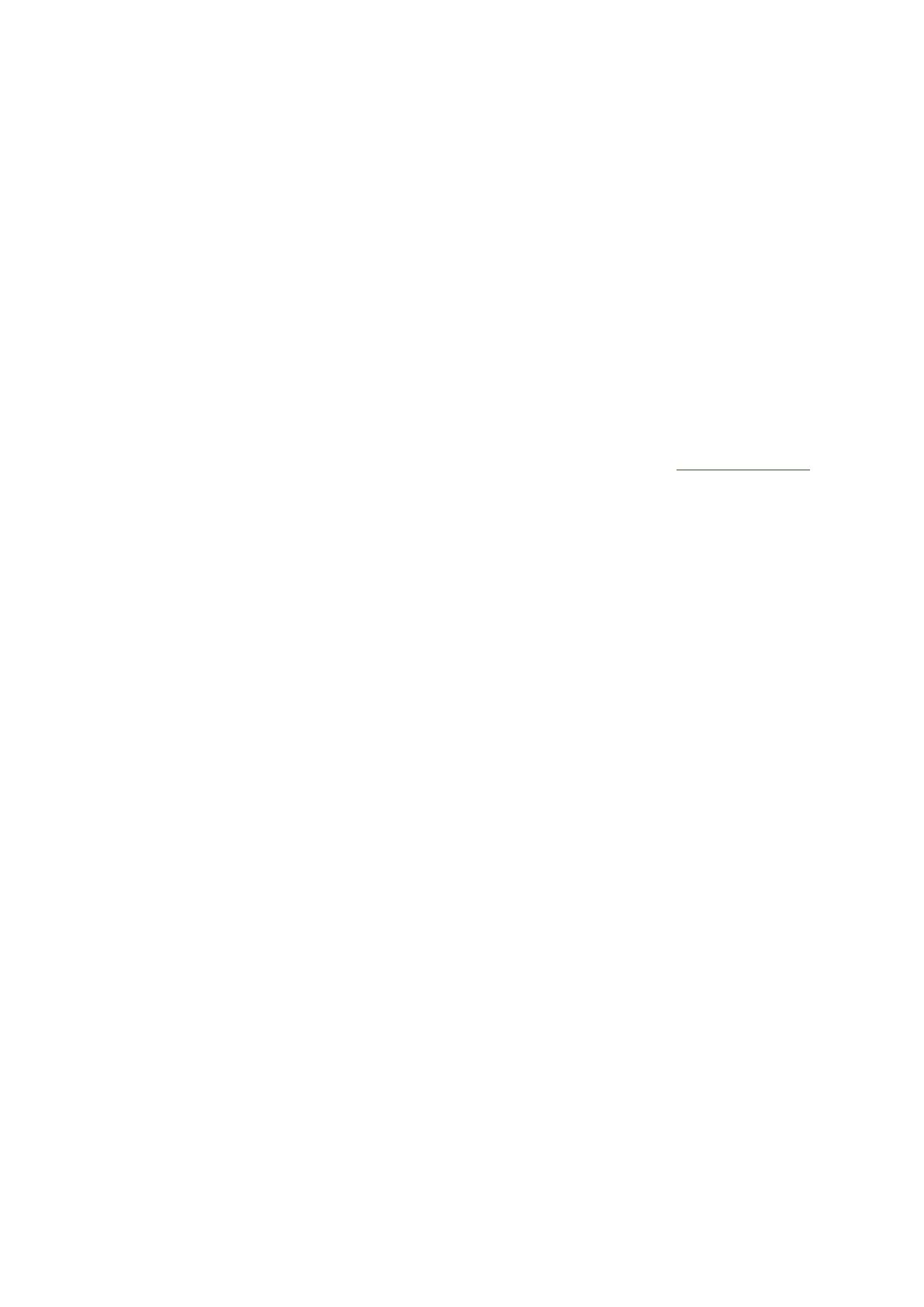
Ce qui suit explique le concept de résistance ou d'endurance à la fracture, ainsi que les paramètres
auxquels il est assujetti comme la température, le taux de déformation, la concentration de contraintes
ou encore le niveau de contrainte.
