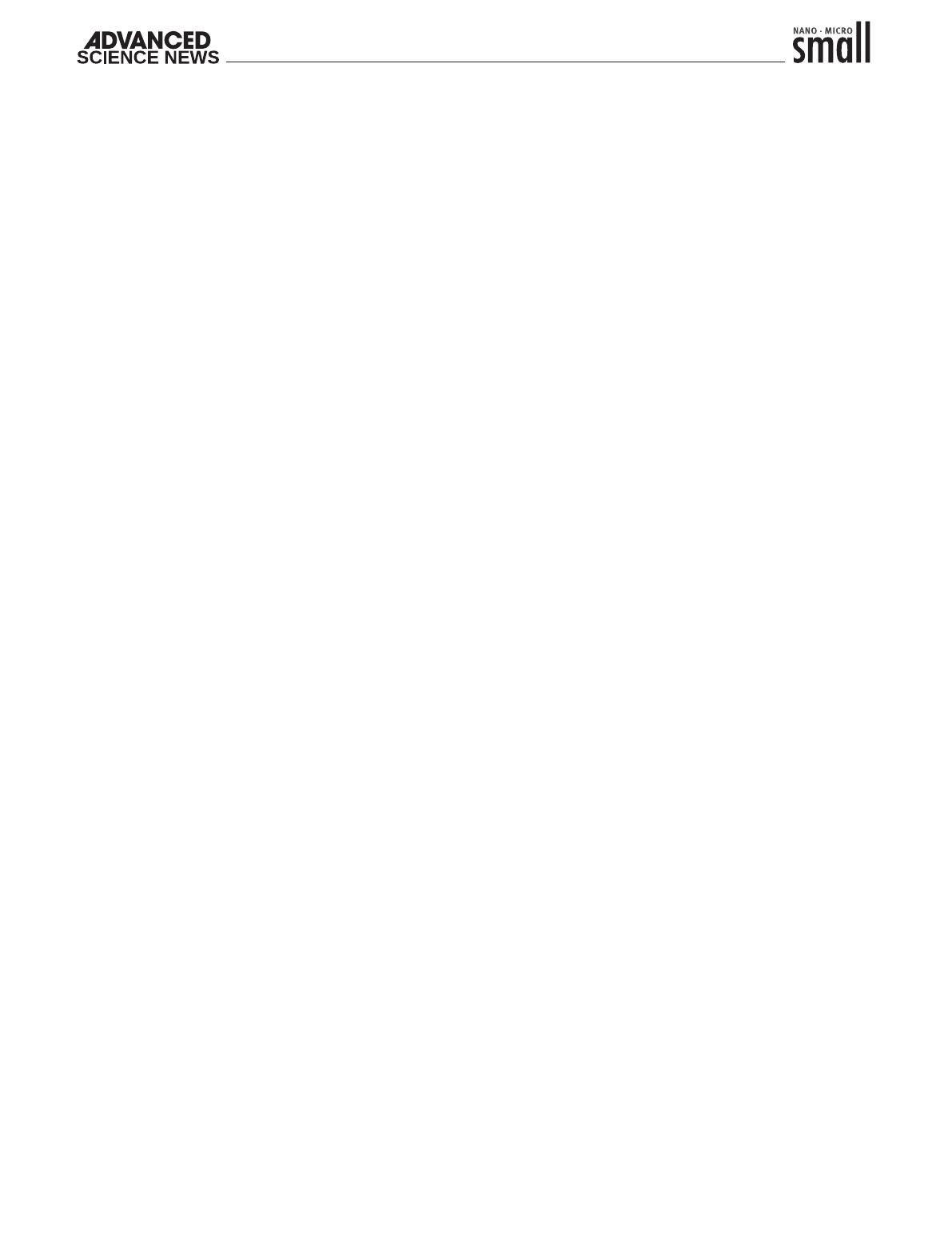
2100510 (2 of 10)
www.advancedsciencenews.com
© Wiley-VCH GmbH
www.small-journal.com
TMDs for enhanced conductivity and improved water-splitting
performance are of paramount significance for water-splitting
process.
Acknowledged by the large specific surface, good conduc-
tivity, and low weight, carbon nanotubes have been considered
as one of the most attractive substrates to be assembled with
active electrocatalysts to form ecient electrocatalysts.[–]
By combining TMDs with carbon nanotubes (CNTs), the con-
ductivity and electrocatalytic performance have been pro-
moted.[–] However, when assembled with CNTs, the size
of TMDs is hard to be controlled, leading to the loss of the
activity.[]The mismatched ratios of length to diameter between
them make it dicult to achieve and maintain the eective con-
nection, which blocks the mass transport and electron transfer
of the catalysts.[] Therefore, only limited works have reported
the composite consisting of TMDs and CNTs with less attractive
catalytic performance.[–] Furthermore, the polarization eect
between WS and CNTs is rarely mentioned and discussed
before, which hinders the development of the WS-based elec-
trocatalysts. Apparently, to design a novel assembly strategy for
the highly ecient TMDs-CNTs composites, and to study the
catalytic mechanism, are of great importance for the following
research on the TMDs-based catalysts.
