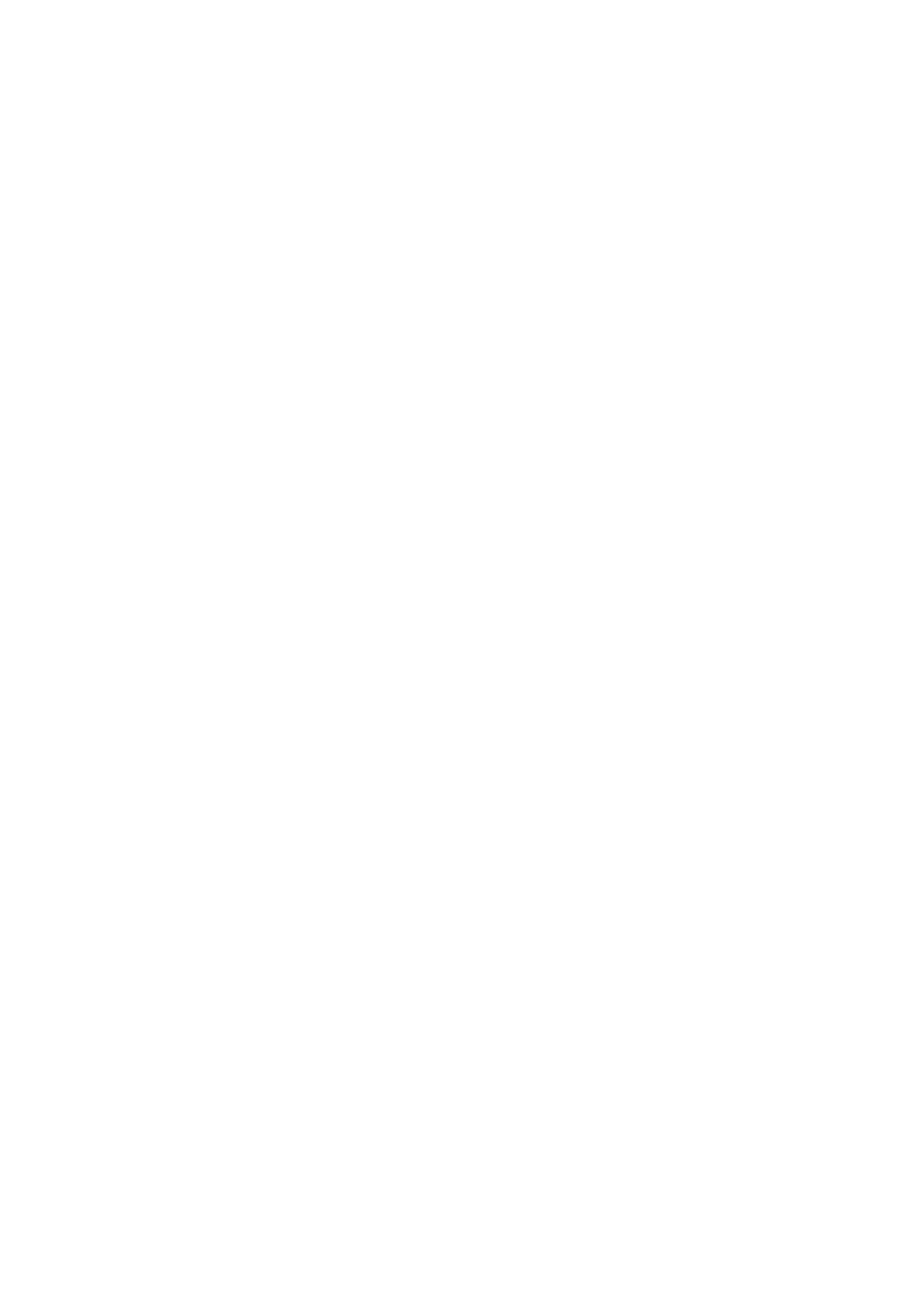
MOSIM’10 - 10 au 12 mai 2010 - Hammamet - Tunisie
C’est sur ce dernier point que nous désirons nous pen-
cher dans la partie suivante.
4 CHAINES LOGISTIQUES INVERSE ET EN
BOUCLE FERMEE
4.1 Chaînes inverses
La réutilisation de produits ou de matériaux n’est pas un
phénomène nouveau. Dans tous les cas, les opportunités
liées à la réutilisation sont à l’origine d’un nouveau flux
retour de matière de l’utilisateur final vers les produc-
teurs. La gestion de ce flux de matière dans le sens oppo-
sé au flux conventionnel de la chaîne logistique est
l’objet d’un nouveau domaine de travail appelé “logisti-
que inverse”. Le conseil exécutif américain sur la logis-
tique inverse définit cette logistique inverse, voir (Ro-
gers et Tibben-Lemke, 1998) comme: “Le processus de
planification, d’implémentation, et de contrôle du flux
rentable et efficace de matière première, d’inventaires de
process, de produits finis et d’informations du point de
consommation au point d’origine dans le but de recaptu-
rer de la valeur ou dans le but d’un traitement convena-
ble des déchets”. Différente de la traditionnelle logisti-
que directe, la logistique inverse réfère aux activités dé-
diées au traitement des produits retournés jusqu’à ce
qu’ils soient récupérés de manière satisfaisante ou mis au
rebut de la chaîne logistique. Ces activités comprennent
la collection, le nettoyage, le désassemblage, les tests et
le tri, le stockage, le transport et les options de récupéra-
tion, comme la réutilisation, la réparation, la remise à
neuf, la refabrication, la cannibalisation et le recyclage.
