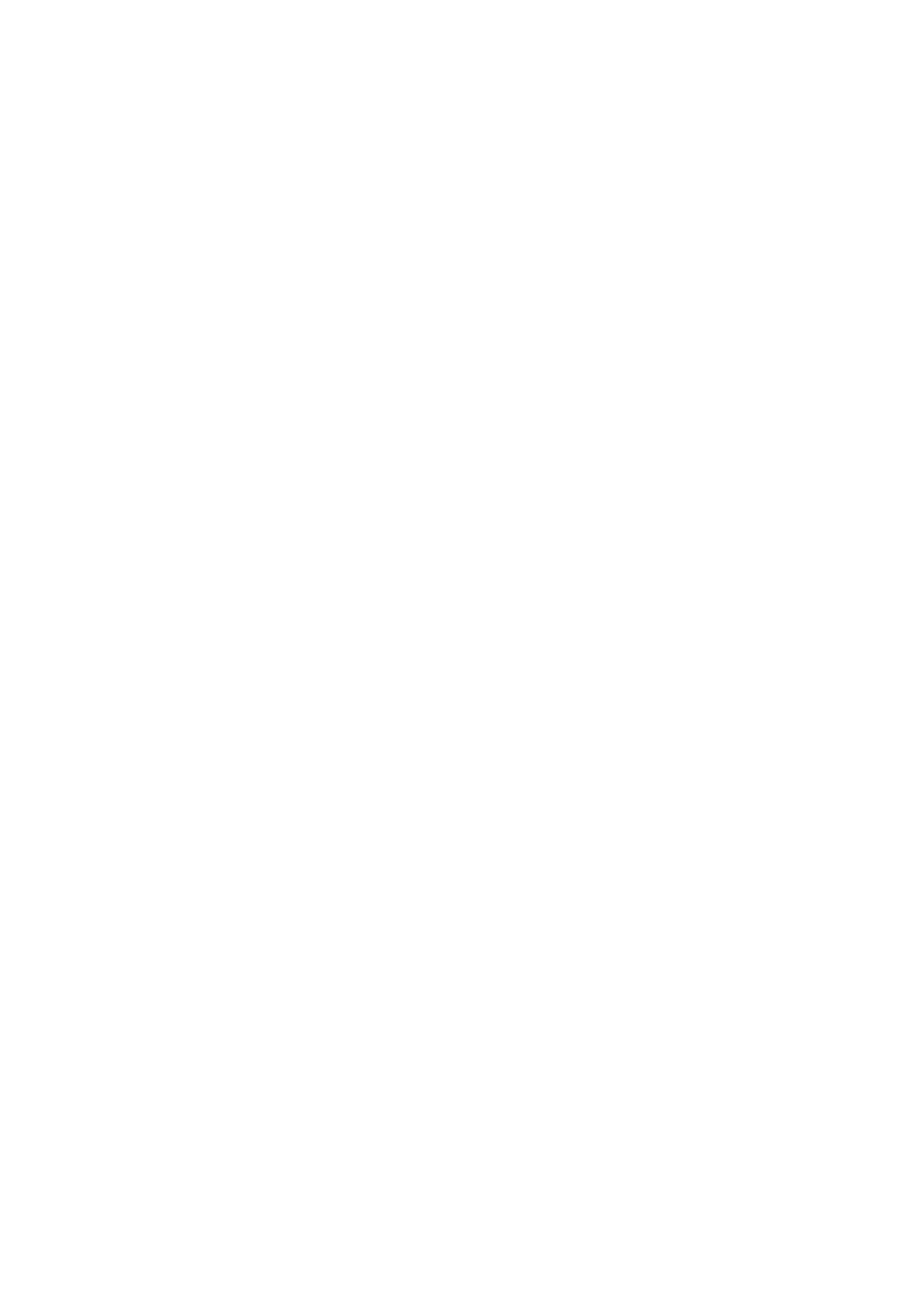
5
Sommaire
Nomenclature ………………………………………………………………………………..
Introduction générale…………………………………………………………………………
Chapitre I : Etat de l’art sur le broutement en usinage
I-1 Introduction………………………………………………………………………………
I-2 Vibrations en usinage ……………………………………………………………………
I-2-1 Les Vibrations libres amorties…..……………………………………………..
I-2-2 Les vibrations Forcées…………………………………………………………
I-2-3 Les vibrations auto-entretenues (broutement)…………………………………
I-3 Le Broutement……………………………………………………………………………
I-3-1 Broutement d'origine régénératif………………………………………………
I-3-2 Broutement d’origine non régénératif………………………………………….
I-3-2-1 Phénomène de couplage des modes de vibration……………………
I-3-2-2 Le Talonnage………………………………………………………..
I-3-2-3 Les interactions à l’interface outil-copeau…………………………..
I-4 Modèles analytiques de broutement……………………………………………………..
I-4-1 Modèle linéaire de broutement de Tobias ……………………………………
I-4-2 Modèle de Wu et Liu…………………………………………………………..
I-4-3 Modèle de Segreti ……………………………………………………………..
I-5 Etude de Broutement en fraisage………………………………………………………...
I-5-1 Connaissances sur la modélisation des efforts de coupe pour le fraisage ……
I-5-2 Différentes méthodes de modélisation des efforts de coupe pour le fraisage ..
I-5-2-1 Les méthodes empiriques …………………………………………...
I-5-2-2 Les méthodes analytiques……………………………………………
I-5-2-3 Les méthodes numériques…………………………………………...
I-5-3 Différents domaines de modélisation des forces de coupe pour le fraisage …
I-5-3-1 Le domaine statique………………………………………………….
I-5-3-2 Le domaine quasi-statique …………………………………………..
I-5-3-3 Le domaine dynamique……………………………………………..
I-5-4 Approches de modélisation du broutement en fraisage ……………………..
I-5-4-1 Simulation de Smith et Tlusty ………………………………………
I-5-4-2 Travaux de Altintas et Budak………………………………………
I-5-4-3 Modélisation de Huaizhong et Xiaoping……………………………
I- 6 l’instabilité de fraisage…………………………………………………………………
1-7 Conclusion ……………………………………………………………………………..
Chapitre II : Modélisation des efforts de coupe en fraisage
II-1 Introduction……………………………………………………………………………...
II-2 Mécanisme du fraisage…………………………………………………………………..
II-2-1 : Mouvement de coupe et avance……………………………………………..
11
13
14
14
15
15
16
18
18
19
20
21
21
22
25
27
27
28
28
29
30
31
31
31
33
33
33
34
38
39
42
44
44