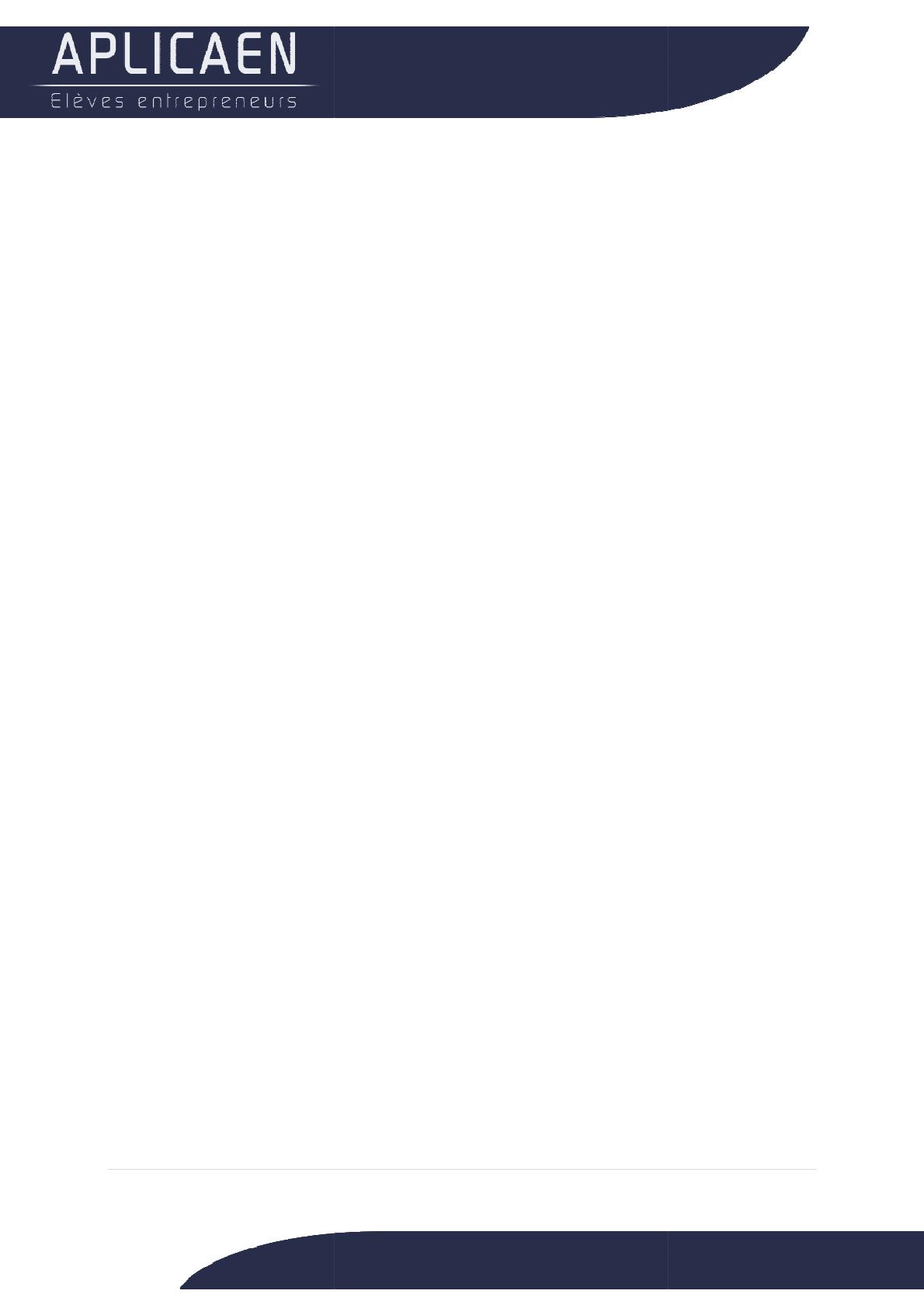
4 | 44 P a g e s
Réf : 002-Livrable-NAE
IV. LE CHROMAGE DUR
................................
1)
Alternative au chromage dur
a.
Traitement de surface par projection
1-
2-
3-
Projection par combustion
4-
5-
b. Solutions
électrolytiques de substitution
1-
2- DLC
................................
3- CVD
................................
c.
Traitement par voie humide
1-
2-
3-
L’oxydation des microarcs
4-
d.
Traitement par voie thermochimique
1- THERMI-SP
................................
2- Cémentation
................................
3-
4- Nitruration
................................
5- K-TECH
................................
6- Corr-I-Dur ©
................................
................................
................................
................................
Alternative au chromage dur
................................
................................
Traitement de surface par projection
................................
................................
................................................................
................................
................................................................
................................
Projection par combustion
................................
................................
................................................................
................................
................................
................................
électrolytiques de substitution
................................
................................
................................
................................
................................
................................
................................
................................
................................
Traitement par voie humide
................................
................................
................................
................................
................................................................
................................
L’oxydation des microarcs
................................
................................
................................................................
................................
Traitement par voie thermochimique
................................
................................
................................
................................
................................
................................
................................
................................
................................................................
................................
................................
................................
................................
................................
................................
................................
................................
................................
................................
APLICAEN
................................
............... 28
................................
........................... 28
................................
......... 28
................................
........... 28
................................
......... 29
................................
........................... 29
................................
.......... 29
................................
.................................... 30
................................
................................... 30
................................
............................. 30
................................
................................ 31
................................
............................... 31
................................
...................... 31
................................
.................................. 31
................................
........... 32
................................
............................. 32
................................
....... 32
................................
........ 33
................................
.................... 33
................................
................. 34
................................
........... 34
................................
.................... 34
................................
.......................... 35
................................
................. 35