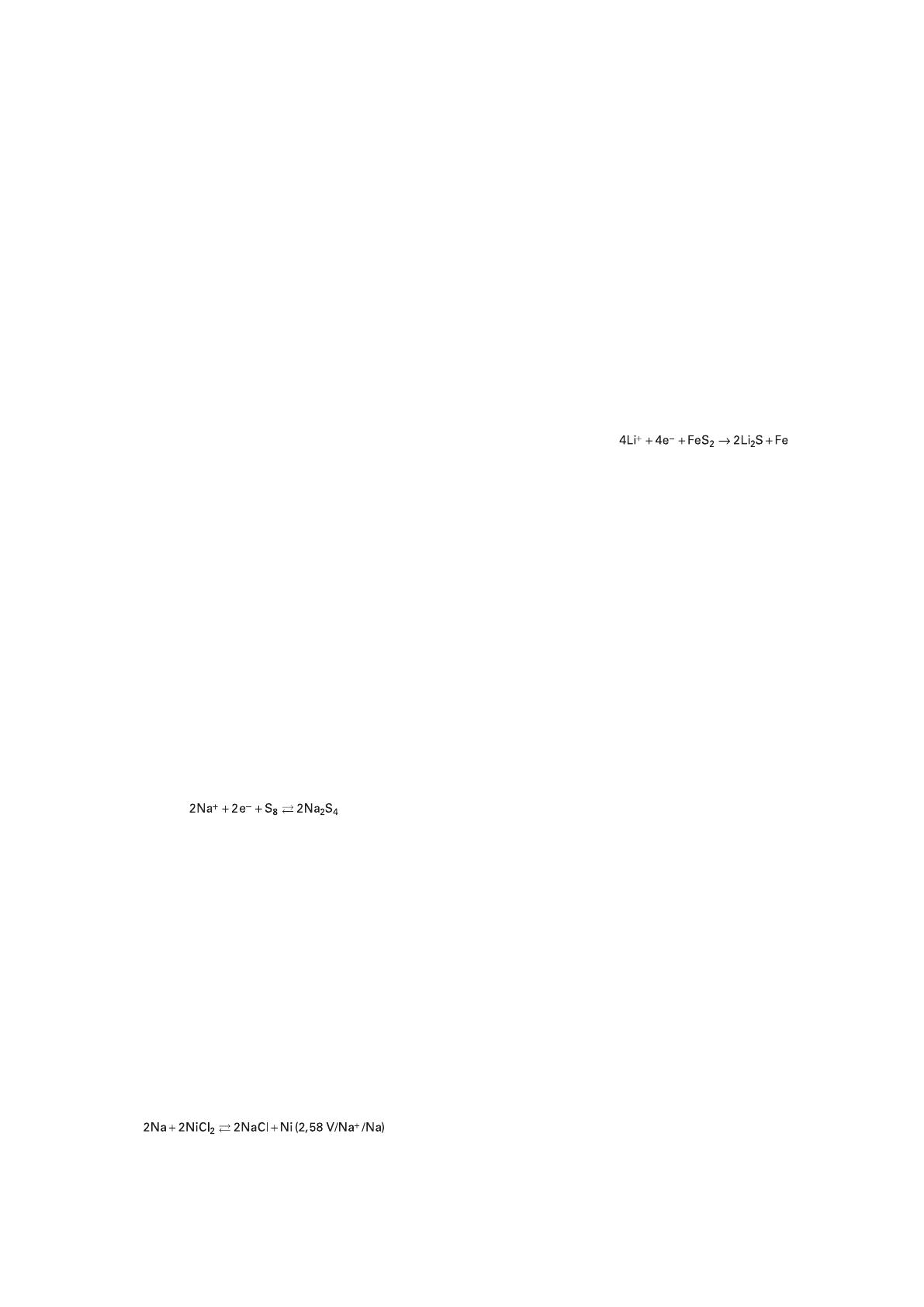
DE VOLTA AUX ACCUMULATEURS LI-ION ________________________________________________________________________________________________
Copyright © – Techniques de l’Ingénieur – Tous droits réservés
BE 8 620 – 4
3. 1970-1991 : boom
des systèmes
rechargeables
Le regain d’intérêt pour le véhicule électrique après le choc
pétrolier de 1973, le développement exponentiel de l’électronique
grand public à partir de la fin des années 1970 et le plafonnement
des performances des accumulateurs Ni-Cd conduisent à une accé-
lération des recherches dans le domaine des accumulateurs. Dans
cette quête de sources d’énergie embarquées pour des applica-
tions grand public, les critères de performance tels que la densité
d’énergie, la cyclabilité, le coût sont d’abord privilégiés, avant que
la sûreté de ces systèmes ne devienne la préoccupation majeure.
