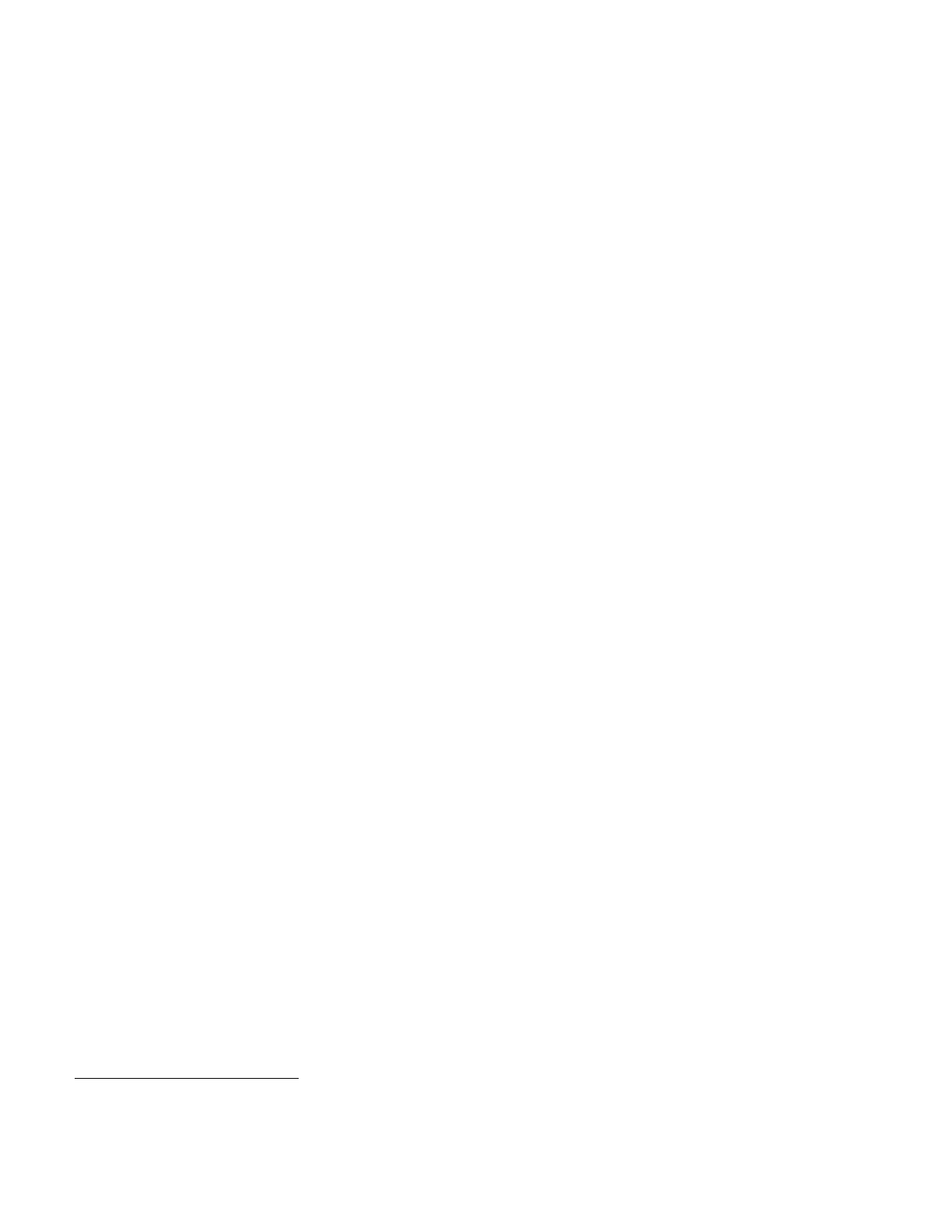
Abstract—Permanent magnet synchronous generators
(PMSGs) are commonly used as a variable speed generator in
wind energy systems. This paper describes a maximum power
point tracking (MPPT) scheme for a PMSG-based wind energy
conversion system (WECS) in which a buck-boost converter is
used to handle a wide range of wind speeds. A closed-loop with a
PWM inverter forces the WECS to extract the maximum power
available from the wind turbine by shifting the phase angle of
output voltage at a given wind speed. The output power is fed to
the grid. The mathematical model of the wind power system is
built and simulated by MATALB/SIMULINK software.
