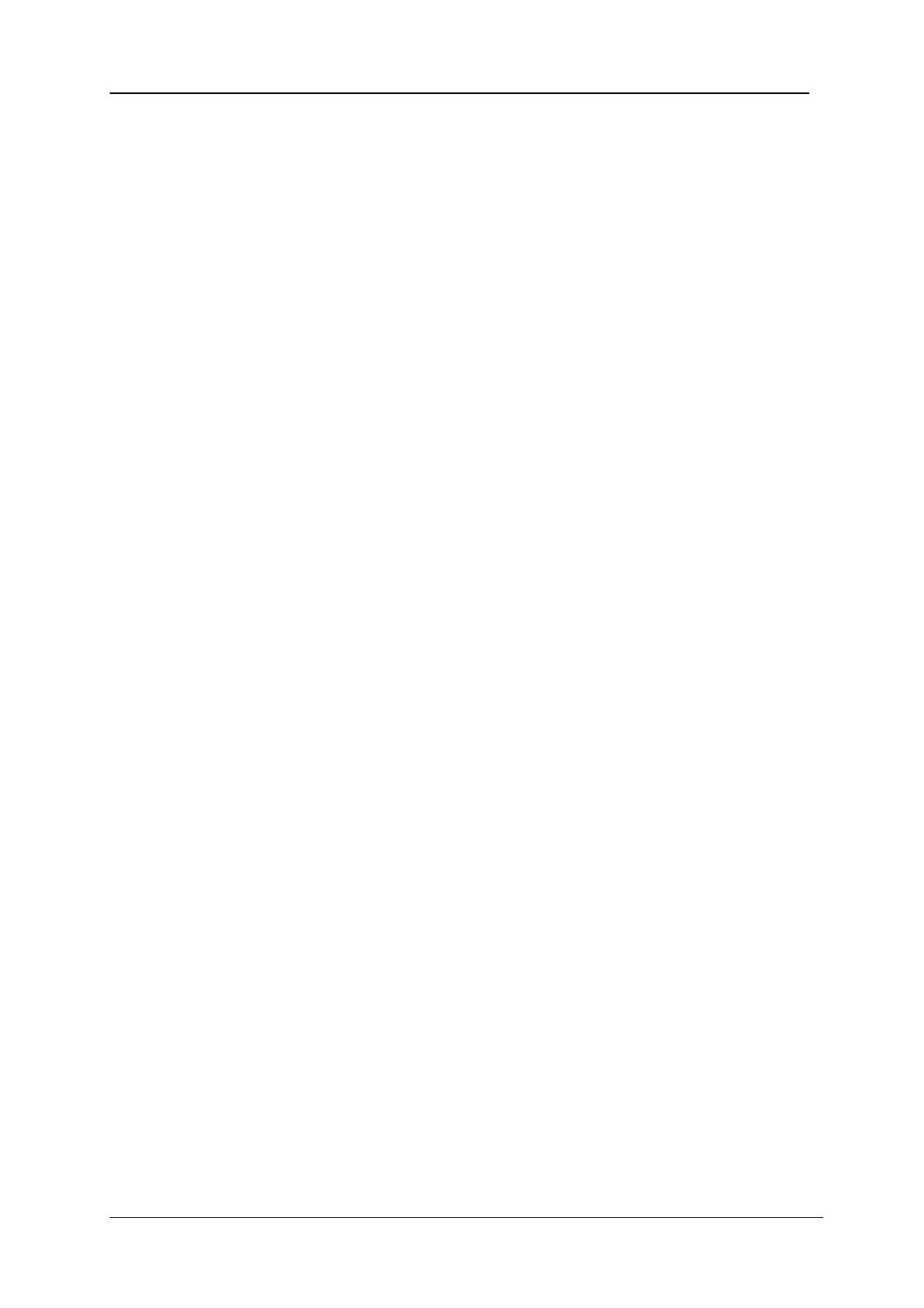
CIRCUITS HYDRAULIQUES.
CHAPITRE 01 : LES PRAMÈTRES DE L’HYDRAULIQUE
Introduction :
Les systèmes hydrauliques se retrouvent partout dans les installations industrielles qui
requièrent de la force, de la flexibilité et de la fiabilité. De nos jours, l’avènement de
l’électronique et de l’informatique a permis de perfectionner les circuits hydrauliques . Ceux
et celles qui oeuvrent dans ce domaine doivent donc se tenir à l’avant-garde de ce qu’il est
convenu d’appeler aujourd’hui l’électrohydraulique .
Pour ce faire, il leur faut bien connaître les principaux facteurs qui conditionnent les
systèmes hydrauliques et être en mesure d’utiliser les formules mathématiques qui les
déterminent .
1-Débit et vitesse :
De façon générale, le débit (qv) es définit comme étant un certain volume de matière
qui se déplace dans un certain volume de matière qui se déplace dans un temps déterminé .
Prenez, par exemple, le nombre d’automobiles qui circulent sur une autoroute durant 1 heure .
On exprime le débit ou volume de circulation pendant cette période par la formule de
circulation pendant cette période par la formule mathématique suivante :
Nombre d’auto / heure = Débit (qv)
Tout comme dans l’exemple de la circulation automobile, le débit (qv) de fluide
dépend directement de la vitesse (v) linéaire de ce fluide et de l’aire (A) de la section de la
conduite (figure 1) où :
- qv = Volume (masse volumique) par unité de temps .
- v = Déplacement linéaire des molécules en unités de longueur par unité de temps
(vitesse) .
- A = Aire en unités carrées de la section prises perpendiculairement au déplacement
du fluide .
Le débit qui circule dans la conduite est égal au produit de v par A, d’ou la formule
générale :
qv = v * A
Voyez maintenant une application concrète de cette formule .
Quel serait le débit d’un fluide (en L/min) qui circule dans une conduite de 50 mm de
diamètre à une vitesse de 100 mm/s ?
Exercice 1 :
1. Donnez la définition du débit .
2. Quels sont les deux principaux facteurs physiques qui influencent le débit dans une
conduite fermée ?
3. Calculez le débit qui circule dans la conduite représentée dans la figure 2 (qv est en
cm3/s) .
1-1-Influence du diamètre des sections :
Formateur : Sami REKIK. 3