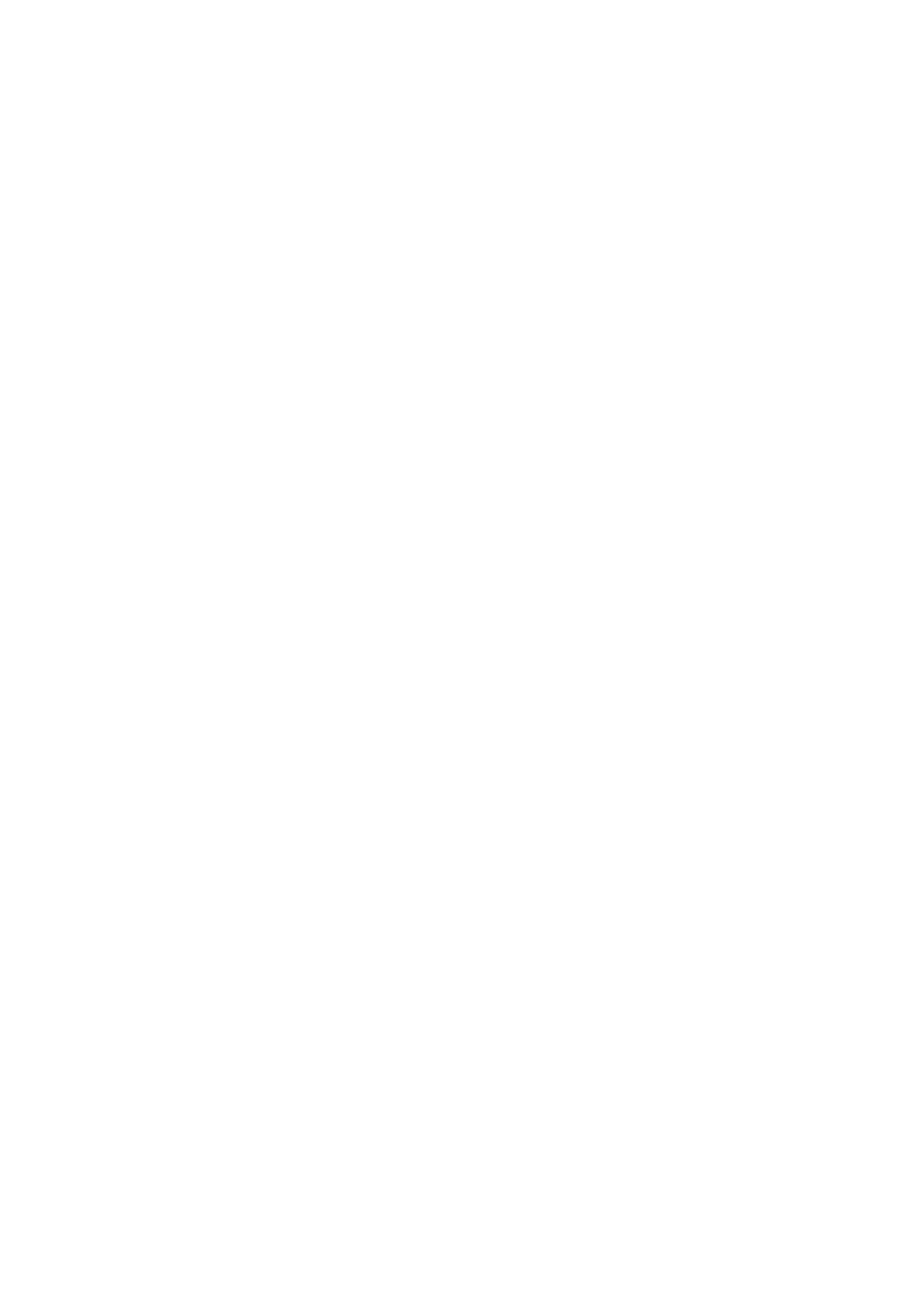
ABSTRACT
Deforestation and firewood shortage are growing problems in many countries of the South.
The energy and fuel shortage in these countries is not only a problem of the rural areas but also
of the densely populated poor margins of medium and large cities. While the traditional types
of fuel (fire wood and charcoal) become more and more exhausted, modern fuels (paraffin,
coal, mineral oil, electricity) are not affordable for the majority of the poor. At the same time,
the generation of organic waste in urban areas poses a growing challenge to the local waste
management system. Organic waste (30-50% of the total waste) is not only a problem because
of its large volume but also because it causes bio-chemical reactions on landfill sites leading to
the formation of landfill gas (methane) and leachates that pollute atmosphere and groundwater.
In rural areas, agricultural residues (straw, rice and coffee husks, coconut and groundnut shells,
bagasse, coir dust, etc.) are generated in large volumes and often not utilised at all. Both urban
and rural organic residues and wastes could be used as alternative domestic fuel if offered in
an acceptable form and at a reasonable price. Briquetting and carbonisation are common
processes to transfer the organic waste into appropriate domestic fuel.
In this study, an appropriate commercial biomass briquetting machine suitable for use in rural
communities was designed and constructed, and the performance evaluation carried out using
sawdust. The physical and combustion properties of the briquette were determined at varying
biomass-binder ratios of 100:15, 100:25, 100:35 and 100:45 using cassava starch as the binding
agent. Both the physical and combustion properties of the briquette were significantly affected
by the binder level (P < 0.05). The optimum biomass-binder ratio on the basis of the
compressed density was attained at the 100:25 blending ratio having a compressed density of
0.7269g/cm3 and a heating value of 27.17MJKg-1 while the optimum blending ratio on the basis
of the heating value was attained at the 100:35 blending ratio with a compressed density of
0.7028g/cm3. It was concluded that the heating values at the optimum biomass-binder ratios
were sufficient to produce heat required for household cooking and small scale industrial
cottage applications. The biomass briquetting machine had a production capacity of about
43kg/hr.
Agro waste manual briquetting machine have been designed and fabricated using locally
available materials. The machine principal parts are made of frame, compaction chamber and
base plate. Compaction chamber contains nine (9) moulding dies each having transmission rod,
piston and ejector. The machine can produce nine (9) briquettes at a time of about 50mm length
and 28mm diameter. The compaction pressure and force was determined to be 17.5 KN/m2
and 215.3N respectively. It is hoped that machine will be very useful for small and medium
scale briquette manufacturers.