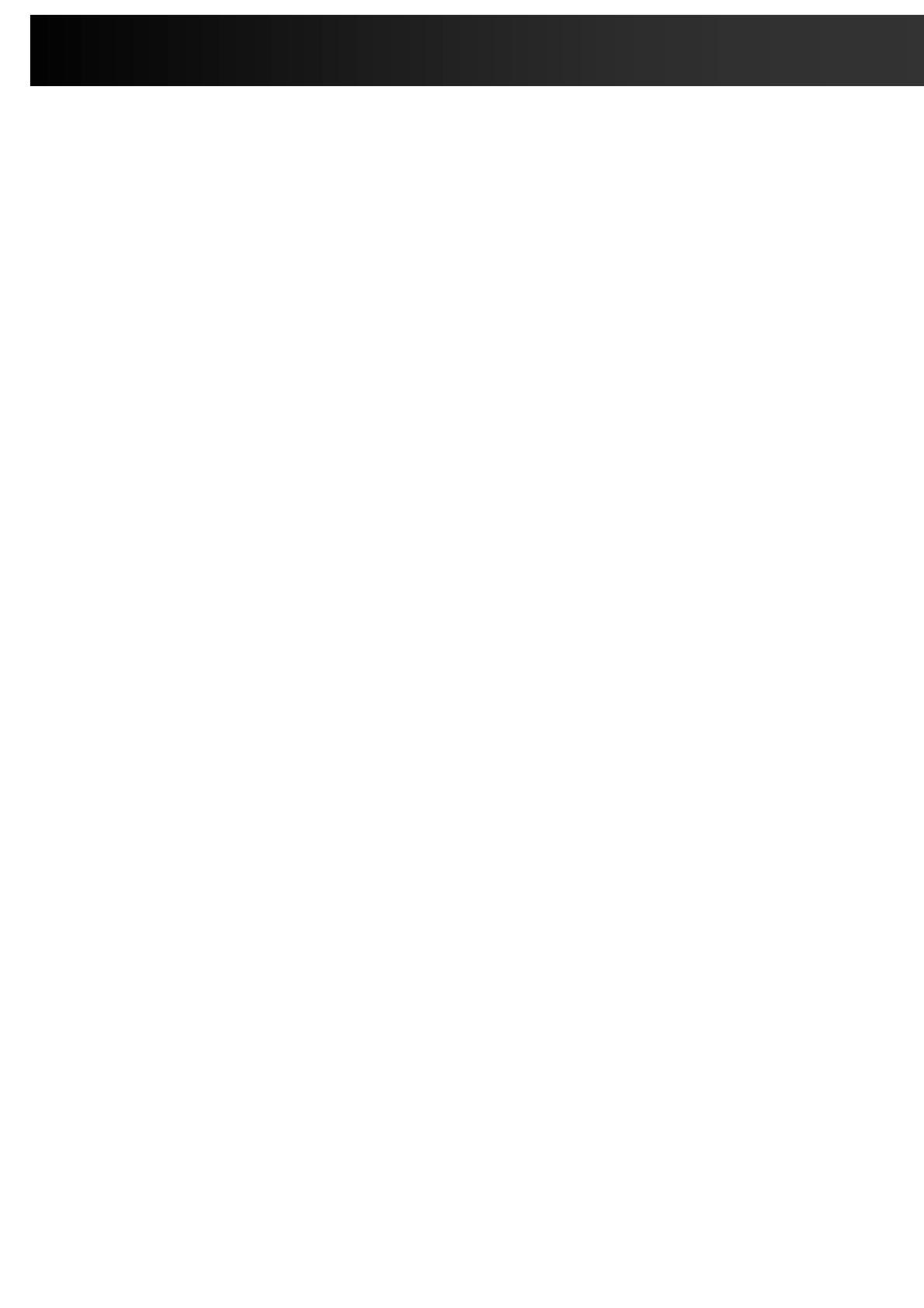
52 Heu VANG / thèse en génie Electrique
Optimisation des étapes technologiques pour la fabrication
des composants de puissance en SiC
Suivant la structure à réaliser, les étapes technologiques diffèrent. Au
CEGELY, une équipe travaille depuis 10 ans sur la réalisation de dispositifs de
puissance. Une étape clef a été étudiée amplement, le dopage localisé par
implantation ionique avec le recuit post-implantation pour activer les
dopants et recristalliser la structure [Laza 02]. Une thèse a été entièrement
consacrée à l’étude de la gravure sèche du SiC avec un réacteur plasma DECR
(Distributed Electron Cyclotronic Resonance) [Lano 97] en vue de la
réalisation notamment de la protection périphérique mesa ou encore de
MOSFET en tranchée appelé UMOSFET. Mais depuis, ce réacteur nous est
inaccessible et il a fallu se tourner vers un réacteur RIE plus classique pour
réaliser nos structures. Pour cela, le procédé a été optimisé par le choix d’un
masque de gravure très sélectif et d’une configuration du réacteur pour
atteindre une vitesse de gravure respectable afin de pouvoir graver
profondément. Les morphologies de la surface et des flancs de gravure sont
également analysées et le process a été optimisé en conséquence.
L’autre étape technologique clef étudiée dans cette thèse est la
métallisation afin de permettre le contact du semi-conducteur pour injecter
des porteurs dans le matériau. Il est connu que la formation de contact
ohmique est difficile dans les semi-conducteurs à grand gap notamment
concernant le type P. Le SiC ne fait pas exception à la règle. Si la réalisation
de contact sur le type N du SiC est relativement aisée puisque beaucoup de
publications font état d’une métallisation à base de Ni permettant d’avoir une
résistance spécifique très faible (10-5 Ω.cm2) [Gao 00][Han 02][Ferr 05], la
formation du contact ohmique sur le type P est plus problématique [Crof 02].
La difficulté réside dans le fait que le niveau de la bande de valence est
relativement élevé par rapport au vide. Et aucun métal ne possède un travail
de sortie proche de cette valeur. Des alliages sont donc nécessaires afin de
pouvoir réaliser un contact de qualité sur le SiC de type P.
Dans ce chapitre, nous allons dans un premier temps passer en revue les
principales étapes technologiques pour la fabrication des composants de
puissance en SiC. Puis une étude plus approfondie de la gravure profonde
plasma du SiC avec un réacteur RIE (Reactive Ion Etching) pour la mise en
place de la protection périphérique mesa est traitée. Ensuite, la dernière
partie sera consacrée à la réalisation des contacts ohmiques et plus
spécialement sur le SiC de type P.