait, structuré autour d’une méthodologie générale de conception
allant de l’analyse du cahier des charges à la vérification des solutions optimales en passant par la création de
modèles multiphysiques couplés ainsi que le choix des méthodes d’optimisation. Les modèles multiphysiques
présentés sont des modèles directs classés en fonction de leur complexité et domaine de validité.
Le dernier chapitre utilisera la méthodologie précédente afin de concevoir deux applications inhérentes au
projet M2EI à savoir une machine synchrone à aimants enterrés simple couche et à bobinage distribué
fonctionnant en alterno-démarreur ainsi qu’un système de transmission d’énergie sans contact destiné à
remplacer le système bague balais des machines à bobinage rotorique.
Finalement, une conclusion générale sur ces travaux sera formulée et des perspectives seront abordées.