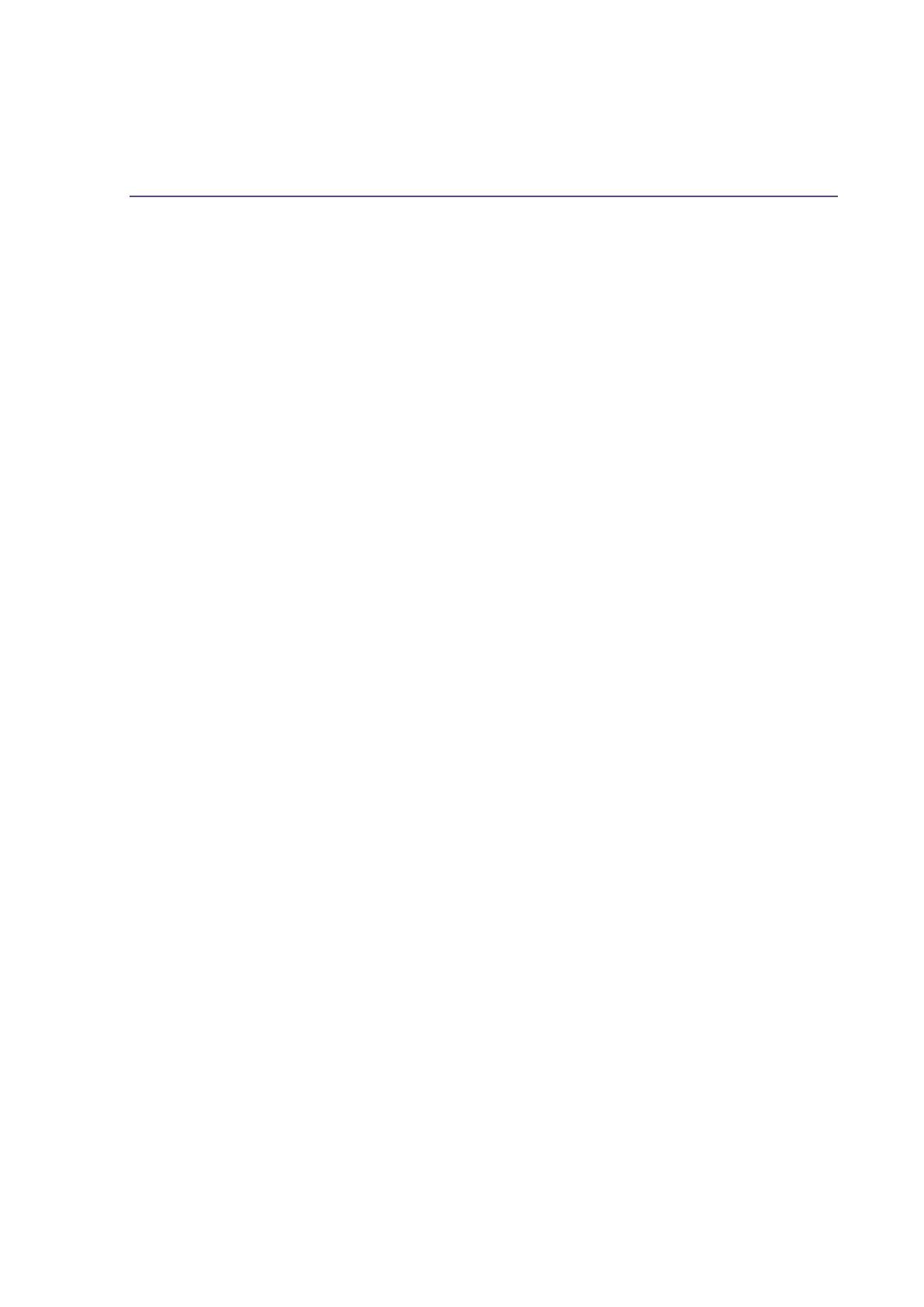
i
Sommaire
Liste des tableaux .......................................................................................................................................... iii
Liste des figures .............................................................................................................................................. v
Liste des annexes ........................................................................................................................................... ix
Introduction .................................................................................................................................................... 1
Chapitre 1 : Généralités ................................................................................................................................. 3
1. Les convertisseurs statiques ............................................................................................................... 3
1.1. Conversion continu-continu ....................................................................................................... 4
1.2. Conversion alternatif-continu ..................................................................................................... 4
1.3. Conversion continu-alternatif ..................................................................................................... 4
1.4. Conversion alternatif-alternatif ................................................................................................... 5
2. Les interrupteurs dans une cellule de commutation ......................................................................... 5
2.1. Interrupteur idéal ....................................................................................................................... 5
2.2. Les semi-conducteurs................................................................................................................. 6
3. Structure d’un module IGBT ............................................................................................................ 7
4. Fonctionnement d’un onduleur ......................................................................................................... 8
5. Stratégie de commande des onduleurs............................................................................................. 11
5.1. La modulation à rapport cyclique constant.................................................................................11
5.2. La Modulation à Largeur d’Impulsion .......................................................................................11
6. Pertes dans les interrupteurs ........................................................................................................... 12
6.1. Méthode analytique de calcul des pertes ....................................................................................15
6.2. Méthode numérique pour la simulation des pertes......................................................................17
7. Modélisation thermique des composants de puissance.................................................................... 19
7.1. Modèles thermiques analytiques : ..............................................................................................19
7.2. Modèles thermiques numériques 3D ..........................................................................................19
7.3. Modèles thermiques approximés : .............................................................................................20
7.4. Modèles compacts ....................................................................................................................21
8. Simulation électrothermique ........................................................................................................... 23
8.1. Méthode de relaxation...............................................................................................................23
8.2. Méthode directe ........................................................................................................................23
9. Conclusion ........................................................................................................................................ 24
Chapitre 2 : Étude Expérimentale ................................................................................................................25
1. Structure du module IGBT étudié ................................................................................................... 25
2. Description du banc expérimental ................................................................................................... 28
2.1. Onduleur monophasé ................................................................................................................30
2.2. Système de refroidissement .......................................................................................................31
2.3. Système de mesure électrique....................................................................................................31
2.4. Systèmes de mesure thermique ..................................................................................................32
3. Résultats expérimentaux .................................................................................................................. 35
3.1. Mesures électriques ..................................................................................................................35
3.2. Mesures thermiques ..................................................................................................................39
4. Conclusion ........................................................................................................................................ 46