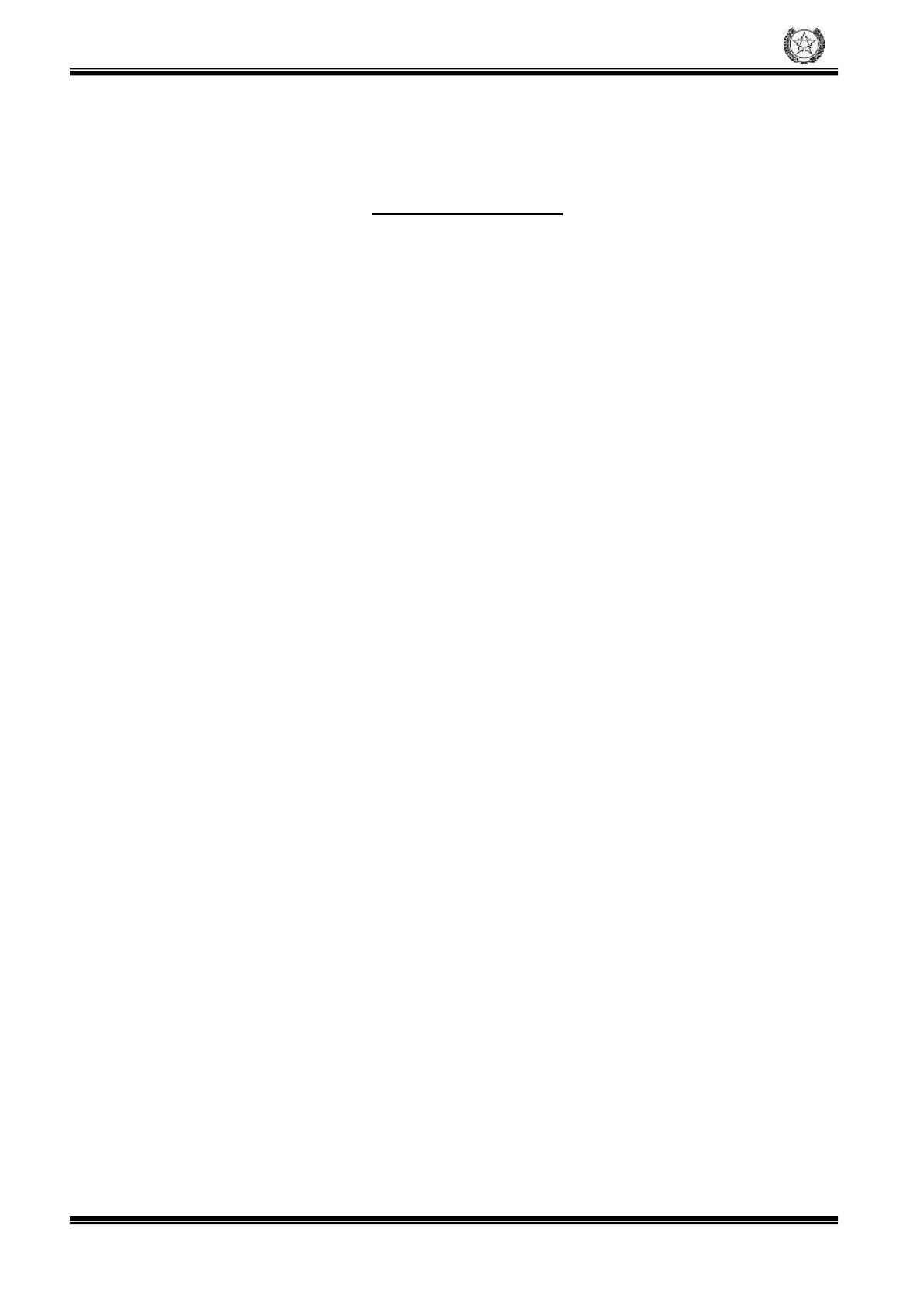
PMK/PC/IE
INTRODUCTION
La Direction Production Minière de Khouribga s’est fixée comme objectif, en 2008, la
réalisation d’un tonnage épierré sec et marchand de 20MT. La part du secteur Sidi
Chennane étant de 7,6 MT.
L’installation d’épierrage du secteur Sidi Chennane est conçue pour produire 6MT. Alors
qu’elle a réalisé en 2007 un tonnage de 6,8MT. Ceci est dû à de grandes améliorations
apportées à la conception de cette installation ; à savoir, l’implantation des systèmes de
décolmatage et l’extension des deux mises à terril par des convoyeurs horizontaux.
Donc afin d’atteindre l’objectif de production en 2008 qui est de 7,6MT, l’installation
d’épierrage de sidi Chennane, qui constitue un goulot d’étranglement, doit faire à nouveau
l’objet d’amélioration en terme de fiabilité et de disponibilité et ce en augmentant :
Le taux d’utilisation, moyennant :
- La saturation de la trémie par le biais de l’augmentation du front actif et de
l’adoption d’une gestion réfléchie des qualités sources qui tient compte du
besoin en qualités marchandes.
- L’acquisition de nouveaux camions.
- La sous-traitance relative au chargement et au transport des intercalaires
couche1-couche2 et couche2-couche3.
Le taux de disponibilité, moyennant :
- La fiabilisation de la partie mécanique
- La fiabilisation de la partie électrique