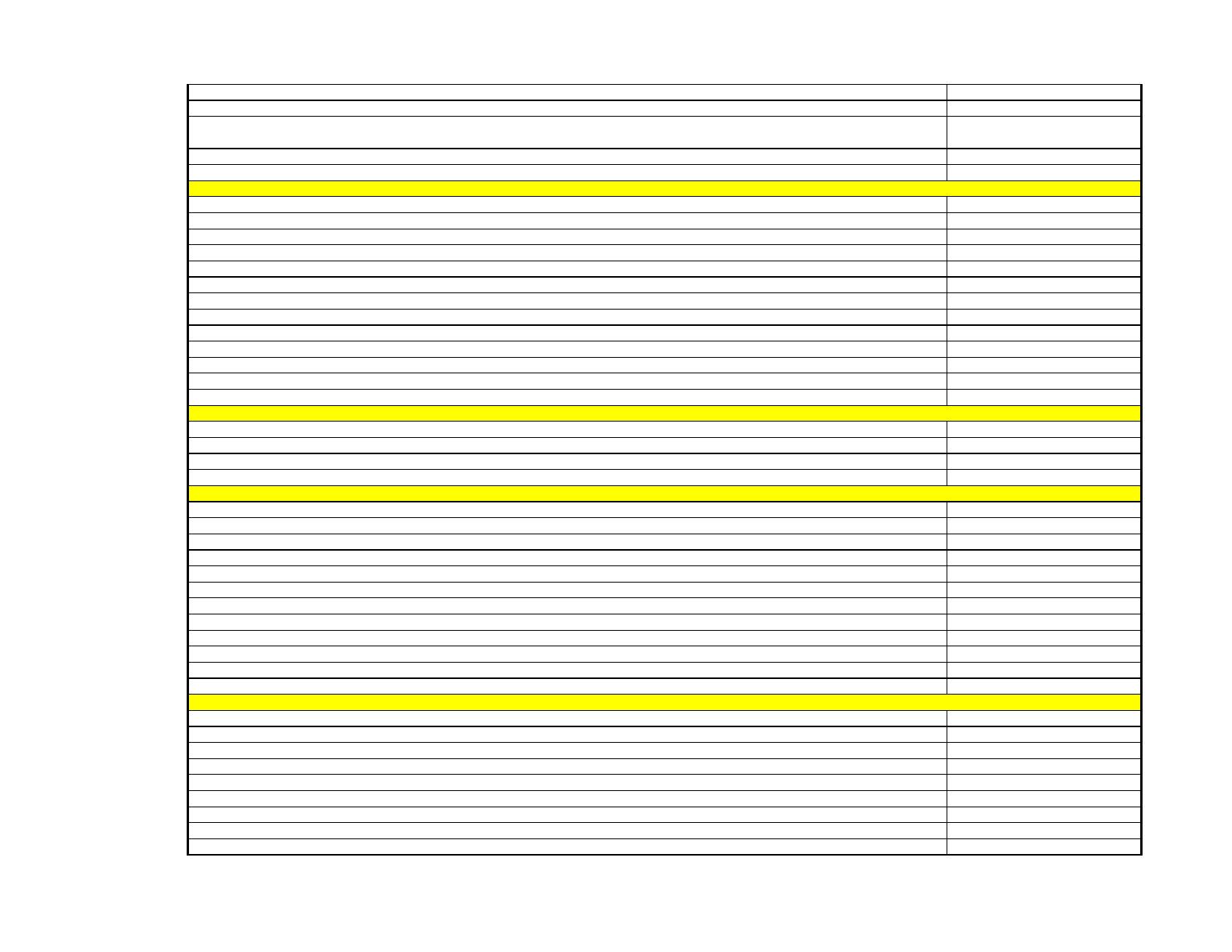
145.895
113.229
6.033
880.128
683.065
0.063
331.030
15.657
1655.151
78.283
0.028
97.263
75.486
486.317
377.429
6.868
4.545
9.089
622.000
463.593
285.512
286.209
47.000
1.060
1.000
1.000
1.150
57.293
1969.493
‐1.200
0.200
64.000
176.467
762.588
463.593
18310.675
39.497
762.588
24.011
286.209
13197.315
46.111
762.588
BasicwindspeedVbm/s(annexA/clause6.2,page51)
k1(table1/clause6.3.1,page7)
k2(table2/clause6.3.2.2,page8)
k3(clause6.3.3.1,page8)
k4(clause6.3.4,page9)
ConvectivebaseshearintankemptyconditionKn(API6502020,E.6.1‐3,pageE‐16)
OverturningmomentintankfullconditionaboutouterraftedgekN‐m(onlywind,noseismic
Factorofsafetyagainstoverturningwhenthetankisfullofethanol(onlywind,noseismic
OverturningmomentsintankemptyconditionaboutouterraftedgekN‐m(onlywind,noseismic
OverturningmomentsintankemptyconditionaboutouterraftedgekN‐m(onlyseismic,nowind
Factorofsafetyagainstoverturningintankemptycondition(onlyseismic,nowind
SumofrestoringmomentsintankfullconditionaboutouterraftedgekN‐m
7.Combinedseismicanalysis‐impulsive,convectiveandverticalwhentankisfullandempty
CombinedbaseshearactingintankfullconditionkN
SurchargepressureintankfullconditionduetoverticalseismicforcekN/sq.m
TotaludlforceonwallduetoverticalsurchargeoutwardskN/m
Momentexertedatwall‐raftinterfaceduetoverticalsurchargekN‐m
Factorofsafetyagainstoverturningwhenthetankisfullofethanol(onlyseismic,nowind
SumofrestoringmomentsintankemptyconditionaboutouterraftedgekN‐
OverturningmomentintankfullconditionaboutouterraftedgekN‐m(onlyseismic,nowind
CombinedoverturningslabmomentintankfullconditionkN‐m(API6502020,E.6.1.5‐2,pageE‐20)
MomentexertedatraftBOCbyseismicforceinconvectivemodeintankfullconditionkN‐m
