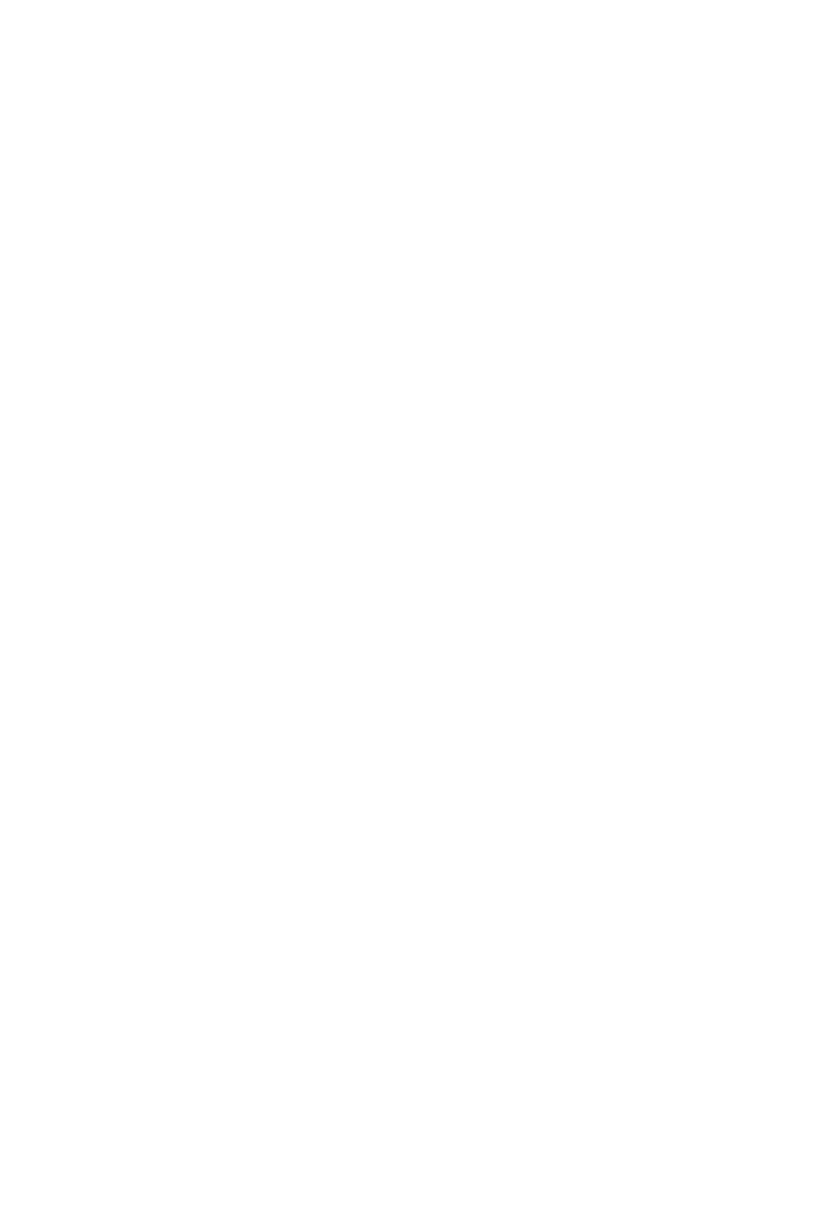
314 Recent Progress in Chemical Engineering
interest and awareness about the importance of alternative energy from
renewable sources, in particular for transportation fuels, and even an
increasing investment in research and development in this area. Examples
include bio-ethanol from the fermentation of starch or sugar rich
agricultural crops, vegetable oils from plants or microalgae and animal
fats, gasification of biomass, wind, hydroelectric power, solar power,
including photovoltaic energy, among many others (Dewulf and Van
Langenhove, 2006; Gilbert and Perl, 2008).
Nowadays biodiesel is the most important alternative diesel fuel in the
EU representing 82% of the total biofuel production (Bozbas, 2008) and
has been reported to emit substantially lower quantities of most of the
regulated pollutants compared to mineral diesel. When compared to fossil
fuels, their relative degree of development varies widely, and its potential
strongly depends on local conditions and sectors of activity where the energy
is used, making it difficult to select the best option and the design and
operation of renewable production systems. These questions are particular
acute in the transportation sector, a cornerstone of modern society and
one of the drivers of economic development, currently almost dependent
on fossil fuels and one of the main contributor to air pollution, in particular
to greenhouse gas (GHG) emissions (Akoh et al., 2007).
In fact fossil fuels are still the dominant source of energy used either
for domestic or industrial consumption and in the medium to long term
this situation will pose a growing threat, economic, societal, or
environmentally, to the ongoing development of human activities. There is
still no consensus among specialists, but it is common belief that the oil
peak is close and the existing reserves will be increasingly harder and more
expensive to explore in future (Laherrere, 2005). For example, tar sands
and coal are seen as valuable resources that may substitute oil, but they
will create far-reaching environmental problems, such as the destruction
of ecosystems and a significant increase in the carbon dioxide and sulphur
oxides emissions (Toman et al., 2008).
The soaring oil prices and growing concerns for the environment leaded
to an increased interest in other fuel sources. Among them, special attention
is given to energy sources such as biodiesel, hydrogen, and bio-ethanol, in
particular when produced from renewable raw materials (Girard and Fallot,
2006). However biofuel’s industry, too, have their critics, notably among
those concerned about the impact on food prices (when farm commodities
like maize, wheat, and sugarcane are diverted to energy), the conversion
of forests and other critical habitats for biofuel’s feedstocks cultivation with
the associated damage on biodiversity (depending on local biodiversity),
loss of soil quality or land fertility (depending on initial soil conditions),
emissions from carbon stock change (including both soil and vegetation),
and land competition (depending on local availability of land).
The increasing demand for biofuels and the fast-rising of energy costs
will require new and independent energy sources to be developed. This