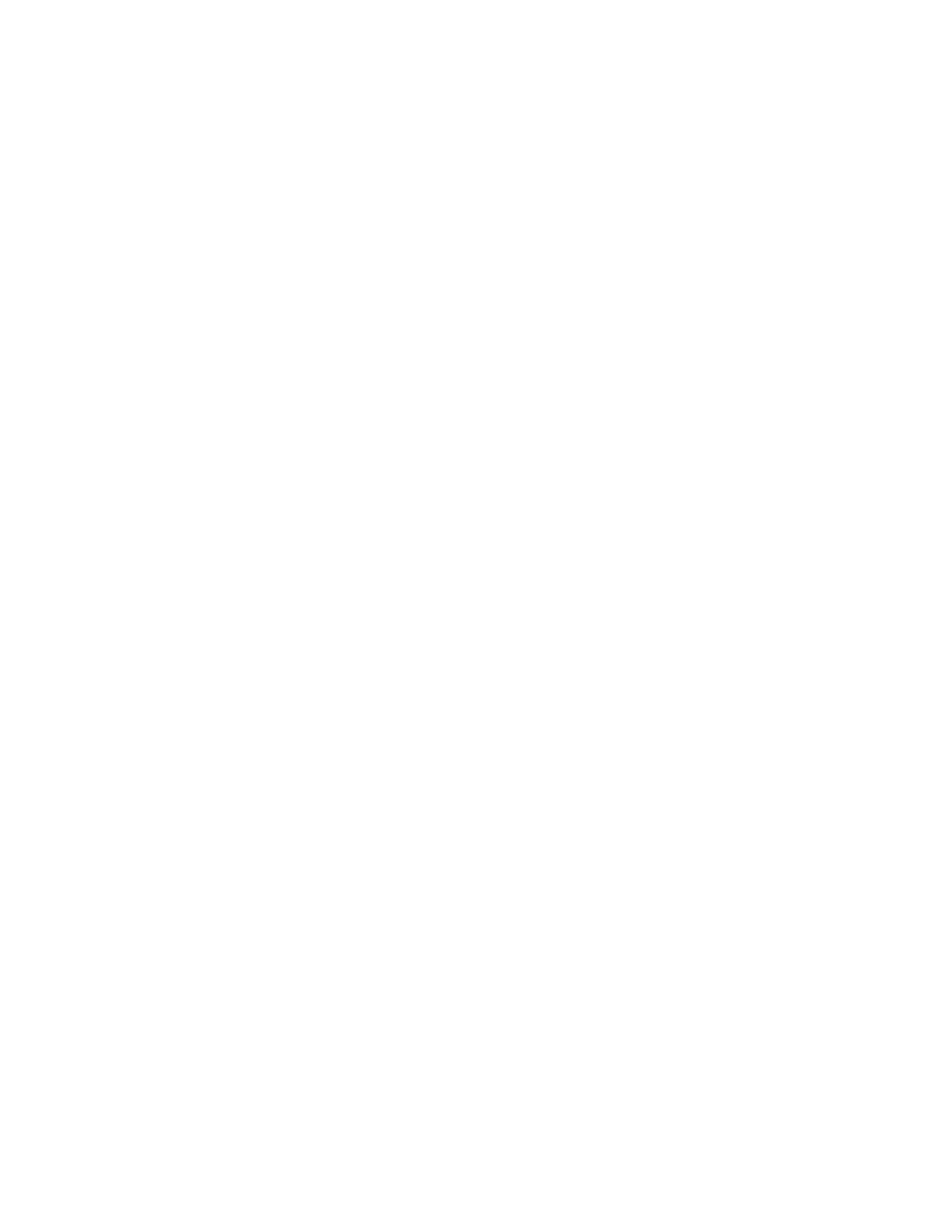
Résumé.
La pollution par les moteurs aéronautiques est un problème majeur que le concept de foyer
prémélangé, prévaporisé pauvre ( ou LPP pour lean premixed prevaporized ) peut permettre de
réduire. En effet, ces foyers tendent à optimiser la combustion en favorisant le mélange et ce
en créant un écoulement swirlé qui a la particularité à la fois d’augmenter le mélange entre les
espèces et d’autre part de stabiliser la flamme. De plus, le fait que le mélange soit fait avant
combustion favorise la réaction de tout le mélange. Enfin, la production d’oxyde d’azote est
réduite dans le cas d’un mélange pauvre. De nombreux avantages semblent donc pousser au
développement de ce type de foyer.
Néanmoins, la stabilisation de la flamme est le problème majeur de ce système. Il existe diffé-
rentes conditions de stabilisation de la flamme, et en particulier la condition de "flashback" qui
conduit à faire remonter la flamme dans le tube de prémélange, avec les risques d’explosion que
cela comporte. Par conséquent, tous les phénomènes relatifs à chacune des étapes mises en jeu
dans ce système doit être parfaitement comprise. Enfin, l’utilisation de l’outil numérique doit
permettre la confirmation des données expérimentales obtenues sur la manipulation.
Mots clés :
flamme de prémélange.
richesse.
instabilité thermo-acoustique.
Abstract.
Keywords :
premixed flame.
equivalence ratio.
thermo-acoustic instability.
2