Différentes avancées conduisent au développement de filières
d’accumulateurs distinctes : la découverte d’électrolytes solides
céramiques ouvre la voie aux accumulateurs fonctionnant à haute
température, celle d’alliages hydrurables à température ambiante
permet la conception des accumulateurs aqueux « alcalins »
Ni-MH, la connaissance des matériaux d’intercalation permet la
conversion des piles au lithium en système rechargeables, et au
bout du compte celle des premiers accumulateurs Li-ion.
3.1 Accumulateurs au sodium « haute
température »
Les premiers accumulateurs à électrode négative en métal alcalin
à voir réellement le jour sont des systèmes fonctionnant à haute
température (> 300 °C). Le plus emblématique d’entre eux est le sys-
tème sodium soufre (Na-S) inventé et perfectionné par Ford
Motors Co. et General Electric dès le milieu des années 1960 [15]. Sa
conception tire parti de la découverte des propriétés de conduction
ionique de matériaux céramiques, et notamment de l’alumine bêta
(β’’-Al2O3) qui est un oxyde mixte d’aluminium et de sodium de
composition 11Al2O3-xNa2O (x~1-2) dopé au Mg, dont la structure
cristalline présente des chemins de conduction des ions sodium. Sa
conductivité est faible à température ambiante (~ 10–2 S · cm–1),
mais atteint une valeur nettement plus élevée à 300 °C (~ 0,2 à
0,4 S · cm–1), compatible avec une utilisation pratique [16]. Ces accu-
mulateurs fonctionnent généralement à une température stabilisée
autour de 350 °C, à laquelle le sodium et le soufre sont sous forme
liquide. L’électrode positive est constituée d’un feutre de carbone
imprégné de soufre liquide. La réaction réversible :
se déroule à environ 2 V/Na+/Na et fait intervenir différents polysul-
fures de sodium Na2Sx comme intermédiaires réactionnels. De
nombreux incidents émaillent le développement de cette technolo-
gie et mettent en évidence la fragilité de l’électrolyte céramique
vis-à-vis des sollicitations thermomécaniques pouvant conduire à
une mise en contact direct du soufre et du sodium fondus. L’appli-
cation visée à l’origine, le véhicule électrique, est abandonnée au
profit du stockage stationnaire de grande dimension. De telles ins-
tallations dédiées à l’écrêtage des pics de production électrique ou
couplées à des sources d’énergie renouvelables (éolien, photovol-
taïque) fonctionnent actuellement au Japon (par exemple, l’instal-
lation de NGK insulators 245 MWh, 34 MW à Rokkasho).
Une variante du système Na-S appelée accumulateur ZEBRA
(Zeolite Battery Research Africa ) est développée à partir de 1985
en Afrique du Sud par le CSIR (Council for Scientific and Industrial
Research). Dans ce système, le soufre est remplacé par du chlorure
de nickel additionné d’un sel de sodium NaAlCl4 permettant
d’assurer la conduction ionique dans le compartiment positif. À la
température de fonctionnement nominale (270 à 350 °C), la
réaction :
est réversible. Cette technologie permet d’atteindre des perfor-
mances convenables (150 W · kg–1, 81 Wh · kg–1 pour une batterie
de complète de 30 kWh). Elle est introduite dans des véhicules
électriques en 1998 (Mercedes Classe A), mais doit être abandon-
née pour des questions de sûreté. Ces accumulateurs sont produits
actuellement par Fiamm SoNick en Italie pour des applications
essentiellement liées au stockage stationnaire (onduleurs,
couplage énergies renouvelables). De nouveaux travaux entrepris
en 2010 par General Electric pour améliorer cette technologie ont
été interrompus en 2015.
