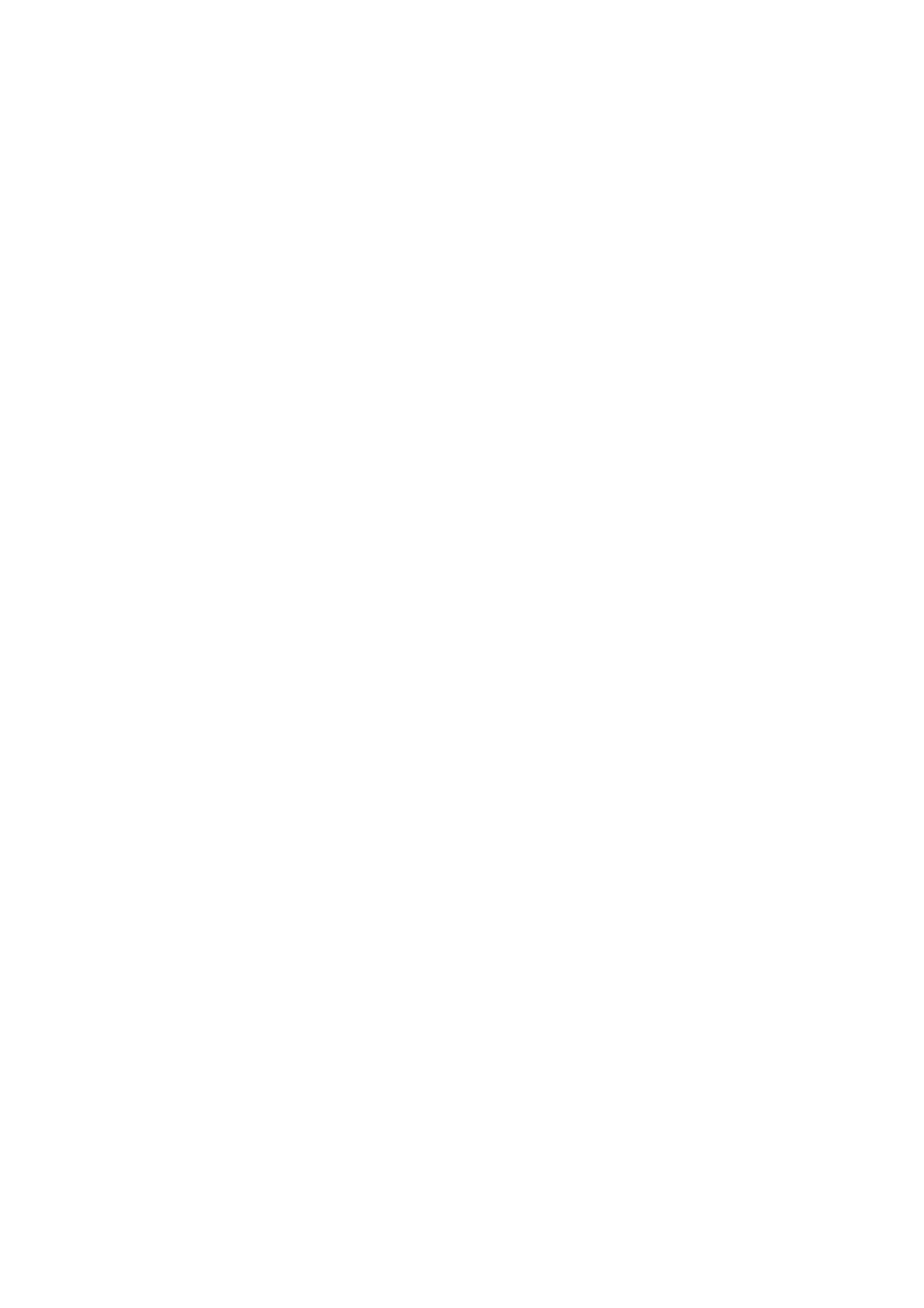
I-3
III.2 EQUIPEMENTS DE CHAUFFAGE, REFROIDISSEMENT, SECHAGE ET
HUMIDIFICATION D’AIR..........................................................................................................III-87
III.2.1 Batteries de chauffage, refroidissement et séchage d’air..........................................III-87
III.2.1.1 Généralités .......................................................................................................III-87
III.2.1.2 Modélisation.....................................................................................................III-89
III.2.2 Humidificateurs .........................................................................................................III-92
III.3 EVAPORATEURS...........................................................................................................III-93
III.3.1 Généralités.................................................................................................................III-93
III.3.1.1 Refroidisseurs de liquides ................................................................................III-93
III.3.1.2 Batteries de refroidissement / séchage à détente directe ..................................III-94
III.3.2 Modélisation ..............................................................................................................III-95
III.3.2.1 Modélisation d’un évaporateur-refroidisseur de liquide ..................................III-95
III.3.2.2 Modélisation d’une batterie à détente directe...................................................III-96
III.4 CONDENSEURS..............................................................................................................III-97
III.4.1 Généralités.................................................................................................................III-97
III.4.1.1 Condenseurs à eau............................................................................................III-97
III.4.1.2 Condenseurs à air .............................................................................................III-98
III.4.1.3 Condenseurs évaporatifs ..................................................................................III-98
III.4.2 Modélisation ..............................................................................................................III-99
III.4.2.1 Condenseur refroidi à eau ................................................................................III-99
III.4.2.2 Condenseurs à air .............................................................................................III-99
III.4.3 Condenseur évaporatif.............................................................................................III-100
III.5 TOURS DE REFROIDISSEMENT..............................................................................III-100
III.5.1 Généralités...............................................................................................................III-100
III.5.2 Exemples de conceptions de tours à contact « direct »............................................III-102
III.5.2.1 Exemples de dispositions sans ventilateur.....................................................III-102
III.5.2.2 Exemples de dispositions avec ventilateur.....................................................III-104
III.5.3 Modélisation des tours à contact direct....................................................................III-106
III.5.4 Tours à contact « indirect » .....................................................................................III-109
III.6 SYSTEMES DE STOCKAGE THERMIQUE ............................................................III-110
III.6.1 Stockage de chaleur sensible ...................................................................................III-110
III.6.1.1 Exemples........................................................................................................III-110
III.6.1.2 Modélisation...................................................................................................III-114
III.6.2 Stockage de chaleur latente .....................................................................................III-117
III.6.2.1 Généralités .....................................................................................................III-117
III.6.2.2 Exemples de systèmes de stockage sous forme de glace................................III-117
III.6.2.3 Modélisation...................................................................................................III-120
III.6.2.4 Identification du coefficient d’échange global du système de stockage.........III-122
III.6.2.5 Stratégies de contrôle du système de stockage de froid .................................III-126
CHAPITRE IV CHAUDIERES................................................................... IV-128
IV.1 GENERALITES............................................................................................................. IV-128
IV.2 MODELISATION.......................................................................................................... IV-131
IV.2.1 Modélisation en marche continue........................................................................... IV-132
IV.2.2 Données par défaut ................................................................................................. IV-137
IV.2.3 Modélisation en marche intermittente .................................................................... IV-138
IV.2.4 Fonctionnement cyclique entre deux niveaux de puissance ................................... IV-139
IV.2.5 Fonctionnement en plusieurs allures et en régime modulant.................................. IV-139
IV.2.6 Chaudières à condensation ..................................................................................... IV-140
IV.2.6.1 Principe de fonctionnement........................................................................... IV-140
IV.2.6.2 Modélisation.................................................................................................. IV-142