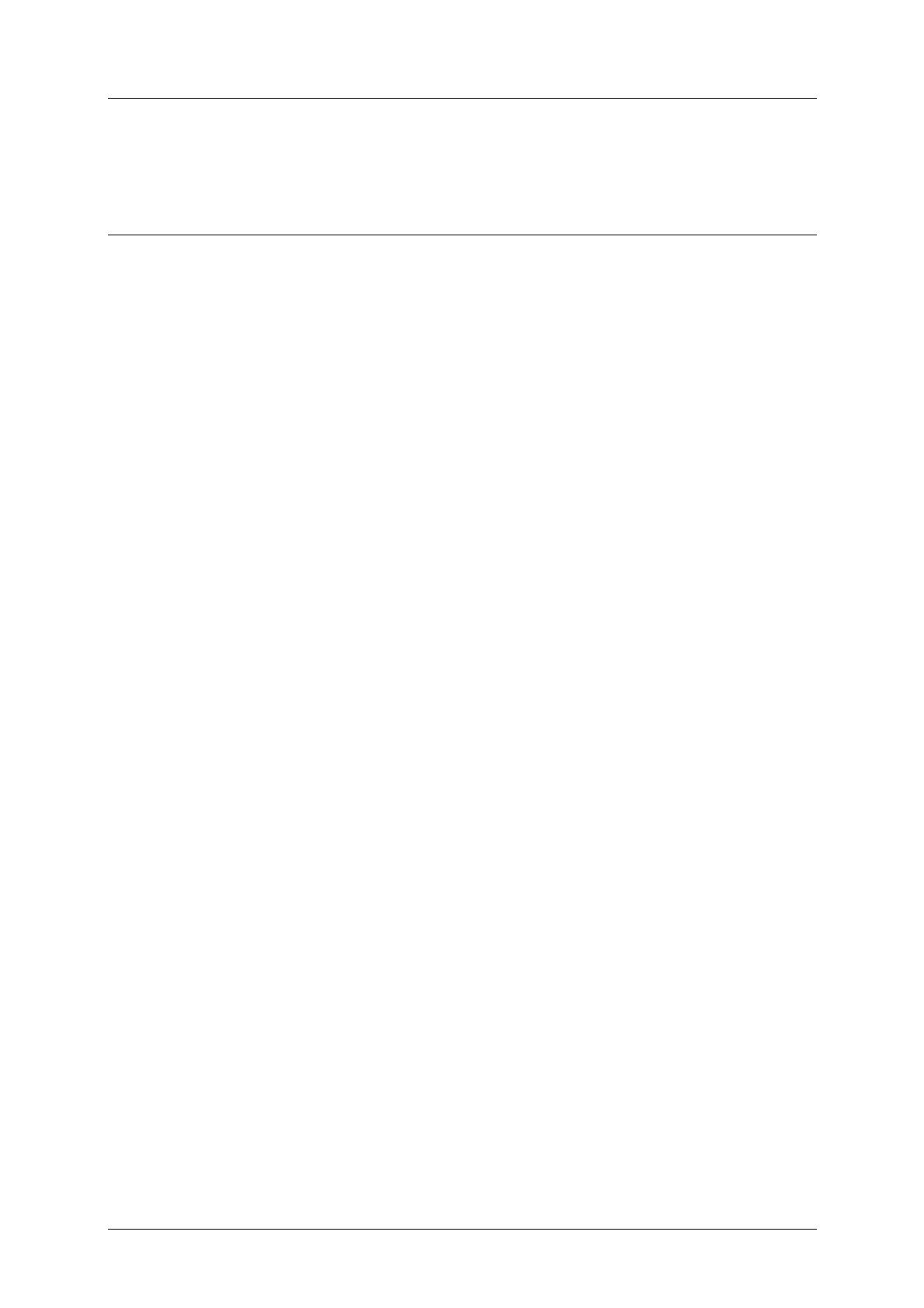
1
Sommaire
Introduction………………….……………………………………...……………..….….….3
Synthèse bibliographique……………………………………………………………….….6
I.1. L’aluminium et ses alliages………………………………………………………………..8
I.2. Les familles d’alliages d’aluminium………………………………………………………9
I.3. Durcissement
structural…………………………………………..……………………..…11
I.4. Ségrégation, précipitation intermétallique et inclusions dans les alliages
d’aluminium.....10
I.5. Système aluminium-cuivre et l’alliage 2024……………...……………………..……….13
I.6. Système aluminium-zinc-magnésium et l’alliage 7075…………………………………..15
I.7. Généralités sur la corrosion de l’aluminium……………………………………………...17
I.8. Influence des éléments d’alliage sur le film passif……………………………………….20
I.9. Rupture physique de la passivité…………………………………………………………21
I.10. Corrosion de l’alliage 2024 et de l’alliage 7075……………………………………...…23
I.10.1. Corrosion par piqûres...….………………………………………………………...23
I.10.2. Corrosion intergranulaire……………………………………………….………….23
I.10.3. Corrosion exfoliante ou feuilletante……………………………………………….24
I.10.4. Corrosion galvanique……….……………………………………………………...25
I.11. Etudes précédentes……………………………………………………………………...25
I.12. Conclusions………………………………………………….…………………………..29
Matériaux, méthodes et conditions expérimentales......................................................33
II.1. Matériaux : alliages d’aluminium 2024 T351 et 7075 T7351 et aluminium pur.…….…33
II.2. Méthodes de caractérisation microstructurale……………………………………..…….34
II.2.1. Microscopie optique……………………………………………………..…………34
II.2.2. Microscopie électronique à balayage…………………………..………..…………34
II.2.3. Microscopie électronique en transmission…..………………..……………………35
II.3. Techniques électrochimiques………………………….………………………………...36
II.3.1. Chronopotentiométrie……………..…………………………………..……………36
II.3.2. Chronoampérométrie……………..……………………………..………………….36
II.3.3. Voltampérométrie…………………………………………………………………..36
II.3.4. Tracés des courbes de Levich……………………………………..………..………36
II.3.5. Spectroscopie d’impédance électrochimique (SIE)……………….……………….37
II.3.5.1. Représentations traditionnelle des données……………..…………………….39
II.3.5.2. Circuits électriques équivalents…………..…………………………………...39
II.3.5.3. Modèle de loi de puissance…………………………………………………...42
II.3.6. Conditions expérimentales des essais électrochimiques……………………….…..44
II.3.6.1. Milieu d’étude………………………………………………………………...44
II.3.6.2. Préparation de la surface……………………………………………………...45
II.3.6.3. Montage électrochimique……………………………………………………..45