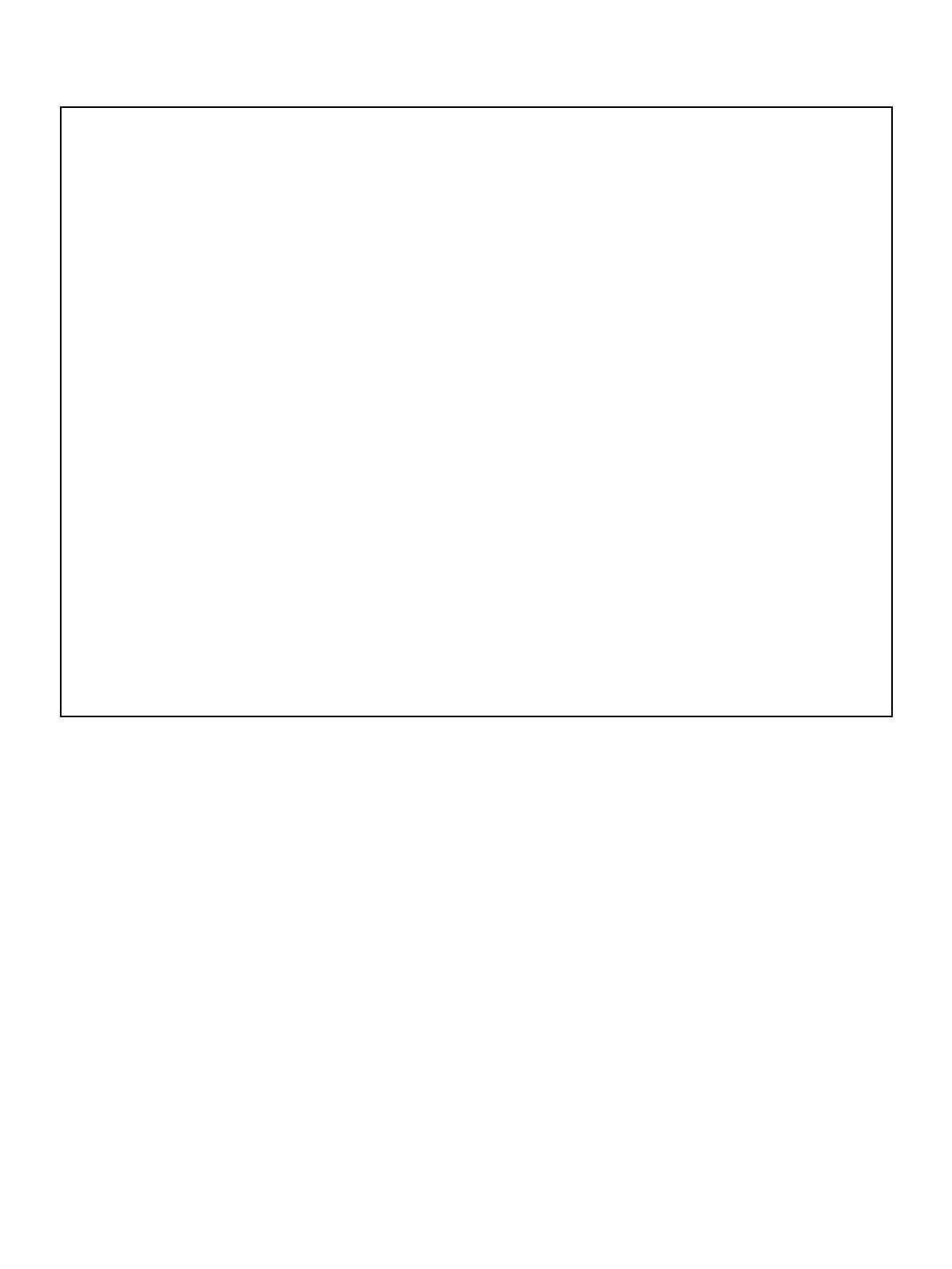
P2D model using orthogonal collocation methods. These tech-
niques can improve the computational efficiency of P2D model to
some extent with acceptable accuracy. However, there are still a
considerable number of equations to be solved to maintain the
integrity of the original model, causing certain calculation and
memory burdens for the vehicular microprocessor.
Analyzing the numerical-method-based simplification tech-
niques, it is clear that the computational burden is ultimately a
matter caused by the model itself. Simplification methods directly
targeting the model structure have been conducted in some re-
searches, among which the single particle (SP) model can be
considered as the most representative one [23]. The SP model de-
scribes each electrode as one spherical particle and neglects the
potential and concentration differences within the electrolyte. Thus
the solid-phase diffusion process in two representative particles
occupies the main computation resource when solving the SP
model. To simplify the solid-phase diffusion, Subramanian et al.
