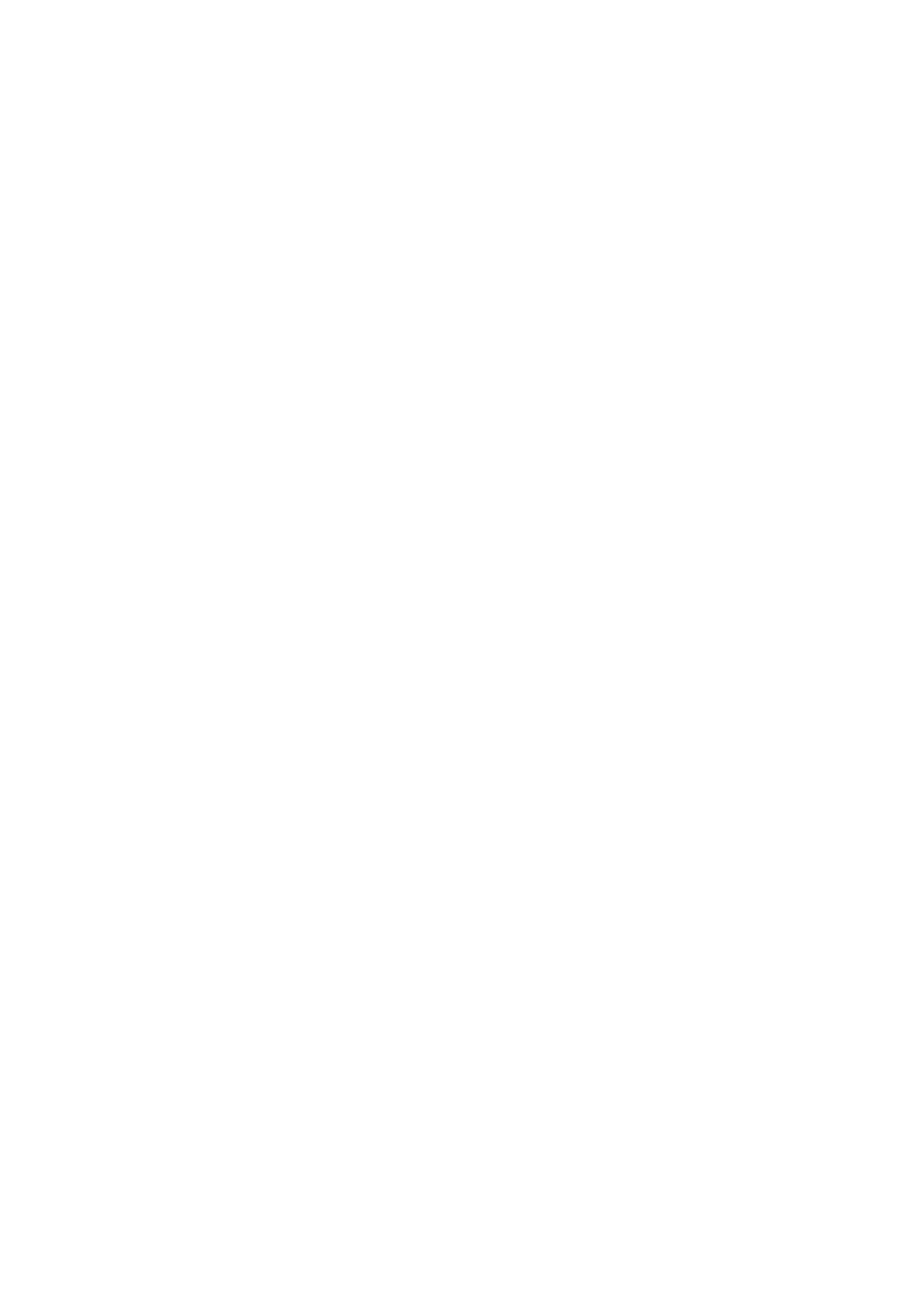
pour des installations à moyenne fréquence, ou à 2000 Volts pour des
installations à la fréquence réseau. Pour les installations à moyenne fréquence,
une tension fixe est appliquée secondairement et un commutateur à plots n’est
pas nécessaire. Pour les installations à la fréquence réseau, des commutateurs à
10 ou 12 plots sont mis en service. Les transformateurs sont surveillés par des
appareils fixes : thermomètre, surveillance de niveau d’huile, relais Buchholz
et déshumidificateur d’air.
Installation de commutation à la fréquence du réseau
b) Une installation de commutation à la fréquence du réseau consiste en une
combinaison de contacteur principal pour le circuit de courant principal, une
résistance d’amortissement pour la réduction du courant transitoire pouvant
être de 6 fois plus élevé que le courant nominal, le dispositif d’équilibrage avec
le self d’équilibrage, les condensateurs et les appareils de commutation pour
l’adaptation aux conditions de service, des condensateurs de compensation
avec des appareils de commutation pour une compensation réglée à cos phi = 1
et les câbles de connexion à la prise de four sur le mur. La commande est
exécutée au moyen des appareils dans l’armoire de commande.
Convertisseur à moyenne fréquence
c) Un convertisseur générant la moyenne fréquence exigée à partir de
l’alimentation réseau 50 Hz est nécessité pour un four à induction à moyenne
fréquence. A cet effet, une tension continue est générée dans un redresseur et
conduite vers l’inverseur via un self de lissage, une tension de moyenne
fréquence étant générée dans l’inverseur par des condensateurs de
compensation et l’inductivité de la bobine de four. L’électronique de
commande intégrée assure la régulation du convertisseur. Le four est
commandé par les appareils dans l’armoire de commande plus un processeur,
le cas échéant.
Alimentation en eau de refroidissement
d) Un système de refroidissement par eau, incluant un refroidissement de retour
de l’eau chauffée, est exigé pour la mise en service d’une installation de four à
induction. L’eau remise en circulation dans le circuit est chauffée de 34° C à
38° C env. dans le convertisseur plus les condensateurs et le self de lissage, et
sa température doit être ramenée à 34° C par un refroidisseur. Le débit de
pompage par les dispositifs électriques doit être d’env. 215 l/h par kW de
puissance perdue. L’eau est chauffée de 35°C à 62°C env. dans la bobine de
four et sa température doit être ramenée à 35°C dans un refroidisseur séparé.
Le débit de pompage par l’installation doit être d’env. 32 l/h par kW de
puissance perdue. En cas de panne de courant ou autre interruption, une
alimentation de secours en eau doit être montée pour le circuit du four. Un
chauffage doit être prévu quand le four est éteint en hiver.
Installation hydraulique
e) Pour la manoeuvre des vérins de basculement, de couvercle et de hotte, une
station hydraulique à pompes haute pression est exigée. Les vérins sont
commandés depuis le pupitre de commande par des commutateurs à levier