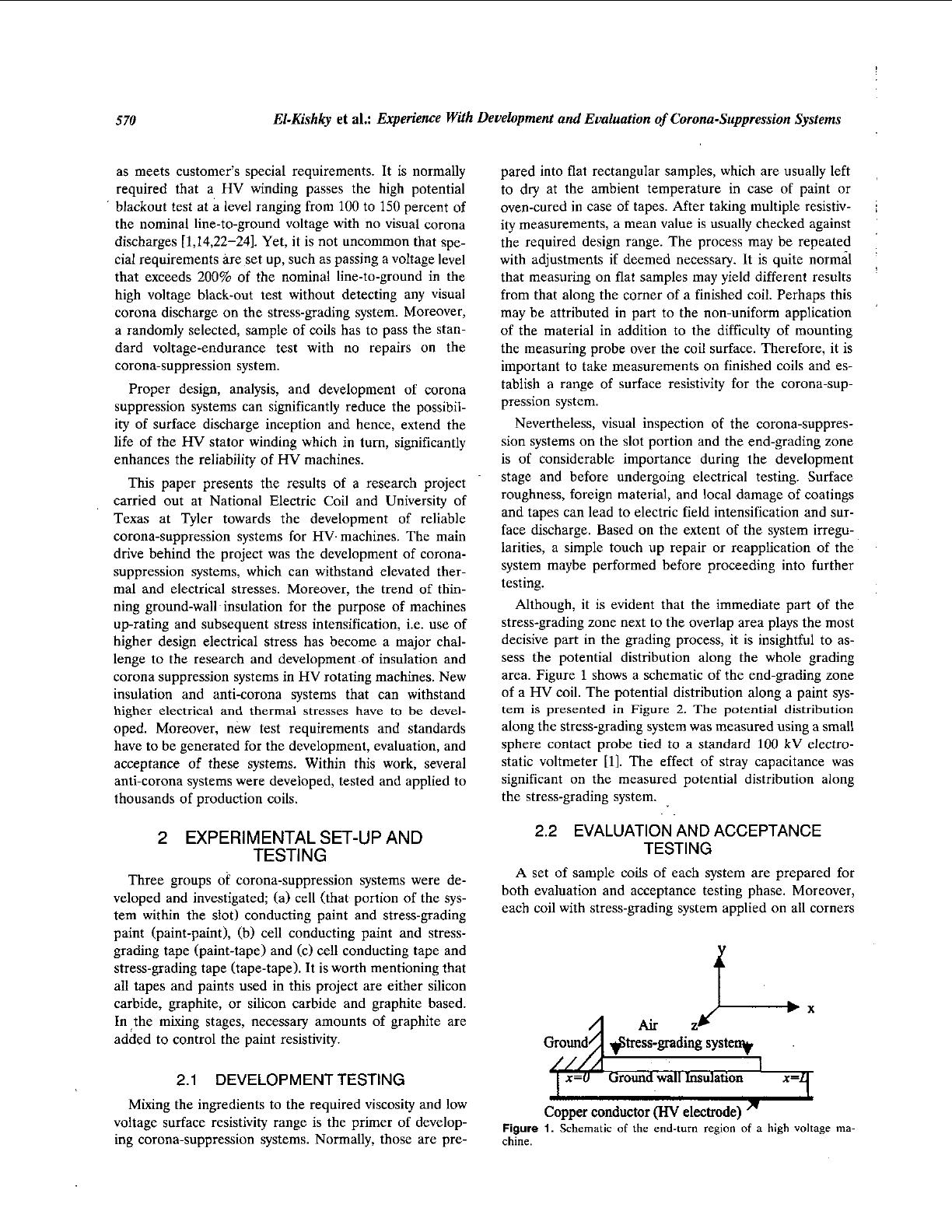
570
El-Kishky
et
al.:
Experience With Development and Evaluation
of
Corona-Suppression Systems
as
meets customer’s special requirements. It is normally
required that a HV winding passes the
high
potential
blackout test
at
a level ranging from
100
to
150
percent of
the nominal line-to-ground voltage with
no
visual corona
discharges
[1,14,22-241.