[24] approximated the lithium-ion concentration distribution
along particle radius with a three-parameter polynomial. Han et al.
[25] described the difference between surface and average con-
centrations of the solid particle using several first-order inertia
links. Forman et al. [26] obtained the linearized transfer function of
solid-phase diffusion system based on Pad
e approximation.
However, the linearized transfer function is applicable only to low
frequency range. Further, Sabatier et al. [27] approximated the
original transfer function using the fractional order theory, which
can work well in the full frequency range.
While the SP model can meet the demand for fast computing, it
manifests a poor prediction quality under high C-rates [28]. On the
one hand, this is because the SP model neglects the nonuniform
reaction effect within electrodes. To address this issue, Deng et al.
[29] and Li et al. [30] approximated the reaction flux in the thick-
ness direction of the electrode as a parabolic or cubic polynomial,
and the polynomial coefficients can be effectively obtained without
too much increase in computational complexity. On the other hand,
the electrolyte dynamics is not included in the SP model. Thus,
extended SP models with a simplified electrolyte diffusion process
also have drawn much attention. To simplify the electrolyte diffu-
sion, Rahimian et al. [31] approximated the electrolyte concentra-
tion distribution with one quadratic polynomial in the separator
and two cubic polynomials in the positive and negative electrodes.
Marcicki et al. [32] converted the electrolyte diffusion PDE to a
linearized transfer function using Laplace transformation and Pad
e
approximation. For further achieving a generalized analytical so-
lution, Yuan et al. [33] isolated the electrolyte diffusion PDEs of
both electrodes by introducing modified boundary conditions and
Nomenclature
aspecific surface area [m
1
]
Aelectrode plate area [m
2
]
brugg Bruggeman number
c
e
electrolyte concentration [mol m
3
]
c
0
e
initial electrolyte concentration [mol m
3
]
c
diff
e
difference between c
e
and c
0
e
[mol m
3
]
c
steady
e
electrolyte concentration at steady state [mol m
3
]
c
s
solid phase concentration [mol m
3
]
c
0
s
initial solid phase concentration [mol m
3
]
c
avg
s
average concentration of solid particle [mol m
3
]
c
max
s
maximum solid phase concentration [mol m
3
]
c
surf
s
concentration at solid particle surface [mol m
3
]
c
diff
s
difference between c
surf
s
and c
avg
s
[mol m
3
]
D
e
electrolyte ionic diffusivity [m
2
s
1
]
D
eff
e
effective electrolyte ionic diffusivity [m
2
s
1
]
D
s
solid phase ionic diffusivity [m
2
s
1
]
FFaraday constant [96487 C mol
1
]
i
0
exchange current density [A m
2
]
I
app
applied current [A]
jpore wall flux [mol m
2
s
1
]
j
avg
average pore wall flux [mol m
2
s
1
]
kkinetics reaction rate constant [A m
2.5
mol
1.5
]
lthickness of porous regions [m]
OCP open circuit potential of solid phase [V]
OCP
surf
open circuit potential at particle surface [V]
OCV
cell
battery open circuit voltage [V]
Q
cell
battery capacity [Ah]
Rideal gas constant [8.314 J mol
1
K
1
]
R
ctct
contact resistance [
U
]
R
s
radius of the spherical solid particle [m]
R
SEI
SEI film resistance [
U
m
2
]
SOC
0
initial state of charge for battery
t
0
þ
electrolyte transference number
Tbattery temperature [K]
V
cell
battery terminal voltage [V]
a
a
anodic transfer coefficient
a
c
cathodic transfer coefficient
b
electrolyte activity coefficient
ε
e
volume fraction of electrolyte
ε
s
volume fraction of solid phase
h
ctct
contact resistance overpotential [V]
h
e
electrolyte overpotential [V]
h
e;con
electrolyte diffusion overpotential [V]
h
e;ohm
electrolyte ohmic overpotential [V]
h
kin
kinetics reaction overpotential [V]
h
sum
kin
sum reaction overpotential of two electrodes [V]
h
SEI
SEI film ohmic overpotential [V]
h
sum
SEI
sum SEI film overpotential of two electrodes [V]
q
lithium-ion stoichiometric number in solid phase
k
e
electrolyte ionic conductivity [S m
1
]
k
eff
e
effective electrolyte ionic conductivity [S m
1
]
k
eff
D
effective ionic diffusion conductivity [S m
1
]
s
s
solid phase conductivity [S m
1
]
s
eff
s
effective solid phase conductivity [S m
1
]
4
e
electrolyte potential [V]
4
s
solid phase potential [V]
Subscripts
isubstitution of n,sep or p
nnegative electrode
n=cnegative-electrode/current-collector interface
ppositive electrode
p=cpositive-electrode/current-collector interface
sep separator
C. Li, N. Cui, C. Wang et al. Energy 221 (2021) 119662
2