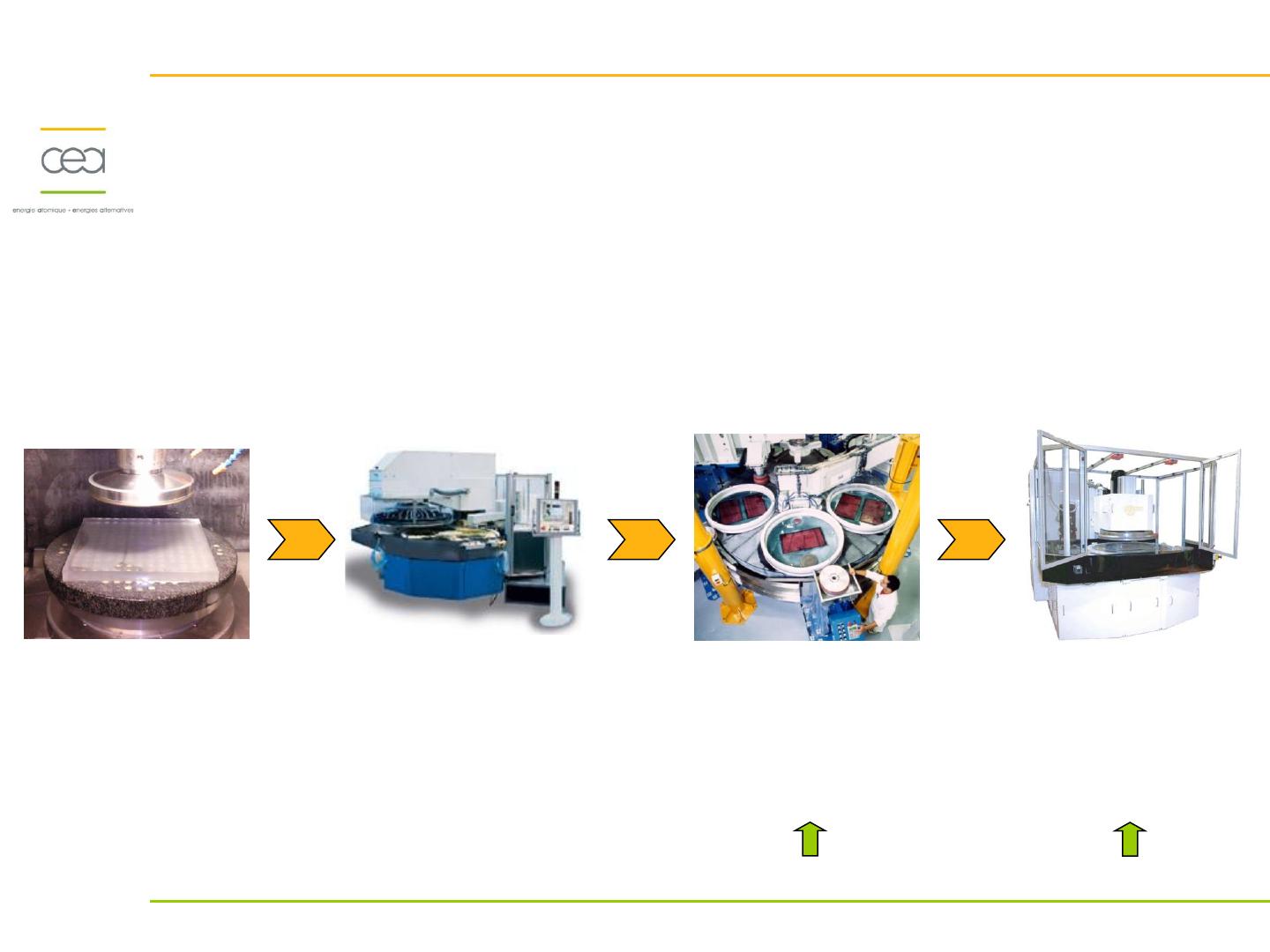
4
Fabrication des grands composants optiques (1/3)
•Objectif double lors de la fabrication des composants optiques :
>bonne qualité optique pour ne pas dégrader le front d'onde transmis
>bonne résistance au flux laser
•Quatre étapes pour obtenir des surfaces de haute qualité optique :
>conformité de la forme (planéité, forme locale)
>faible rugosité (diffusion de l'énergie et surintensités laser)
doucissage polissage
forme générale planéité, rugosité
abrasifs
> 100 µm liés
à une meule (diamant)
planéité, rugosité
abrasifs
10-50 µm en
suspension dans de l'eau
(diamant, Al2O3, SiC, B4C, …)
abrasifs
~ 1 µm en
suspension dans de l'eau
(CeO2, ZrO2, …)
ébauchage
CEA-Cesta Etude et compréhension des procédés de surfaçage 16-17/06/2011
finition
rugosité
abrasifs
1 nm-1 µm
pré-suspendus
(REO2, SiO2, …)
+ éventuellement retouche locale