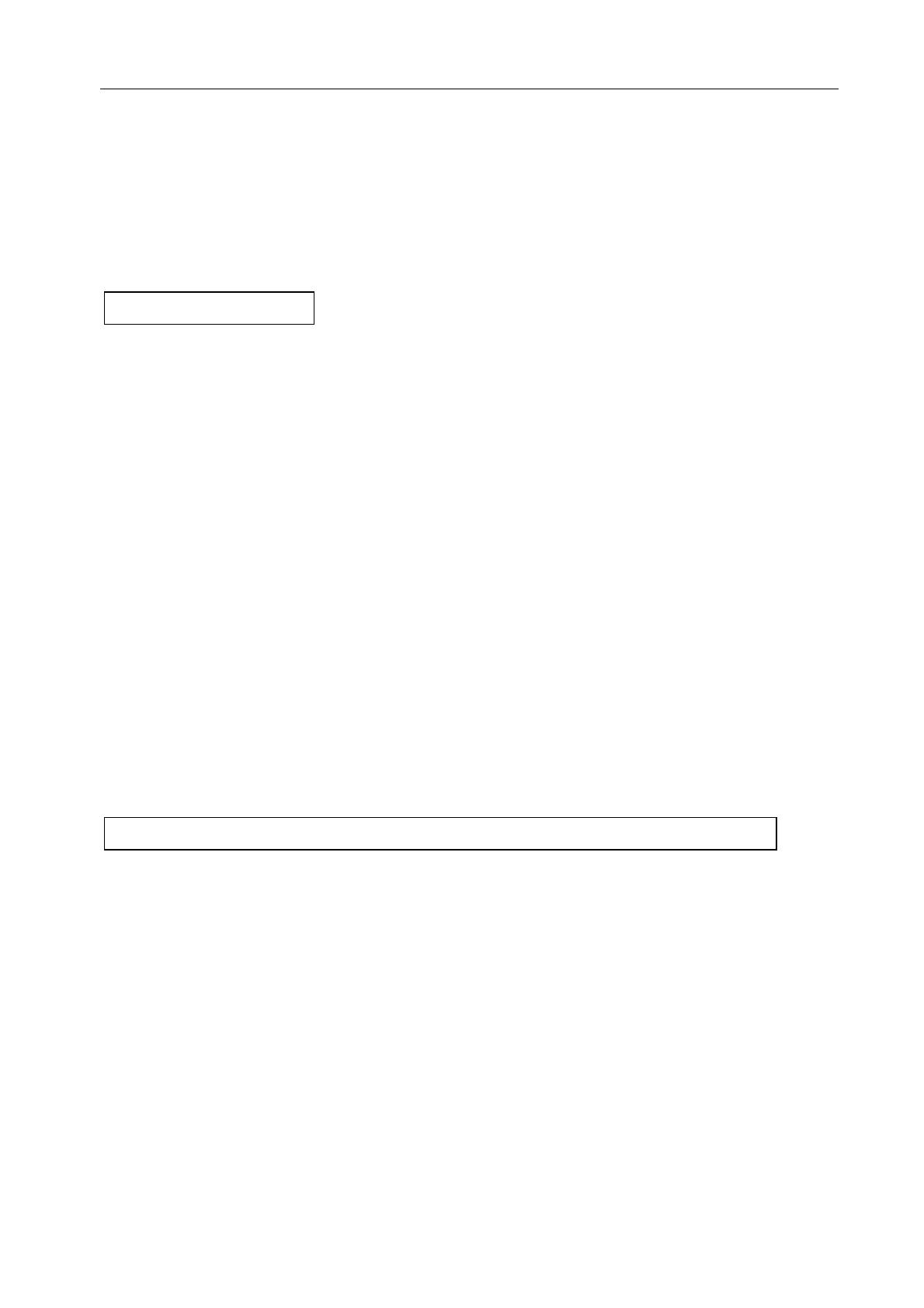
Chapitre VI : Conception et réalisation de démonstrateurs 139
CHAPITRE VI
Conception et réalisation de démonstrateurs
VI.1 Introduction
Au cours des chapitres précédents nous avons développé un modèle de calcul par
éléments finis du comportement thermomécanique des membranes composites SiO2/Si. Dans
ce chapitre nous nous servons de ce modèle pour concevoir et réaliser deux architectures de
capteurs à membrane de type PSOI qui sont présentées et discutées. Un logiciel de conception
a été développé au laboratoire au cours de cette thèse pour prévoir la sortie électrique du
capteur en fonction de la réponse en pression et en température du corps d’épreuve, des
propriétés physiques du polysilicium et de la disposition des jauges. La conception des
capteurs a donc demandé un important travail de programmation qui ne sera pas présenté ici.
Nous montrons simplement la technique d’interpolation linéaire des déformations simulées en
surface du corps d’épreuve qui permet de s’affranchir du maillage éléments finis. Nous
donnons également le principe du calcul des variations de résistance des jauges
piézorésistives. Enfin les premiers résultats sur démonstrateurs sont présentés.
VI.2 Position des jauges piézorésistives sur le corps d’épreuve
Le principe de fonctionnement d’un capteur piézorésistif à membrane de type PSOI a été
décrit au chapitre I. Pour obtenir un capteur de pression sensible les jauges piézorésistives en
surface du corps d’épreuve doivent être disposées aux endroits où celui-ci se déforme le plus
sous pression. La simulation par éléments finis de la réponse pneumatique d’une membrane
carrée permet de connaître les zones de sa surface où les déformations sont maximales et
uniaxiales. Comme le montrent les Figure 82.a et Figure 82.b ces zones sont situées sur les
axes médians de la structure près des bords de la membrane. Dans ces zones les déformations
sont positives (tension) et en majorité uniaxiales.
Du fait de la forme carrée de la membrane, la carte des déformations εy est symétrique par