CombinedbaseshearactingintankemptyconditionkN
8.Windanalysis(samefortankfullandtankemptyconditions,IS875part3:2015)
Heightabovebaseplatesatwhichthecenterofactionofslaboverturningmomentliesinconvectivemodem(API6502020,clauseE.6.1.2.2‐3,
pageE‐18)
MomentexertedbyverticalseismicforceinimpulsivemodeaboutouteredgeofraftkN‐mintankfullconditio
Verticalseismicforceinimpulsivemodeintankfullcondition,kN
ConvectivebaseshearintankfullconditionKn(API6502020,E.6.1‐3,pageE‐16)
Verticalseismicforceinimpulsivemodeintankemptycondition,kN
MomentexertedbywindloadaboutraftTOCkN‐m
9.Checkforoverturningofringwallintankfullandemptyconditions
WindloadactingonshellkN(clause7.3.1,page10)
DesignwindpressurePzN/sq.m(clause7.2,page9)
ExternalpressurecoefficientCpe(table5,page13)
6.Verticalseismicanalysiswhentankisfullandempty(IS1893part1:2016,IS1893part2:2014,API650:2020)
MomentexertedatraftBOCbyseismicforceinconvectivemodeintankemptyconditionkN‐m
Effectivefrontalareanormaltowindforcesq.m
CombinedoverturningslabmomentintankemptyconditionkN‐m(API6502020,E.6.1.5‐2,pageE‐20
MomentexertedbyverticalseismicforceinimpulsivemodeaboutouteredgeofraftkN‐mintankemptyconditio
Designverticalaccelerationcoefficientinimpulsivemode(IS1893part22014,clause4.10.1,page10)
DesignwindspeedVzm/s(clause6.3,page5)
Designverticalaccelerationcoefficientinconvectivemode(IS1893part22014,clause4.10.1,page10
Verticalseismicforceinconvectivemodeintankfullcondition,kN
Verticalseismicforceinconvectivemodeintankemptycondition,kN
MomentexertedbyverticalseismicforceinconvectivemodeaboutouteredgeofraftkN‐mintankfullconditio
MomentexertedbyverticalseismicforceinconvectivemodeaboutouteredgeofraftkN‐mintankemptyconditio
InternalpressurecoefficientCpi(clause7.3.2.1,page11)