Simulation results show that the proposed control scheme has a
good dynamic performance and operates the wind generation
system with the maximum efficiency.
Index Terms—maximum power point tracking, permanent
magnet synchronous generator, phase shift, pulse width
modulation, wind energy
I. INTRODUCTION
ARIABLE-SPEED wind generation systems make it
possible to extract the maximum energy from wind with
widely varying speeds. The permanent magnet synchronous
generators (PMSGs) are suitable for small variable-speed wind
turbine generator systems. The wind generation system with a
PMSG represents one important trend of development for
wind power applications with numerous advantages like
higher efficiency due to the absence of field copper loss, lower
operating speed due to higher number of poles with smaller
pole pitch, and the elimination of gearbox [1], [2]. Smaller
wind turbines use fixed pitch angle without the need for
additional pitch control. The power from the wind energy
conversion system (WECS) is normally fed to an ac grid.
Like in any wind power system, it is desirable to extract the
maximum power available at a given wind speed. There are
different methods used to extract the maximum power from
the wind. Different control concepts for maximum power
point tracking (MPPT) in WECS with PMSG are described
and the performance for each is compared in [3]. The MPPT
methods can be broadly classified as those which use sensors
and those which do not use sensors. They are also classified
based on the type of control, such as fuzzy logic based control
[4] and sliding mode control [5].
Xin Wang and S. Yuvarajan are with the Department of Electrical and
Computer Engineering, North Dakota State University, Fargo, ND 58108
USA (email: xinwang28@hotmail.com; subbaraya.yuvarajan@ndsu.edu).
Lingling Fan is with the Department of Electrical Engineering, University
of South Florida, Tampa, USA (email: linglingfan@usf.edu).
To convert the variable-frequency output voltage from the
PMSG into an ac voltage of the grid frequency (60Hz), two
typical power converter topologies for small wind turbine
systems with PMSG are presented and explained in [6]. The
first configuration uses a diode-bridge rectifier, a boost
converter and an inverter; and the second configuration uses a
back-to-back converter system. The MPPT is implemented on
the dc-dc converter in the former system and on the PWM
inverter in the latter one. In the dc-dc converter, the duty cycle
is controlled, and in the PWM inverter the modulation index is
controlled, for MPPT. An input-output feedback linearization
(IOL) technique is applied to design the high-performance
nonlinear current controller on the PWM rectifier in [7]. A
sensorless MPPT control strategy on the PWM inverter is
implemented in [8], which is achieved without a wind speed
sensor and mechanical sensors such as rotor speed sensor and
position sensor. A new variable-speed WECS with a PMSG
and Z-source inverter is proposed in [9]. Compared to the
conventional WECS with boost converter, the number of
semiconductor switches used in [9] is reduced by one and the
system reliability is improved. Another nonlinear approach for
MPPT is also presented in [10]. It uses a matrix converter and
the controller is based on the nonlinear adaptive backstepping
method which is able to effectively accommodate the effects
of system uncertainties.
The paper proposes an MPPT scheme for a WECS with a
PMSG. The major advantage of using a PMSG is its ability to
handle a wide range of rotor speeds which correspond to a
large range of wind speeds. In a PMSG, the frequency and
amplitude of the output voltage vary with wind speed. In order
to maintain a narrow range of dc link voltage, the proposed
wind generation system uses a dc-dc converter with buck-
boost feature which can step up or step down the rectified
voltage by controlling its duty cycle. Also, in the PWM
inverter, another closed-loop is designed to accurately track
the maximum power point by shifting the phase angle of the
output voltage with respect to that of the grid voltage.
II. DESCRIPTION OF THE WECS SET UP
The functional block diagram of the proposed wind energy
MPPT system is shown in Fig. 1. The wind speed measured
using an anemometer is utilized to compute the maximum
MPPT Control for a PMSG-Based Grid-Tied
Wind Generation System
Xin Wang, Subbaraya Yuvarajan, Senior Member, IEEE, and Lingling Fan, Senior Member, IEEE
V