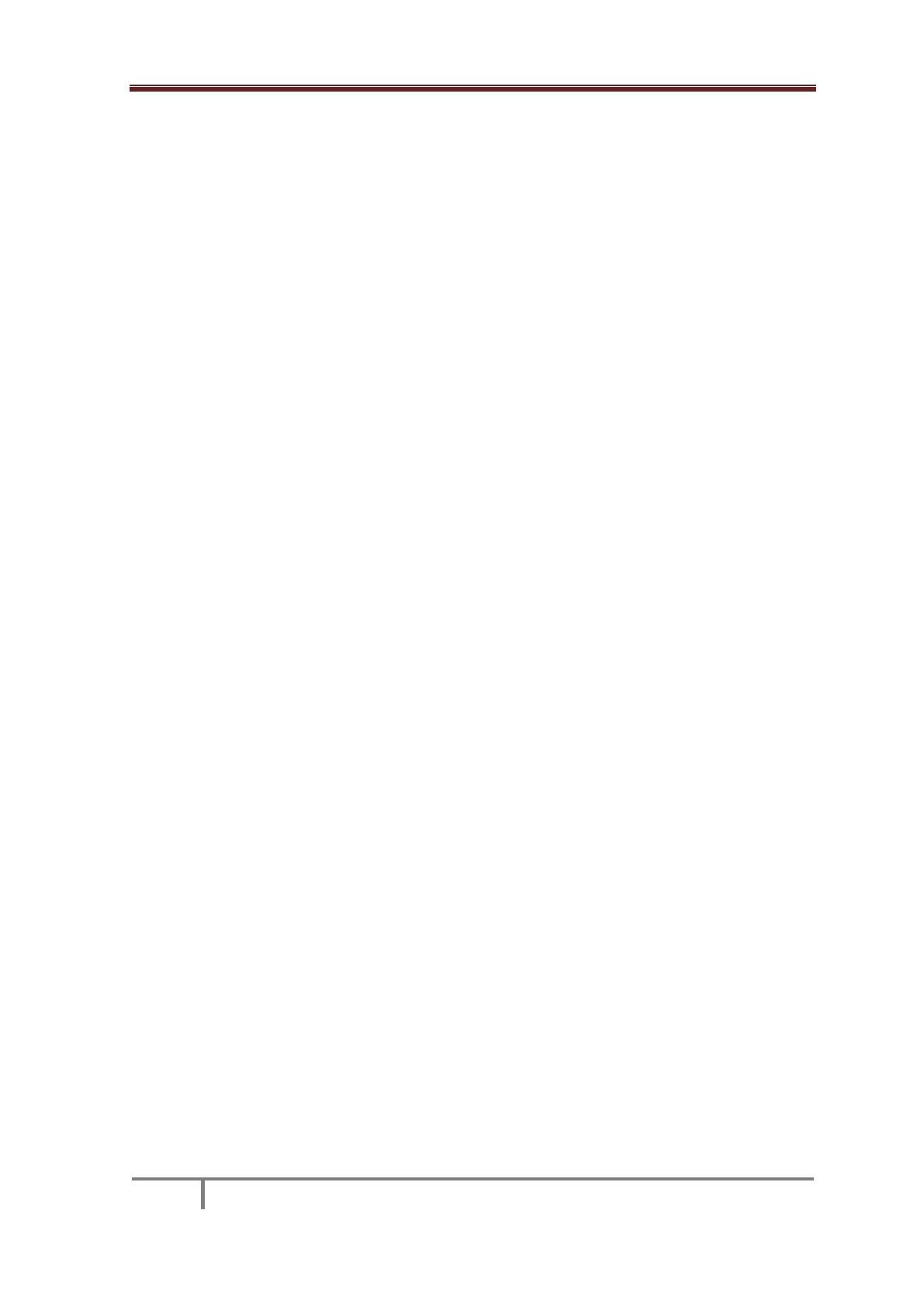
General Introduction
General Introduction
The functioning of electronics can be sensitive to the presence of earth ground and
nearby objects and bodies. For example, a student handling a circuit can unknowingly affect
the circuit’s operation via stray capacitance between the student’s body and the circuit itself.
Sometimes this body capacitance can be a nuisance, such as when encountering unwanted
electrostatic discharge (ESD). On the other hand, capacitive proximity sensors in the form
of touchscreens, touchpads, pushbuttons, and Theremins intentionally utilize body
capacitance. Capacitive proximity sensors (and capacitance measurement devices in general)
are particularly prone to ground loading effects. For instance, a capacitive sensor device
connected to a battery with no other connections to the external world may perform very
differently compared to the same sensor powered by an AC wall outlet and referenced to
mains supply earth. An effective designer of such devices requires an understanding of
appropriate system ground design. A key design skill knows how to visualize and model
parasitic capacitance between the various bodies and objects in the system, such as the local
ground plane, earth ground, capacitor electrodes, and the user. Capacitive proximity sensors
are well suited for educational projects and rapid prototyping. Simple capacitive sensors can
be made with inkjet printing technology or by hand using inexpensive and recycled
materials. Traditionally, however, textbooks and the educational literature pay relatively
little attention to the fact that capacitive proximity sensors can be highly sensitive to ground
loading. Earth ground is largely discussed in the context of power distribution, safety, and
EMI shielding, with little attention to capacitive proximity sensors. This paper presents an
interactive classroom demonstration for directly exploring body capacitance and the effects
of ground loading on a capacitive proximity sensor. The activity was developed to give
students a simple and practical example of how ground loading can affect a real capacitance
measurement. The activity follows established strategies for effective demonstrations, such
as stimulating discussion, challenging an assumption, and asking students to make
predictions on the most probable outcome. For the demonstration, the class is presented with
a hand-held LCR meter connected to a pair of homemade capacitive sensor electrodes
composed of two strips of aluminum foil. Students compare the sensor’s performance for
two system ground configurations. In one case the LCR meter is battery powered, and in the
second case, the LCR meter is plugged into a three prong wall outlet. This experiment