Des systèmes rechargeables au lithium fonctionnant à haute
température sont développés à partir du début des années 1970 au
sein des laboratoires américains d’Argonne [17] et de Sandia, rapi-
dement suivis par Toyota [18] après 1973. Après des essais infruc-
tueux de transposition du système Na-S au lithium, une
technologie utilisant un électrolyte en sels fondus (eutectique
LiCl-KCl) et le couple de matériaux d’électrode Li(Al)/FeS2 , solides
à la température de fonctionnement (450 à 500 °C), a été dévelop-
pée. Il s’avère en effet que la réaction de conversion :
est parfaitement réversible à haute température. C’est également
le cas pour d’autres sulfures métalliques ; cependant, des considé-
rations de coût amènent à privilégier le disulfure de fer. Le déve-
loppement de ces accumulateurs se prolonge jusqu’au début des
années 1990 [19] pour aboutir à des performances intéressantes
(180 Wh · kg–1, 400 W · kg–1), sans pour autant que cela débouche
sur une utilisation commerciale dans le domaine du véhicule élec-
trique.
3.2 Accumulateurs au lithium(-ion)
3.2.1 Systèmes rechargeables à électrode
de lithium métallique
L’application des concepts d’électrodes à insertion [20] [21] aux
dispositifs de stockage électrochimique de l’énergie, discutée au
cours de la conférence « NATO Advanced Study Institute on Fast
Ion Transport in Solids, Solid State Batteries and Devices » à Belgi-
rate (Italie) en septembre 1972, jette les bases du développement
des accumulateurs au lithium, puis par la suite Li-ion, fonctionnant
à température ambiante. Les électrodes à insertion sont en effet
constituées de matériaux, conducteurs mixtes ioniques et électro-
niques qui, de par leur structure cristallographique et leur compo-
sition, sont susceptibles de permettre l’insertion/désinsertion
d’ions au sein de leur structure et de compenser ce transfert de
charge ionique par un transfert électronique. Les dichalcogénures
de métaux de transition (TaS2 , TiS2 , MoS2...), constitués de feuil-
lets d’octaèdres MS6 maintenus entre eux par des liaisons faibles
de type Van der Waals et offrant des sites cristallographiques
vacants susceptibles d’accueillir des atomes supplémentaires entre
ces feuillets, en sont des exemples emblématiques. En 1974, Stan-
ley Whittingham démontre dans un premier temps la possibilité
d’y insérer électrochimiquement des ions Ag+ [22], puis transpose
ce travail au lithium. Il met en évidence la bonne réversibilité de
cette réaction d’intercalation du Li+ (figure 2) et le comporte-
ment de solution solide des composés LixTiS2 (0 < x < 1). Logique-
ment, il dépose un brevet concernant l’utilisation du TiS2 comme
électrode positive dans des systèmes réversibles (accumulateurs)
au lithium en 1976 [23] [24].
Par la suite, la société Exxon Entreprises (division batteries)
conçoit et commercialise durant la période 1976-1978 le premier
système rechargeable fonctionnant à température ambiante, des-
tiné à l’alimentation des montres. Il est constitué d’une électrode
positive de TiS2 , d’un électrolyte liquide (LiBPh4 dans 1,3 dioxo-
lane), d’un séparateur microporeux en polyoléfine (Celgard) et
d’un alliage LiAl comme électrode négative. Le prix élevé du TiS2
stœchiométrique et la cyclabilité très modeste obtenue au bout du
Parution : novembre 2016 - Ce document a ete delivre pour le compte de 7200083534 - cea saclay // 132.166.84.222
Ce document a ete delivre pour le compte de 7200083534 - cea saclay // 132.166.84.222
Ce document a ete delivre pour le compte de 7200083534 - cea saclay // 132.166.84.222tiwekacontentpdf_be8620 v1