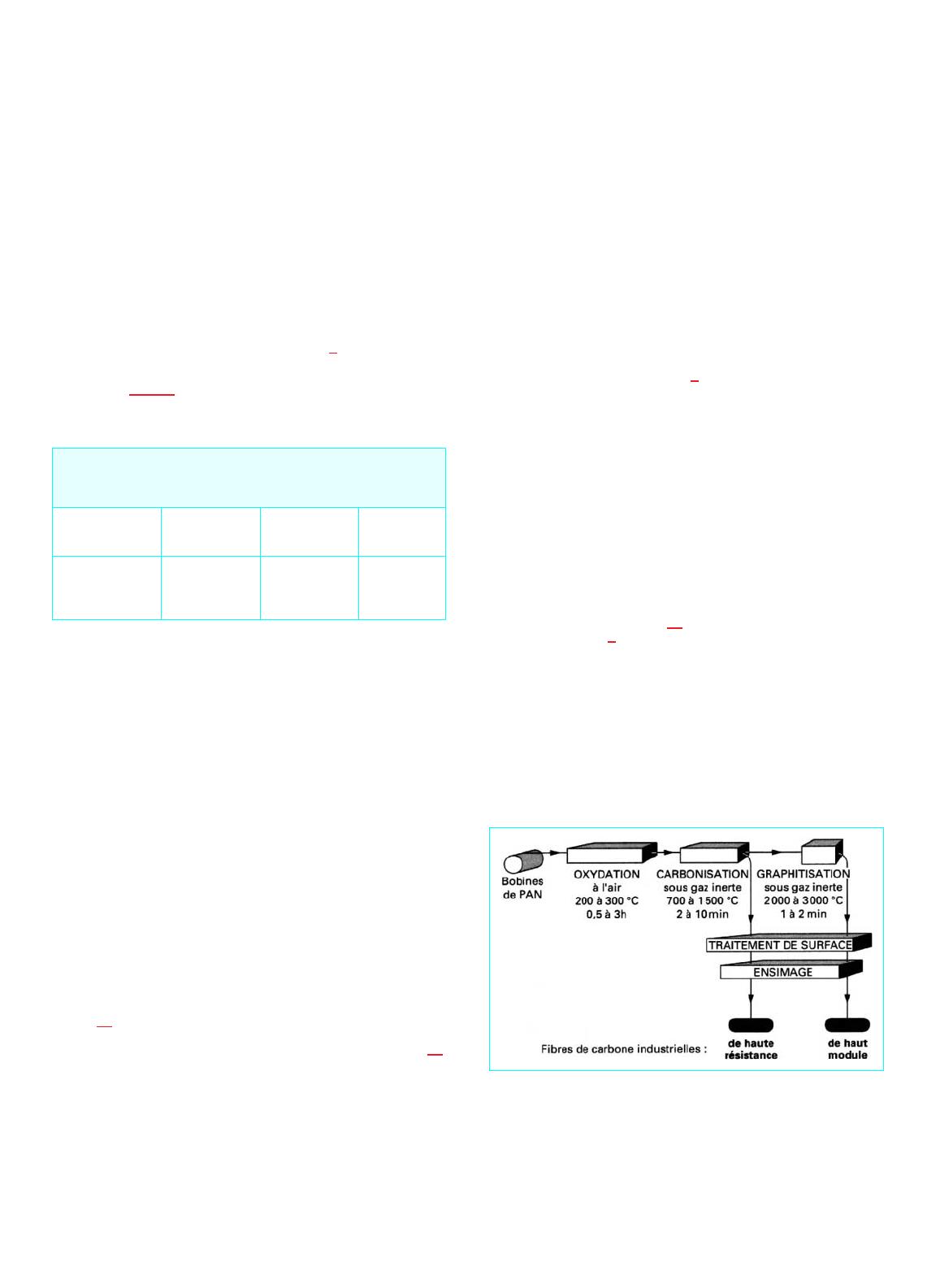
___________________________________________________________________________________________________________________ FIBRES DE CARBONE
Toute reproduction sans autorisation du Centre français d’exploitation du droit de copie est strictement interdite.
© Techniques de l’Ingénieur, traité Plastiques et Composites A 2 210 − 3
1.1 Fibres obtenues à partir de rayonne
Les premières fibres de carbone étaient fabriquées à partir de
tresses, de tissus ou d’un mat de fibres de rayonne, l’ensemble étant
agrafé sur un cadre rigide et chauffé dans une première étape
à 1 000-1 500 oC pour transformer la cellulose en carbone sous
atmosphère inerte, puis à 2 000-2 500 oC pour obtenir une meilleure
résistance à l’oxydation à température élevée. Aucune tension
particulière n’était appliquée pendant le traitement thermique ; c’est
pourquoi les propriétés mécaniques des fibres de carbone obtenues
n’étaient pas aussi élevées que celles obtenues aujourd’hui à partir
d’un précurseur sous tension contrôlée pendant le traitement ther-
mique vers 1 500 oC. De plus hauts modules et de plus hautes téna-
cités furent en effet obtenus en augmentant la tension et les
températures du traitement thermique (tableau 1). La production de
ces fibres cessa lorsqu’elles perdirent leur compétitivité économique
vis-à-vis des fibres de carbone obtenues à partir de PAN et de brais
mésophases (§ 1.3.2). Les principales raisons en étaient le coût des
matières premières et des procédés, le tout accentué par les pro-
priétés mécaniques moins performantes des fibres. (0)
1.2 Fibres obtenues à partir de PAN
1.2.1 Précurseur
Les fils de polyacrylonitrile (PAN) précurseur sont fabriqués
selon la technologie bien établie de polymérisation et de filage des
fibres acryliques à usage textile par voie solvant, mais avec des dif-
férences sensibles.