Yet, it is not uncommon that spe-
cial requirements are set up, such as passing a voltage level
that exceeds 200%
of
the nominal line-to-ground in the
high voltage black-out test without detecting any visual
corona discharge on the stress-grading system. Moreover,
a randomly selected, sample of coils has to pass the stan-
dard voltage-endurance test with no repairs on the
corona-suppression system.
Proper design, analysis, and development of corona
suppression systems can significantly reduce the possibil-
ity of surface discharge inception and hence, extend the
life of the HV stator winding which
in
turn, significantly
enhances the reliability
of
HV machines.
This paper presents the results of a research project
carried out at National Electric Coil and University of
Texas at Tyler towards the development of reliable
corona-suppression systems for HV machines. The main
drive behind the project was the development of corona-
suppression systems, which can withstand elevated ther-
mal and electrical stresses. Moreover, the trend of thin-
ning ground-wall insulation for the purpose of machines
up-rating and subsequent stress intensification, i.e. use of
higher design electrical stress has become a major chal-
lenge to the research and development of insulation and
corona suppression systems in HV rotating machines. New
insulation and anti-corona systems that can withstand
higher electrical and
thermal
stresses
have
to
be
devel-
oped. Moreover, new test requirements and standards
have to be generated for the development, evaluation, and
acceptance of these systems. Within this work, several
anti-corona systems were developed, tested and applied to
thousands of production coils.
2
EXPERIMENTAL SET-UP AND
TESTING
Three groups of corona-suppression systems were de-
veloped and investigated; (a) cell (that portion of the sys-
tem within the
slot)
conducting paint and stress-grading
paint (paint-paint), (h) cell conducting paint and stress-
grading tape (paint-tape) and (c) cell conducting tape and
stress-grading tape (tape-tape). It is worth mentioning that
all tapes and paints used in this project are either silicon
carbide, graphite, or silicon carbide and graphite based.
In the mixing stages, necessaly amounts of graphite are
added to control the paint resistivity.
2.1
DEVELOPMENT TESTING
Mixing the ingredients to the required viscosity and low
voltage surface resistivity range is the primer of develop-
ing corona-suppression systems. Normally, those are pre-
pared into flat rectangular samples, which are usually left
to dry at the ambient temperature in case of paint or
oven-cured
in
case of tapes. After taking multiple resistiv-
ity measurements, a mean value is usually checked against
the required design range. The process may be repeated
with adjustments
if
deemed necessaly. It
is
quite normal
that measuring
on
flat samples may yield different results
from that along the corner of a finished coil. Perhaps this
may be attributed
in
part to the non-uniform application
of the material
in
addition to the difficulty of mounting
the measuring probe over the coil surface. Therefore, it is
important to take measurements
on
finished coils and es-
tablish a range of surface resistivity for the corona-sup-
pression system.
Nevertheless, visual inspection of the corona-suppres-
sion systems on the slot portion and the end-grading zone
is of considerable importance during the development
stage and before undergoing electrical testing. Surface
roughness, foreign material, and local damage of coatings
and tapes can lead to electric field intensification and
SUI-
face discharge. Based on the extent of the system irregu-
larities, a simple touch up repair or reapplication of the
system maybe performed before proceeding into further
testing.
Although, it is evident that the immediate part of the
stress-grading zone next to the overlap area plays the most
decisive part in the grading process, it is insightful to as-
sess the potential distribution along the whole grading
area. Figure
1
shows a schematic of the end-grading zone
of a HV coil. The potential distribution along a paint sys-
tem
is presented
in
Figure
2.
The
potential
distribution
along the stress-grading system was measured using a small
sphere contact probe tied
to
a standard
100
kV electro-
static voltmeter
[l].
The effect of stray capacitance was
significant on the measured potential distribution along
the stress-grading system. .~
2.2
EVALUATION AND ACCEPTANCE
TESTING
A set of sample coils of each system are prepared for
both evaluation and acceptance testing phase. Moreover,
each coil with stress-grading system applied
on
all corners
V
f
Ground
+tress-grading
systev
Copper
conductor
(HV
electrode)
Figure
1.
Schematic
of
the
end-turn
region
of
a
high
voltage
ma-
chine.