Herein, a novel WS/CNTs hollow microsphere with supe-
rior water-splitting catalytic performance has been successfully
synthesized via a spray-drying method. Many D WS layers
have been confined onside the surface of CNTs shell to form a
unique D conductive framework. By the confinement of CNTs
shell, the obtained WS exhibits decreased size and increased
exposed edge sites, both of which promote the electrocatalytic
performance. The overpotential can be optimized to mV
(at mA cm−) for HER and mV (at mA cm−) for OER
in KOH, which surpasses almost all the H-WS based nano-
composites, even some noble metal materials. Benefitting from
the simple procedure, industrial output and the eective force
assembly property, the WS/CNTs composite exhibits excellent
water-splitting performance (.V for mA cm−). The polari-
zation eect between WS and D CNTs networks accelerates the
electronic conductivity, leading to the ecient electrocatalysis,
which is confirmed by electron holography and density func-
tional theory (DFT) calculations. Therefore, our results provide a
guidance for the modification of TMD-based bifunctional water-
splitting catalysts through the polarization boosted strategy.
2. Results and Discussion
The synthesis process of WS nanosheets grown on carbon
nanotube hollow microsphere as illustrated in Figure1a and
Scheme S, Supporting Information. At first, the ammonium
tungstate was dissolved into the mixture of distilled water and
CNTs to form a stable solution. Under the eect of ultrasonic
crushing, the agglomerated CNTs were dispersed, and con-
tinuously stirred for h to acquire a homogeneous suspension.
Afterward, via a facilely forced assembly spray-drying method,
a composite consisting of CNTs shells and tungstate ions has
been obtained. The stable solution was broken up to form uni-
form liquid drops, consisting of tungstate, CNTs, and water.
Under the heat exchange of the hot wind, the water is quickly
evaporated and the CNTs are assembled to form a hollow
sphere, which is ascribed to the low diuse speed of CNTs
inward compared with water molecules and ions outward. By
adding HSO (. ) into NaS, HS has been obtained and
then pumped into the tube furnace to form WS/CNTsHMS
composite. Finally, the hollow microspheres wound by CNTs
are obtained, and the inner and outer interfaces of the balls are
loaded with a large amount of WS. This structure not only
limits the size of WS which is beneficial to acquire more
active sites, but also improves the WS conductivity by the eec-
tive connection between CNTs and WS, both of which promote
the electrocatalysis performance of WS.
The morphology and structure of both CNTsHMS and WS/
CNTsHMS is measured by scanning electron microscopy
(SEM) and transmission electron microscope (TEM). The CNT-
sHMS exhibits a hollow yarn-like structure (Figure Sa, Sup-
porting Information), which is corresponding to the previous
works.[] The microparticle sizes are measured from . to
µm. After calcined at °C, the WS/CNTsHMS- exhibits a
combined feature of yarn-like CNTs hollow shells and D-WS
confined in the twining CNTs (Figure b–d). Under a lower
temperature of °C, WS/CNTsHMS- shows a com-
posite feature of CNTs and D H-WS (Figure Sb,d, Sup-
porting Information). Its size distribution has an average size
of . nm, compared with . nm of WS/CNTsHMS-
(Figure Sb,c, Supporting Information). Under a higher calci-
nation temperature of °C, however, the size of WS reaches
. µm (Figure Sd, Supporting Information). The increased
size of WS makes it dicult to form the uniform hollow
microsphere for the mismatched size of WS and CNTs, leading
to the unsuccessful assembling of WS/CNTsHMS (Figure Sd,
Supporting Information).
As the unique assembling of CNTs and WS exhibits strong
confinement eect,[] the size of WS is obviously decreased
compared with commercial WS, which leads to the increased
active sites of WS (Figure S, Supporting Information).
Figure e–g shows the TEM images of WS/CNTsHMS-.
This structure is prepared via forced assembly method by
D-CNTs and D-WS.The high-angle annular dark field-
scanning transmission electron microscope element mapping
(STEM)-mapping exhibits that the W and S elements mainly
mapped onside the D hexagonal WS layers, while the C ele-
ment dispersed on the surface of CNTsHMS, which confirms
the successful synthesis of WS/CNTsHMS (Figure h–k). To
observe the inside structure of WS/CNTsHMS, a thin slice of
WS/CNTsHMS cut by FIB is shown in Figure S, Supporting
Information. The D WS layers are confined at the CNTs
shell (Figure Sb–d, Supporting Information), which is cor-
responding to the TEM images. Importantly, many layers are
grown inside the CNTs shell (Figure Sd, Supporting Informa-
tion). Supposedly, the tungstate is adsorbed onside the CNTs
via the spray-drying method. During the sulphuration process,
the tungstate gradually transforms into WS and then grows
larger toward every orientation to form WS/CNTsHMS. Fur-
thermore, via almost the same method, other TMDs-based
composites have been successfully prepared including MoS
(Figure S, Supporting Information) and VS (Figure S, Sup-
porting Information), confirming the possible widely applica-
tion for the modification of TMDs. Moreover, the spray-drying
Small 2021,