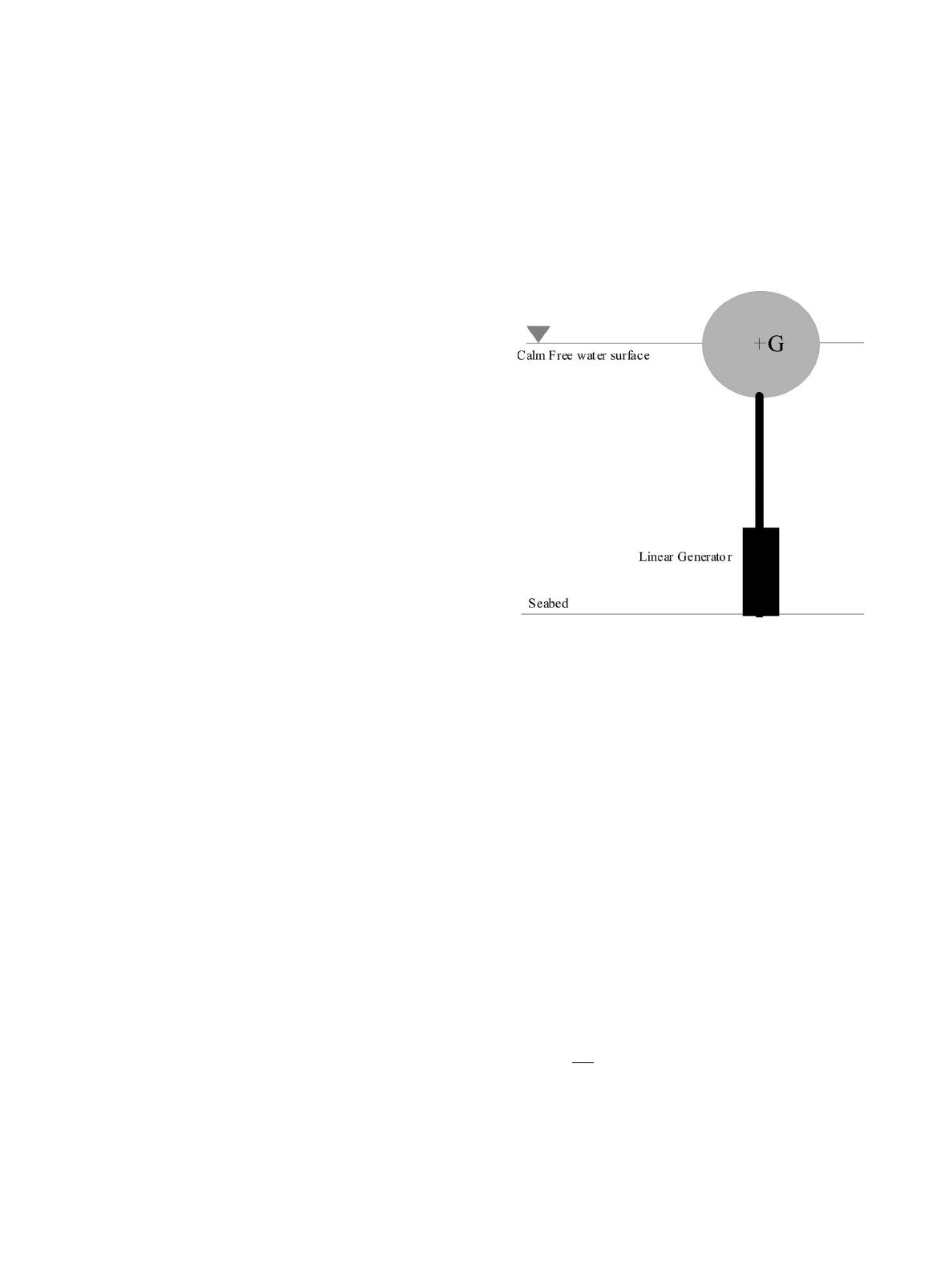
1152 IEEE TRANSACTIONS ON INDUSTRIAL ELECTRONICS, VOL. 53, NO. 4, AUGUST 2006
A Tubular-Generator Drive For
Wave Energy Conversion
Vincenzo Delli Colli, Piergiacomo Cancelliere, Member, IEEE, Fabrizio Marignetti, Member, IEEE,
Roberto Di Stefano, and Maurizio Scarano, Member, IEEE
Abstract—This paper illustrates the operation of a tubular-
machine drive as a linear generator for a heave-buoy wave energy
conversion. Linear generators, which are adopted in marine power
plants, offer the advantage of generating without introducing any
conversion crank gear or hydraulic system. The use of a tubular-
machine topology allows the electromagnetic thrust density to be
improved. This paper briefly summarizes the principles of marine
wave buoy interaction and reports the design analysis and control
of a permanent-magnet (PM) synchronous tubular linear machine
based on a scaled generator prototype and on a rotating simulation
test bench.
