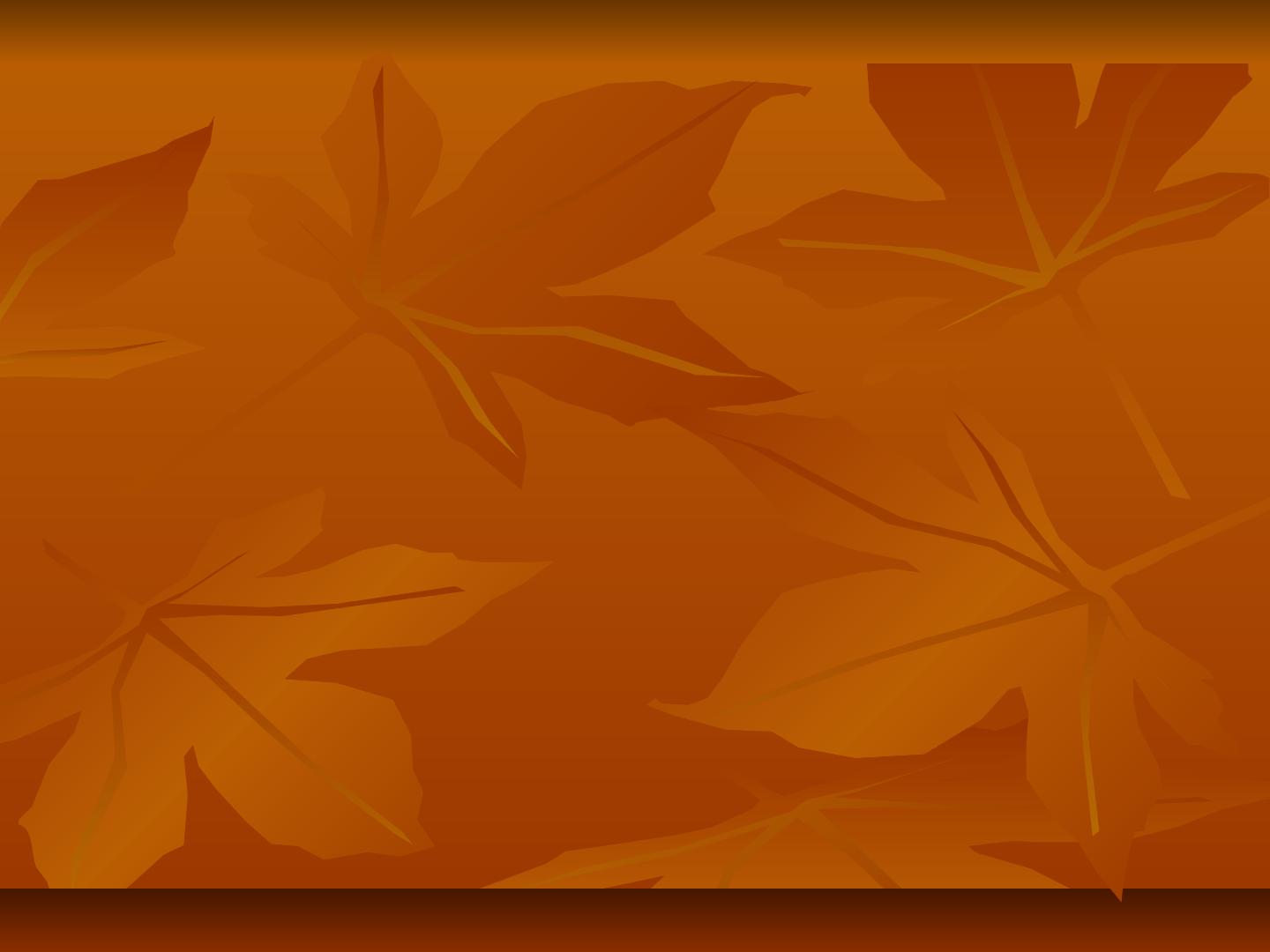
To strike the
To strike the electric arc
electric arc, the electrode is brought into contact
, the electrode is brought into contact
with the workpiece in a short sweeping motion and then pulled
with the workpiece in a short sweeping motion and then pulled
away slightly.
away slightly.
This initiates the arc and thus the melting of the workpiece
This initiates the arc and thus the melting of the workpiece
and the consumable electrode, and causes droplets of the
and the consumable electrode, and causes droplets of the
electrode to be passed from the electrode to the weld.
electrode to be passed from the electrode to the weld.
The heat produced by the arc melts the base metal, the
The heat produced by the arc melts the base metal, the
electrode core rod, and the coating.
electrode core rod, and the coating.
As the molten metal droplets are transferred across the arc and
As the molten metal droplets are transferred across the arc and
into the molten weld puddle, they are shielded from the
into the molten weld puddle, they are shielded from the
atmosphere by the gases produced from the decomposition of
atmosphere by the gases produced from the decomposition of
the flux coating. The molten slag floats to the top of the weld
the flux coating. The molten slag floats to the top of the weld
puddle where it protects the weld metal from the atmosphere
puddle where it protects the weld metal from the atmosphere
during solidification
during solidification