Des méthodes d'examen et d'essai mises à disposition des concepteurs pour apprécier l'aptitude à la
rupture fragile sont présentées, ainsi qu'une approche de la mécanique linéaire élastique de rupture.
Dans la conception de structures en matériaux ductiles, l'aptitude à résister à la charge de manière
sécurisée est basée sur l'analyse des contraintes de façon à assurer que la contrainte nominale reste
confinée dans le domaine élastique du matériau. Des ruptures qui surviennent à l'intérieur de ce domaine
élastique (en deçà de la limite d'élasticité du matériau) sont classées comme ruptures fragiles. Ces
ruptures peuvent s'initier à partir de petits défauts de continuité au sein du matériau (ligne d'inclusions
intermétalliques par exemple) ou de défauts de type fissure qui n'altèrent pas grandement la distribution
de la contrainte nominale et qui ne sont habituellement pas pris en considération dans l'analyse de
contrainte.
Pour un taux de chargement très élevé, une discontinuité peut fortement diminuer la bonne ductilité du
matériau prédite par un essai de traction satisfaisant réalisé sur éprouvettes usinées (sans défaut de
surface et aux contours arrondis) et provoquer la ruine de la structure par rupture fragile. C'est ce mode
de rupture qui est à l'origine du tragique accident survenu à la plateforme pentagone Alexander Kielland.
Il devient par conséquent évident qu'une conception saine doit bannir toutes les discontinuités
(singularités), ce qui reste difficile en construction soudée et surtout en construction moulée.
Pour beaucoup de structures traditionnelles comme les bateaux, les ponts et les équipements sous
pression, l'expérience de la conception, des matériaux et des modes de fabrication ont permis d'établir
une corrélation satisfaisante, pour le matériau, entre réussite à l'essai de flexion par choc standard sur
éprouvette entaillée et bonne tenue en service.
Dans le domaine aéronautique, l'analyse de fatigue permet souvent de prévoir la durée de vie à
l'amorçage des fissures. On utilise donc la phase de propagation de fissure pour réaliser des inspections
en prévention de la rupture dont les intervalles sont définis par la mécanique de la rupture.
Une des motivations en faveur de l'application des concepts de la mécanique de la rupture et des essais
à réaliser sur joints soudés ou pièces moulées est d'être en mesure de se prémunir, dès la phase de
conception, des effets produits par les discontinuités présentes. Il est largement reconnu que les joints
soudés et les pièces moulées comportent toujours un certain nombre de discontinuités, ce qui place le
concepteur devant un dilemme. Le concepteur souhaitera toujours utiliser des joints soudés ou des pièces
moulées exempts de discontinuités, ce qui n'est absolument pas réaliste.
L'approche pratique consiste à reconnaître la présence de ces discontinuités au sein des assemblages et
de déterminer une taille critique à partir de laquelle une discontinuité devient préjudiciable, autrement
dit à partir de laquelle il faut les rechercher et les éliminer. Mais comment décider à partir de quelle
dimension critique une discontinuité a toutes les probabilités de devenir préjudiciable ?
Étant donné que la méthode conventionnelle d'essai de flexion par choc n'est plus appropriée, les
méthodes d'essais issues de la mécanique de la rupture (essais de fracture), lorsqu'ils sont applicables,
peuvent contribuer à établir une corrélation entre taille critique d'une discontinuité et contrainte de
rupture pour un matériau ou une soudure donné et donc permettre une estimation directe de la taille des
défauts acceptables pour différentes configurations et conditions de fonctionnement. Cependant,
l'évolution permanente des matériaux (matériaux à haute limite d'élasticité), les conceptions de plus en
plus complexes et les nouvelles technologies de soudage ou de moulage font que les ingénieries ne
peuvent pas avoir le recul nécessaire sur le comportement de ces nouvelles conceptions et les contraintes
attendues pas forcément attestées. En conséquence il y aura toujours une grande nécessité, pour le
concepteur, à traiter de manière analytique le problème des discontinuités.