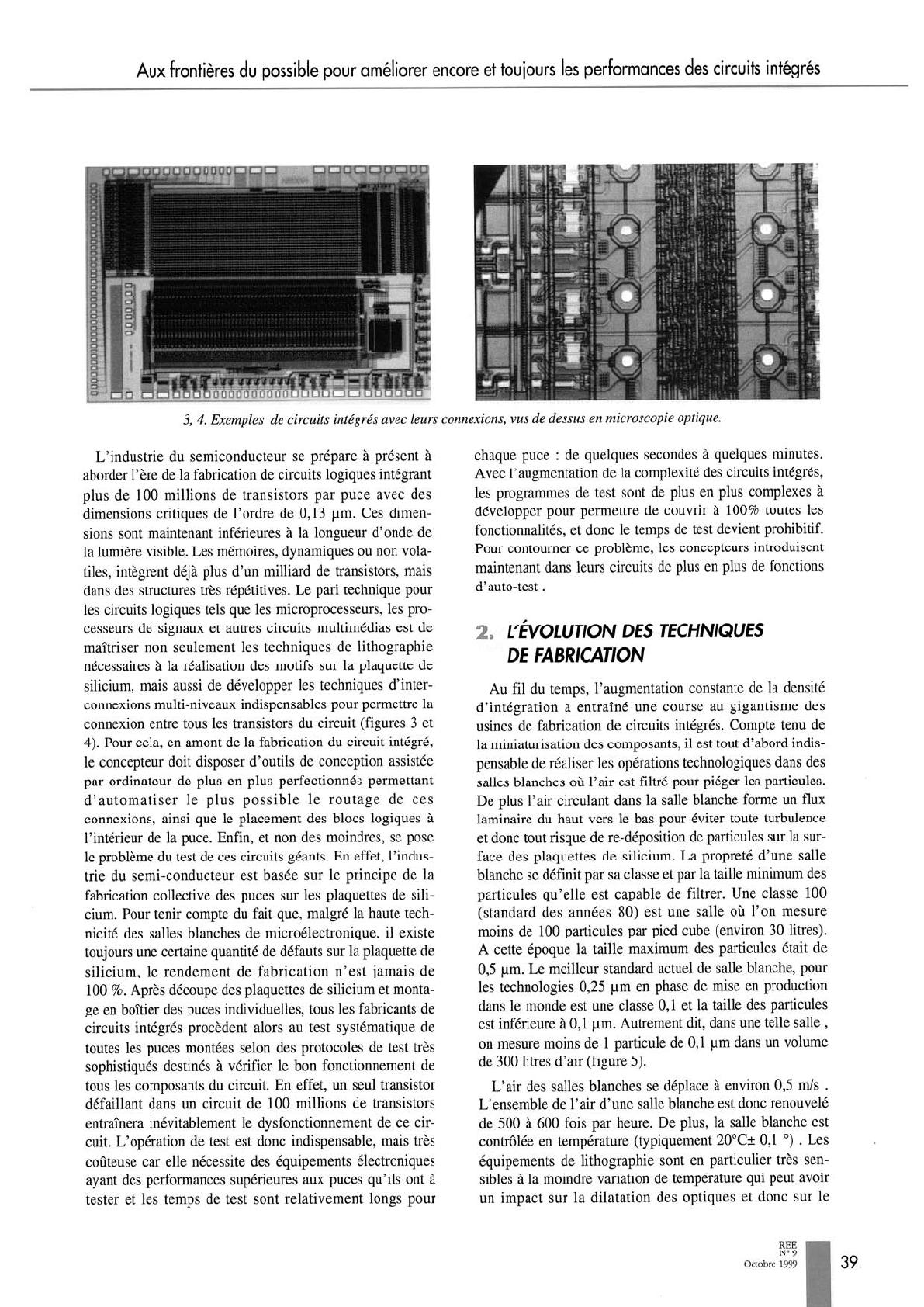
Aux frontières du possible pour améliorer encore et toujours les performances des circuits intégrés
Hi
f II Ey e
k
i :
1&
L_ i' tri J' i, C n h'Î I r a 0 l'C : L , Y___J __., r :''
...,.,
_
.
i F :' _
. r.' xs -
J "
,7, ". " v ffle,
c (, n i n r n -, 17 ! 3 i -, rn l7 rr.
3, 4. Exemples de circuits intégrés avec leurs connexions, vus de dessus en microscopie optique.