Différents comonomères peuvent être utilisés, par exemple
l’acrylate ou le méthacrylate de méthyle, et leurs taux varient d’un
fabricant à l’autre. Ces comonomères sont aussi choisis pour favo-
riser la stabilisation du précurseur lors de l’étape d’oxydation et pour
éviter la fusion des monofilaments. Pour les mêmes raisons, les fila-
ments du précurseur sont généralement recouverts d’un agent de
protection (finish) tel un corps gras ou un produit siliconé, qui a pour
but d’éviter la fusion, de prévenir le collage des filaments entre eux
et de participer éventuellement au mécanisme d’oxydation en
limitant l’effet exothermique.
Chaque fabricant utilise un solvant du PAN et une solution coa-
gulante différente. Ces choix, liés aux procédés, sont importants car
ils déterminent la pureté du PAN qui est directement liée à sa stabilité
thermique. La forme et le diamètre du monofilament dépendent de
la forme et du diamètre de la filière utilisée ainsi que du couple
solvant/solution coagulante. Différents degrés de régularité de sur-
face peuvent être obtenus selon le solvant et la solution coagulante
utilisés [3]. La nature des impuretés métalliques présentes dans la
fibre de carbone dépend des impuretés présentes dans le PAN pré-
curseur et des sels utilisés lors de la fabrication du précurseur [4].
À titre indicatif, les fibres d’Hercules (USA), IM-6G et ASA-W,
contiennent environ 1 000 ppm de sodium (soit 0,1 % en masse), ce
qui fait penser à l’utilisation de comonomères contenant du sodium.
La fibre de BASF, le Celion G-40X, contient plus de 100 ppm de zinc
provenant vraisemblablement du chlorure de zinc en solution
aqueuse employé pour dissoudre le PAN.
Après filage, les monofilaments peuvent être étirés jusqu’à 500 %
d’allongement, afin de leur conférer une orientation axiale préfé-
rentielle. Cette opération est souvent accompagnée de traitements
à chaud par passage sur des rouleaux chauffants ou dans de la
vapeur d’eau.
La plupart des précurseurs PAN sont constitués de 1 000 à 1 200
filaments d’environ 0,16 tex ou mg/m et d’un diamètre de 10 à 20 µm.
Certains précurseurs PAN peuvent contenir 24 000 ou 48 000, voire
320 000 filaments comme dans les PAN à usage textile, mais ils ne
permettent pas d’obtenir des fibres de carbone à très hautes
performances.
1.2.2 Traitements thermiques
L’ensemble du procédé d’obtention des fibres de carbone à partir
de PAN est présenté sur la figure 1.
1.2.2.1 Oxydation
L’étape d’oxydation du précurseur s’effectue dans un four régulé
sous air, à des températures se situant entre 200 et 300 oC pendant
un temps pouvant varier de 30 min à 3 h, selon les profils temps-
températures propres à chaque procédé. L’oxydation du PAN est une
réaction fortement exothermique (dégageant jusqu’à 3 800 kJ/kg).
Elle exige un contrôle très rigoureux de la cinétique si l’on veut éviter
la fusion des monofilaments. Lors de l’oxydation, le précurseur, dont
la masse apparente n’augmente que de quelques pour-cent, subit
de très profondes modifications physiques et chimiques. Les fila-
ments de PAN passent d’un état plastique à un état infusible ther-
miquement stable. Chimiquement, le précurseur est partiellement
déshydrogéné par oxydation et des doubles liaisons apparaissent.
Le PAN de formule chimique simplifiée (C3H3N)n se transforme en
(C3H1,4NO0,6)m. Plusieurs modèles de structures de types cyclo-
aromatiques ont été proposés [5]. Le modèle de Takahagi et coll. est
donné sur la figure 2. Pendant cette étape et l’étape suivante – la
carbonisation – les propriétés élastiques de la fibre se modifient en
continu. Il est donc essentiel de maintenir en permanence une ten-
sion appropriée si l’on veut conserver une orientation axiale à la fibre.
1.2.2.2 Carbonisation
Le précurseur stabilisé pendant l’étape précédente est carbonisé
sous azote, jusqu’à des températures de l’ordre de 1 200 à 1 500 oC
pendant un temps qui peut varier de 2 à 10 min. Dans cette étape,
environ 60 % de la masse du PAN oxydé sont éliminés sous forme
de gaz. Ces gaz sont essentiellement constitués par de la vapeur
d’eau, des dérivés carbonés CO2, CO, CH4 et azotés HCN, N2, NH3.
Tableau 1 – Propriétés mécaniques en traction
des fibres de carbone fabriquées entre 1960 et 1974
à partir de fibres de rayonne
Producteur Produit
commercialisé
Module
de traction
(GPa)
Résistance
en traction
(MPa)
Union Carbide Thornel 25 175 1 250
Thornel 40 280 1 750
Thornel 50 350 2 000
Thornel 100 700 3 500
Figure 1 – Principe du procédé de fabrication des fibres de carbone
ex-PAN