Index Terms—Heave buoy, linear synchronous generators,
marine energy, tubular generators.
I. INTRODUCTION
THE USE of a tubular machine as a linear generator for a
heave-buoy wave energy conversion in order to improve
the force density N/m3that can be attained is proposed in
this paper.
Linear machines are increasingly used today as generators.
In fact, some energy sources and especially marine ones exhibit
an alternating motion. One of the most promising renewable
energy sources characterized by a reciprocating motion is rep-
resented by tide and wave marine energy [1]–[4].
Linear generators are suitable for direct-drive applications,
since they permit a reduction in the number of subsequent
energy transformation steps. Coupling an electrical generator
directly with the reciprocating energy source also permits the
reduction of moving parts and simplifies the system. The overall
efficiency is thereby enhanced.
Different electrical-machine topologies have been proposed
in literature to be utilized as direct-drive linear generators [5].
One encouraging way to convert an alternating mechanical
energy into an electrical energy by means of a direct drive is
to use a linear tubular synchronous permanent-magnet (PM)
generator. The force-to-weight ratio of such machines has been
proved to be higher than the flat linear topology [6].
Section II summarizes the basic principles of the heave-
buoy mechanics, whereas, Section III outlines the design of
the proposed tubular generator and presents the results of the
finite-element analysis (FEA) together with the experimental
validation. Section IV presents the optimal buoy control, which
Manuscript received March 29, 2005; revised June 28, 2005. Abstract
published on the Internet May 18, 2006.
The authors are with the Department of Automation (DAEIMI), Fac-
ulty of Engineering, University of Cassino, 03043 Cassino, Italy (email:
Digital Object Identifier 10.1109/TIE.2006.878318
Fig. 1. Semisubmerged sphere as marine wave energy converter.
allows the sea-to-buoy power transfer to be maximized, and
Section V discusses the drive control used to perform the
electromechanical and ac/dc conversion control. Finally, Sec-
tion VI presents the test facility, and Section VII gives the
results of the experiments on mechanical to dc power conver-
sion obtained by means of a tubular prototype as well as the
results of the wave conversion obtained by a rotating simulation
test bench.
II. HEAVE-BUOY MECHANICS
In this paper, a simple heave-buoy system is considered as
a wave energy converter (WEC). There are many shapes for
the buoy as a WEC: a sphere-shaped buoy is considered in
the following. Generally, buoy WECs can be displaced in any
direction when an incident wave occurs; in this formulation, the
buoy WEC is restricted to oscillate in the heave mode only, as
shown schematically in Fig. 1.
The equation of motion for a simple heaving-buoy device is
Md2
dt2z=Fe+Fr+Fb+Fv+Ff+Fu(1)
where Mis the mass of the buoy, Feis the excitation force
due to the incident wave on the buoy, Fris the radiated force,
Fbis the hydrostatic buoyancy force, Fvand Ffrepresent
unavoidable viscous and friction effects, respectively, and Fuis
an outside force that could be externally imposed. The zheave
0278-0046/$20.00 © 2006 IEEE
Authorized licensed use limited to: Université de Lorraine. Downloaded on November 20,2021 at 14:54:57 UTC from IEEE Xplore. Restrictions apply.