Trois grands arguments expliquent le besoin croissant en
activities inverses: l’intérêt économique, comme la pos-
sibilité de recapturer de la valeur sur des produits utili-
sés, les directives gouvernementales comme la directive
européenne WEEE référencée 2002/96/EC sur les dé-
chets issus des équipements électriques et électroniques,
et les pressions des consommateurs pour le retour des
produits utilisés ou défectueux, voir (Srivastava, 2008).
En effet, plusieurs pays ont renforcé la législation sur le
respect de l’environnement, en rendant les producteurs et
fabricants responsables de leur produit tout au long de
son cycle de vie. Les obligations de reprises sont à
l’exemple des mesures prises. Mais même si la législa-
tion est moins rigide, la motivation des consommateurs
impose une pression sur les entreprises pour la prise en
compte des questions environnementales. Une image
“verte” est devenue un argument commercial important.
Cette évolution est à l’origine pour beaucoup
d’entreprises de la recherche de possibilités de reprise
pour traitement de leurs produits. D’un autre côté, il
existe également des activités économiques dont le but
est essentiellement la recapture de valeur encore incorpo-
rée dans un produit usagé (par exemple la refabrication à
l’aide de pièces détachées). Les aspects écologiques et
économiques sont souvent liés. Par exemple, augmenter
les coûts de récupération des déchets engendre une ré-
duction effective de ces déchets, et les consommateurs
soucieux de l’environnement représentent une nouvelle
opportunité de marché.
Les activités de logistique inverse sont effectuées dans
des usines spécifiques qui peuvent être de deux types,
voir (Melo et Saldanha-da-Gama, 2009): les centres de
collection (c'est-à-dire les endroits où les consommateurs
viennent déposer les produits usés) et les sites de retra-
vail (les centres de refabrication et centres de réparation
et de remise à neuf), voir (Rappold et Van Roo, 2009).
C’est dans ce contexte que la structure même du réseau
doit être étendue avec des liens pour le transport des flux
retours allants des consommateurs jusqu’aux sites où ont
lieu les réparations, les refabrications, et/ou les activités
de recyclage (par exemple les entrepôts, les usines de
refabrication).
Lorsque l’on modélise une chaîne logistique inverse,
seul le flux inverse doit être considéré. Un ensemble de
localisations possibles pour les différents types d’usines
est donné et un choix doit être effectué. Les articles col-
lectés peuvent être véhiculés via des itinéraires diffé-
rents. L’optimisation intervient au niveau des coûts de la
chaîne logistique, généralement fixes et des coûts varia-
bles pour les usines et les transports intermédiaires. La
programmation linéaire en nombres mixtes est la techni-
que la plus répandue et la plus utilisée. Parfois, les loca-
lisations sont imposées ce qui conduit à un problème de
programmation linéaire. D’un point de vue mathémati-
ques, les modèles sont standards, voir (Krikke et al.,
2003) et les références qui y sont faites.
Une caractéristique particulière à prendre en compte
dans la conception de chaînes inverses est le grand degré
d’incertitude accompagnant le retour des produits usagés
par les consommateurs non seulement en termes de
quantité mais aussi en termes de qualité. Les produits de
grande qualité peuvent avoir un coût de transport plus
élevé (et donc être à l’origine d’un réseau centralisé),
alors que le transport étendu de produits de petite valeur
n’est pas économique. Par ailleurs, les produits peuvent
également être retournés pendant leur cycle de vie (re-
tours commerciaux, garanties, réparations), à la fin de
leur utilisation, ou en fin de vie ce qui nécessite de
considérer les caractéristiques des produits retournés afin
d’optimiser le processus de récupération de la valeur.
Enfin, les marchés de fin de vie des produits retournés ne
sont pas toujours bien connus.
Une autre particularité des chaînes inverses est la dépen-
dance aux acteurs intervenants dans la chaîne. En effet,
une spécificité de la logistique inverse est que certaines
compétences et expériences sont indispensables ce qui
impose des contraintes sur les acteurs possibles pour les
activités de réutilisation qui peuvent être aussi bien le
fabricant ou alors un prestataire de service, voir (Min et
Ko, 2008). Ceci ajoute des contraintes quant à la possibi-
lité d’intégrer les activités logistiques directes et inver-
ses, ce qui représente un véritable challenge pour la
conception de systèmes de distribution, voir (Fleis-
chmann et al., 1997).