L'industrie du semiconducteur se prépare à présent à
aborder l'ère de la fabrication de circuits logiques intégrant
plus de 100 millions de transistors par puce avec des
dimensions critiques de l'ordre de 0,13 um. Ces dimen-
sions sont maintenant inférieures à la longueur d'onde de
la lumière visible. Les mémoires, dynamiques ou non vola-
tiles, intègrent déjà plus d'un milliard de transistors, mais
dans des structures très répétitives. Le pari technique pour
les circuits logiques tels que les microprocesseurs, les pro-
cesseurs de signaux et autres circuits multimédias est de
maîtriser non seulement les techniques de lithographie
nécessaires à la réalisation des motifs sur la plaquette de
silicium, mais aussi de développer les techniques d'inter-
connexions multi-niveaux indispensables pour permettre la
connexion entre tous les transistors du circuit (figures 3 et
4). Pour cela, en amont de la fabrication du circuit intégré,
le concepteur doit disposer d'outils de conception assistée
par ordinateur de plus en plus perfectionnés permettant
d'automatiser le plus possible le routage de ces
connexions, ainsi que le placement des blocs logiques à
l'intérieur de la puce. Enfin, et non des moindres, se pose
le problème du test de ces circuits géants. En effet, l'indus-
trie du semi-conducteur est basée sur le principe de la
fabrication collective des puces sur les plaquettes de sili-
cium. Pour tenir compte du fait que, malgré la haute tech-
nicité des salles blanches de microélectronique, il existe
toujours une certaine quantité de défauts sur la plaquette de
silicium, le rendement de fabrication n'est jamais de
100 %. Après découpe des plaquettes de silicium et monta-
ge en boîtier des puces individuelles, tous les fabricants de
circuits intégrés procèdent alors au test systématique de
toutes les puces montées selon des protocoles de test très
sophistiqués destinés à vérifier le bon fonctionnement de
tous les composants du circuit. En effet, un seul transistor
défaillant dans un circuit de 100 millions de transistors
entraînera inévitablement le dysfonctionnement de ce cir-
cuit. L'opération de test est donc indispensable, mais très
coûteuse car elle nécessite des équipements électroniques
ayant des performances supérieures aux puces qu'ils ont à
tester et les temps de test sont relativement longs pour
chaque puce : de quelques secondes à quelques minutes.
Avec l'augmentation de la complexité des circuits intégrés,
les programmes de test sont de plus en plus complexes à
développer pour permettre de couvrir à 100% toutes les
fonctionnalités, et donc le temps de test devient prohibitif.
Pour contourner ce problème, les concepteurs introduisent
maintenant dans leurs circuits de plus en plus de fonctions
d'auto-test.
L'ÉVOLUTION DES TECHNIQUES
DE FABRICATION
Au fil du temps, l'augmentation constante de la densité
d'intégration a entraîné une course au gigantisme des
usines de fabrication de circuits intégrés. Compte tenu de
la miniaturisation des composants, il est tout d'abord indis-
pensable de réaliser les opérations technologiques dans des
salles blanches où l'air est filtré pour piéger les particules.
De plus l'air circulant dans la salle blanche forme un flux
laminaire du haut vers le bas pour éviter toute turbulence
et donc tout risque de re-déposition de particules sur la sur-
face des plaquettes de silicium. La propreté d'une salle
blanche se définit par sa classe et par la taille minimum des
particules qu'elle est capable de filtrer. Une classe 100
(standard des années 80) est une salle où l'on mesure
moins de 100 particules par pied cube (environ 30 litres).
A cette époque la taille maximum des particules était de
0,5 Mm. Le meilleur standard actuel de salle blanche, pour
les technologies 0,25 flm en phase de mise en production
dans le monde est une classe 0,1 et la taille des particules
est inférieure à 0, 1 p m. Autrement dit, dans une telle salle,
on mesure moins de 1 particule de 0,1 pm dans un volume
de 300 litres d'air (figure 5).
L'air des salles blanches se déplace à environ 0,5 m/s.
L'ensemble de l'air d'une salle blanche est donc renouvelé
de 500 à 600 fois par heure. De plus, la salle blanche est
contrôlée en température (typiquement 20'C± 0,1'). Les
équipements de lithographie sont en particulier très sen-
sibles à la moindre variation de température qui peut avoir
un impact sur la dilatation des optiques et donc sur le
REE
N'9
Octobre 1999