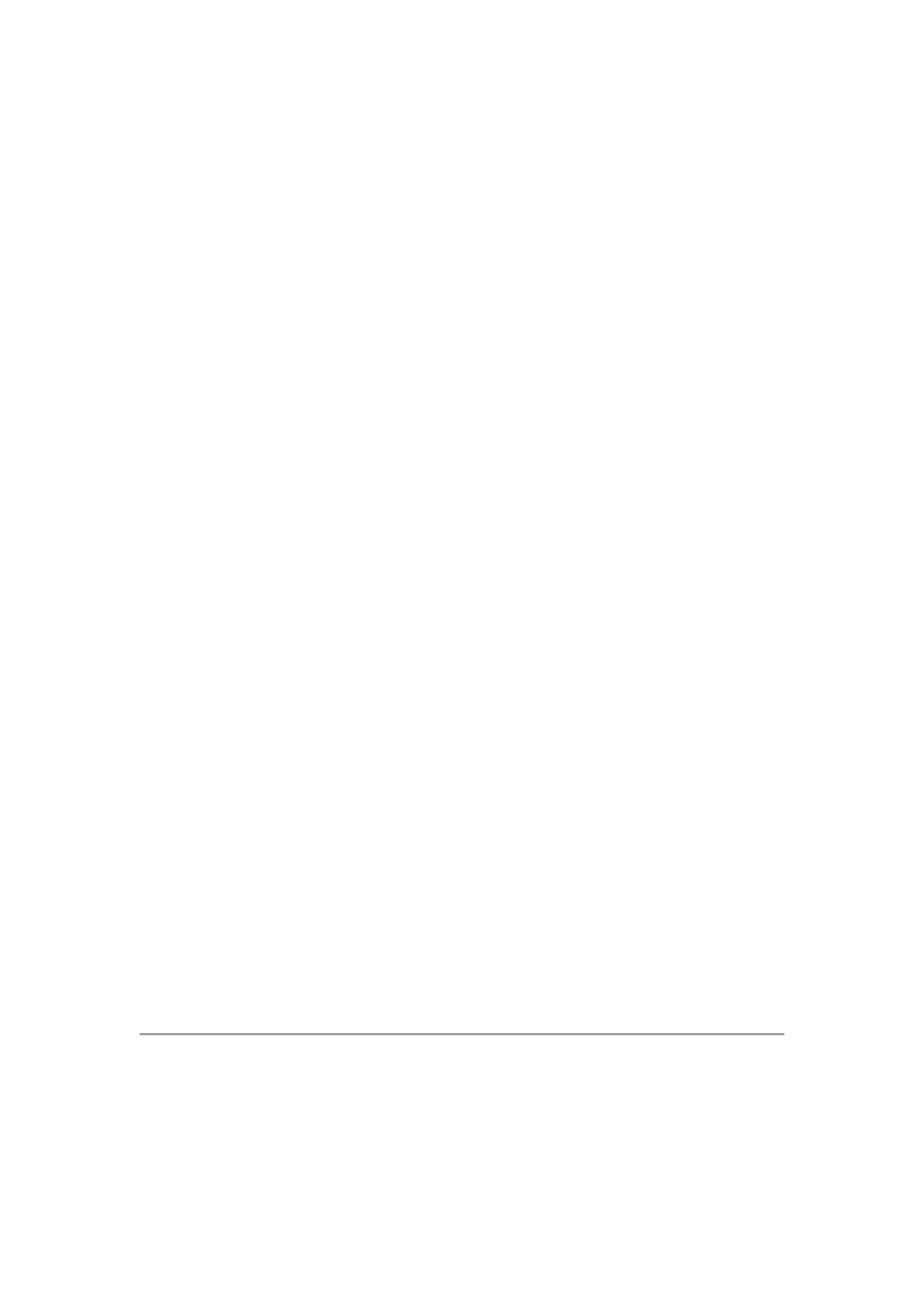
Avoid ground loops. Do not paint ground points.
The following publications may provide additional information:
IEEE Standard 142" Recommended Practice for Grounding of Industrial and
Commercial Power Systems"
IEEE Standard 1100" Recommended Practice for Powering and Grounding
Sensitive Electronic Equipment"
Electrical codes and service publications may provide additional requirements.
Shielded Wiring
The following considerations are the primary purposes for grounding equipment:
Safety of personnel
Improved equipment operation
Continuity of service
There are four main reasons for having grounded systems:
Safety
Protection against a lightning strike
Reduction in the emission of noise
Integrity of the signal
Terminate the following shields at one end only. Limit the length of the shields'
breakouts to less than 50.8 mm (2 inches).
The shield for the input signal from the synchronizer must be connected to
terminal 21 on the module. Leave the shield floating at the synchronizer's end.
The shield for the speed trim potentiometer must be connected to terminal 21
on the module. Leave the shield floating at the potentiometer end.
The shield for the pulse width modulated output (PWM) must be connected to
terminal 21 on the module. Leave the shield floating at the engine control's
end.
Always connect the shield for the load share module to terminal 12 on the module.
This terminal is not chassis ground. Never connect the shield for the load share
module to chassis ground. Refer to the wiring diagram in Illustration 2.