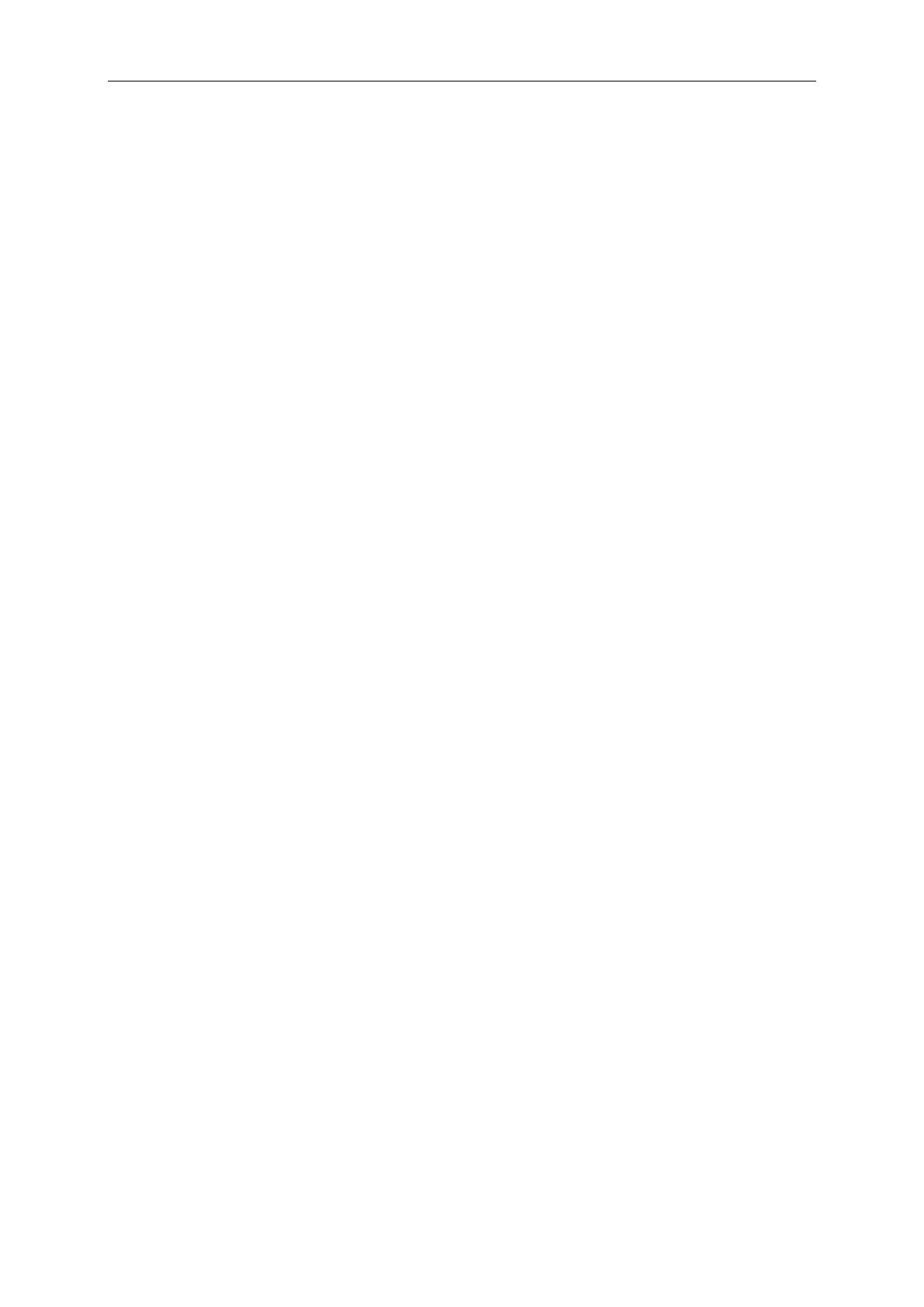
Remerciement
2
Remerciements
mes travaux de thèse (financé Education
Nationale Française) au sein du laboratoire G travailler avec
nombreuses personnes enrichissantes, accessibles et impliquées.
ils ont porté à ce travail. Je voudrais remercier M. Christophe Gorecki pour avoir accepté
Je tiens aussi à remercier M. Bruno Allard et M. Dejan
Vasic, rapporteurs de ce manuscrit, pour leur étude détaillée et pertinente de mes travaux. Je
remercie M. Gonzalo Picun examiné ma thèse, et avoir partagé avec nous sa vision
industrielle intéressante et sa grande expérience.
Je remercie sincèrement M. Jean Christophe Crébier, mon directeur de thèse. Je suis très
avoir eu la chance et le plaisir de travailler avec lui. Tout au long de mes années
non seulement les conseils scientifiques, mais aussi les critiques
importantes. Ses idées et ses solutions intéressantes ont apporté des améliorations
importantes pour mon travail de thèse.
Avec tous mes sentiments, je remercie à Nicolas Rouger, co-encadrant de ma thèse qui
honneur
et la chance de travailler avec toi. Je te remercie pour tes conseils scientifiques tes
encouragements. Merci Nicolas
encouragements. retravailler ensemble.
Je voudrais adresser mes remerciements à tout le personnel du CIME-Nanotech que ai eu
èse, Alexandre Chagoya pour son aide
mais aussi pour avoir toujours été présent afin de résoudre mes problèmes sur le logiciel
Cadence, Irène Pheng en avais besoin.
Je souhaiterais également remercier tous les doctorants et permanents du laboratoire
G2ELab par leurs présence, leurs conseils leurs soutien. Merci entre autre à Raha, Davy,
Clément, Farshid, Melissa, Olivier, Anthony, Xavier, Vincent, Luybomir pour leur
investissement, leur ouverture, leur sympathie et pour nos nombreux échanges riches et
formateurs.
Je souhaiterais également remercier mes amis Vietnamiens de G2Elab (anh Phuong, anh
PJ Sang, anh Trum petit, anh Dinh Quang, Quang anh, Vinh, Quang Linh, Hoang, Dinh Binh,